Bottled water is one of the most widely consumed products in the beverage industry and one of the most demanding in terms of quality. Unlike other industries where water is an auxiliary resource, bottling water is the final product. This means that any change, contamination or imbalance in its physico-chemical and microbiological parameters can directly affect its marketing, consumer perception and, ultimately, public health.
In this context, the legislation in force is particularly strict. At European level, Directive (EU) 2020/2184 on the quality of water intended for human consumption, together with its transposition into national legislation, defines the criteria that water intended for bottling must meet. In addition, depending on its origin and treatment, specific regulations may apply, such as those for natural mineral waters and spring waters, regulated in the case of Spain by Royal Decree 1798/2010.
Requirements include, but are not limited to
- Absence of pathogenic micro-organisms.
- Strict limits for chemical contaminants and treatment by-products.
- Stability of the organoleptic profile (smell, taste, colour).
- Controlled mineral composition, both from a legal and nutritional point of view.
In the light of these requirements, the choice of water treatment technologies becomes a fundamental decision. Each water source, whether groundwater, surface water or mains water, has different characteristics that must be corrected or stabilised by an appropriate treatment line. The bottling industry therefore requires tailor-made solutions that combine operational reliability, regulatory compliance and energy efficiency.
Bottling water treatment: a technological chain dedicated to quality
Depending on the characteristics of the raw water and the type of final product desired, the treatment of water intended for bottling may require the application of different technologies. The most used are:
- Reverse osmosis: Allows the removal of dissolved salts, organic compounds, microorganisms and heavy metals. It is particularly useful when the water is highly mineralised or contains contaminants.
- Degassing: Used to reduce the concentration of gases such as carbon dioxide, dissolved oxygen or hydrogen sulphide, which can affect the chemical stability of the water, its taste and cause problems in packaging.
- Remineralisation: After intensive purification, the mineral profile of the water must be adjusted to meet legal parameters and improve organoleptic characteristics. This process allows the “character” of the bottled water to be customised.
- Filtration and final disinfection: Processes such as microfiltration, ultraviolet light or ozonisation guarantee microbiological stability until the moment of bottling.
The correct sequencing of these technologies, as well as their dimensioning and control, are essential to ensure the consistent quality of bottled water, which consumers take for granted but which requires complex technical work.
Key parameters in the quality of bottled water
The quality control of bottled water requires continuous and accurate monitoring of several parameters. These criteria are defined both by current legislation and by the standards of the sector itself, which aims to guarantee a safe, stable and acceptable final product for the consumer.
The most important parameters are listed below, classified by typology:
1. Physico-chemical parameters:
- pH: Ideally between 6.5 and 8.5. Influences the stability of the water and the corrosiveness of the system.
- Conductivity: Related to the total salt content; low mineralised water should be below 500 μS/cm.
- Turbidity: Visual indicator of the presence of solids; should be less than 1 NTU.
- Colour and odour: should be neutral; any deviation may indicate contamination or decomposition of organic matter.
2. Chemical Parameters:
Total Dissolved Solids (TDS): Related to the taste and classification of the water (low, medium or high mineralisation).
- Specific ions:
- Calcium and magnesium (hardness)
- Sodium and potassium
- Chlorides, sulphates and nitrates (nitrates should be kept < 50 mg/L)
- Heavy metals:
- Iron, manganese, lead, arsenic, cadmium (all in very low or undetectable concentrations).
3. Microbiological Parameters:
- Total, absence of:
- Escherichia coli
- Enterococcus spp.
- Total coliforms
- Total bacteria count at 22 °C and 37 °C within legal limits
4. Others relevant parameters:
- Dissolved oxygen and free CO₂: Can affect the stability and taste of the water, as well as the bottling process.
- TOC (Total Organic Carbon): Indicator of the level of organic matter. Essential to prevent microbial growth.
- Pesticides and disinfection by-products: Must be absent or well below legal limits.
5. Organoleptic and aesthetic parameters:
- Flavour: Must be neutral or characteristic of the type of bottled water (natural mineral, spring…).
- Odour: Nonexistent or pleasant, with no metallic, chlorinated or earthy notes.
Success Story: Food Grade Bottled Water Treatment Plant

3D View RO Plant
As part of its commitment to innovation and providing solutions adapted to critical sectors, J. Huesa Water Technology has designed, manufactured and supplied a high-capacity water treatment plant (36 m³/h) for a company specializing in the bottling of water for human consumption. This installation guarantees safe and stable treatment that complies with the most demanding standards of food regulations and good manufacturing practices.
Hygienic design and compact assembly
The plant has been designed with a compact and hygienic engineering approach and is built on an AISI 316 stainless steel skid with surfaces suitable for contact with food grade water.
This arrangement allows:
- Facilitate plug & play installation in process lines.
- Minimise the risk of cross contamination.
- Optimise preventative maintenance and operational accessibility.
The skid design also favours the integration of instrumentation, control and automation in a compact and robust unit, prepared for industrial environments with high demands on cleanliness and traceability.

Detail clamp valve
Treatment Line
The treatment line implemented by J. Huesa meets a critical need: to obtain water that is microbiologically safe, low in dissolved solids and with a mineral profile that guarantees stability, taste and compliance with regulations.
1. Two stage Reverse Osmosis
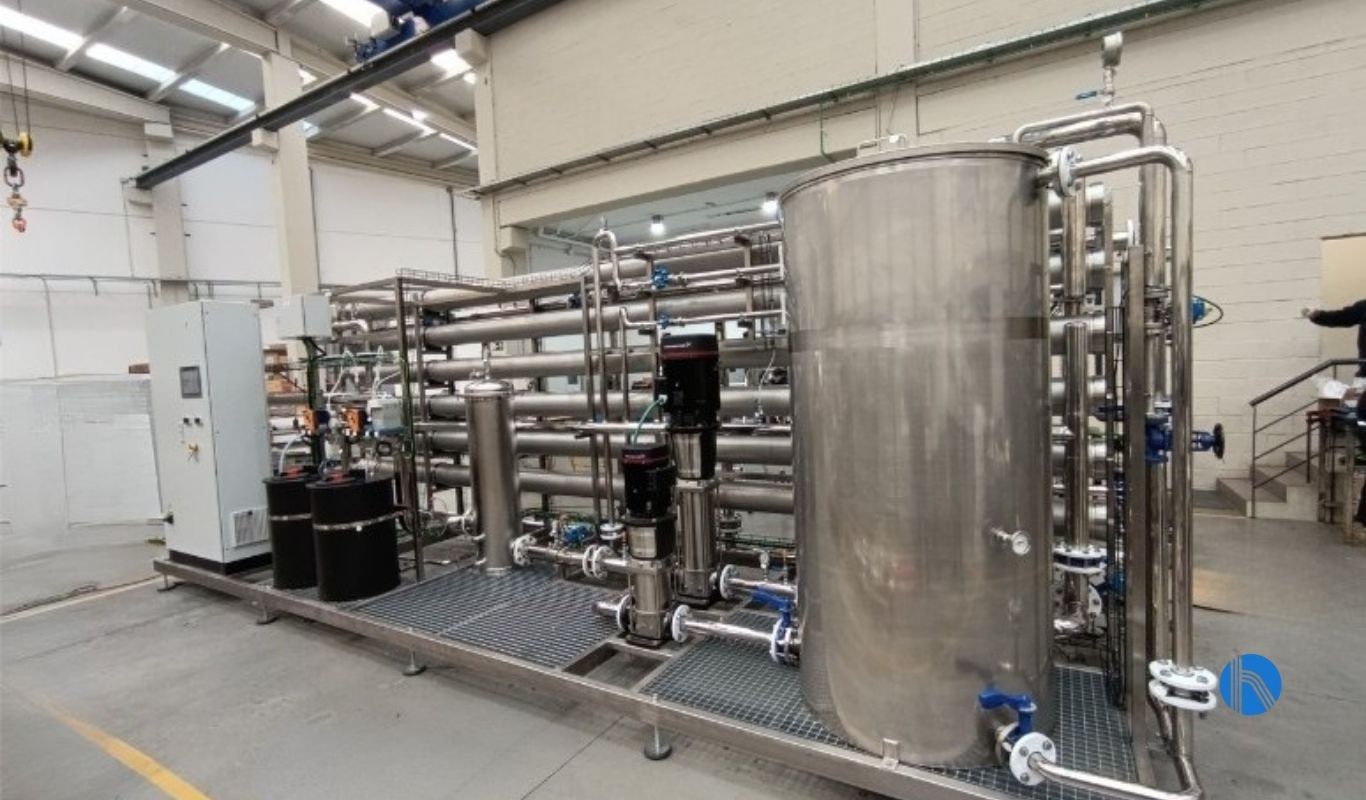
RO plant View
A dual stage reverse osmosis system has been implemented to maximise water recovery and ensure a drastic reduction in Total Dissolved Solids (TDS), micro-organisms, metals and organic compounds.
The double stage allows
- Higher ion rejection efficiency.
- Reduced specific energy consumption.
- Reduced fouling and extended membrane life.
This module is automated with instrumentation to control pressure, conductivity, flow rate and permeate leak detection, with continuous data logging for traceability.
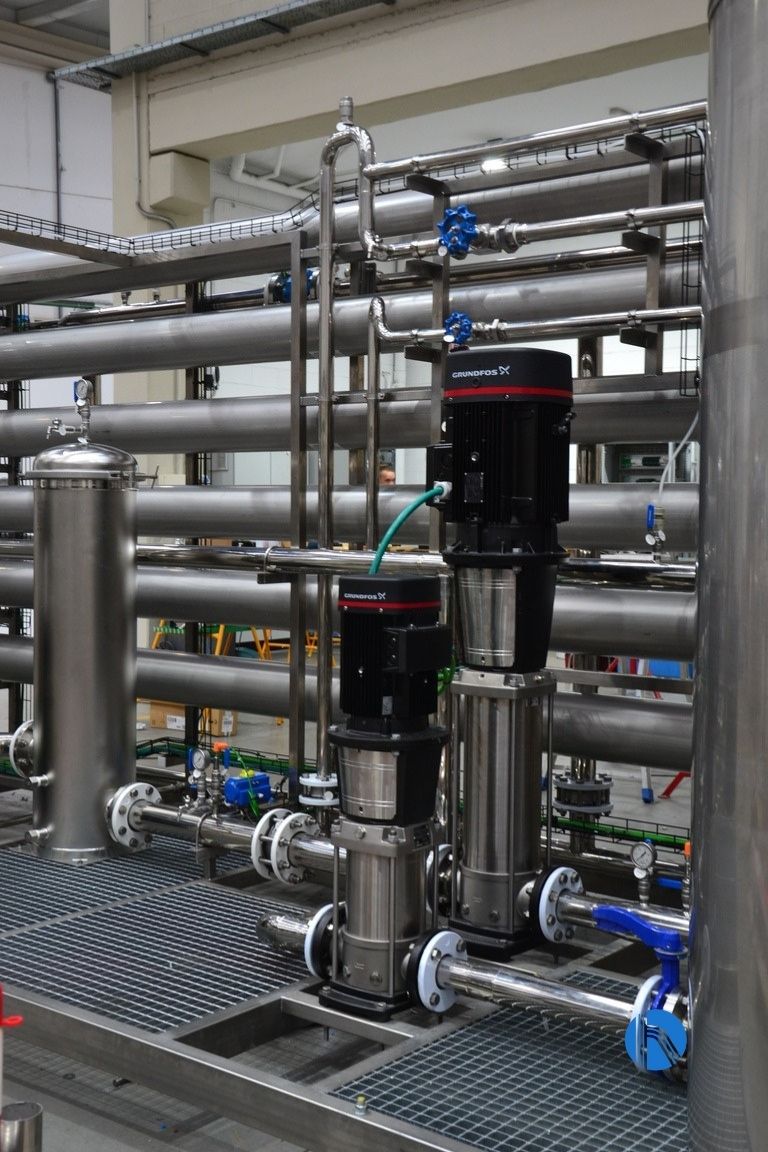
High- and low-pressure pumps detail
2. Desgassing
As an advanced solution for water stabilisation, a membrane contactor degassing system has been integrated as a non-invasive and highly efficient technology to remove dissolved gases such as carbon dioxide (CO₂).
This technology offers:
- High mass transfer efficiency and minimal energy consumption.
- Improved pH control without chemical intervention.
- Prevention of oxidation and limitation of microbiological risk in the line.
The membrane contactors used are made of food-grade certified materials and are integrated into the automatic control system to ensure continuous and safe operation.
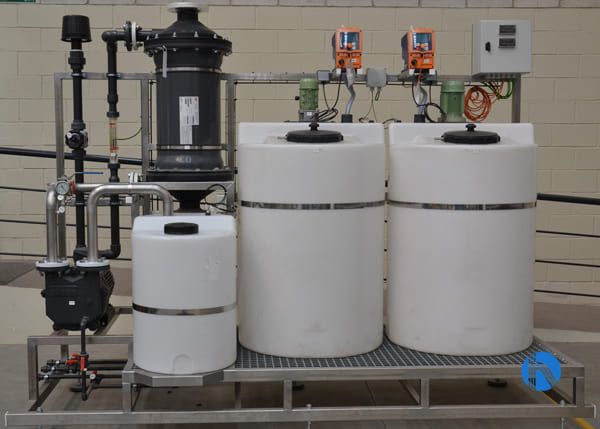
Degassing plant
3. Remineralisation
To meet the regulatory and organoleptic requirements of the final product, a remineralisation module has been incorporated, which allows the presence of calcium, magnesium and other essential minerals to be precisely adjusted, thus guaranteeing
- The classification of the water as drinking water and its correct nutritional labelling.
- Compatibility with the standards of each production batch.
- Improved sensory perception of the bottled water.
The system is designed to work in sync with the requirements of the bottling process, adapting dosing and remineralisation in real time to the quality of the treated water.
Technology and food hygiene at the service of bottled water
This plant is a representative example of J. Huesa Water Technology’s know-how in the design and implementation of advanced water treatment solutions, specifically adapted to the needs of the food and beverage industry, where the safety, stability and traceability of the water are critical factors for the excellence of the final product.
The system combines in an integrated way:
- Hygienic design on a food-grade stainless steel skid, robust, compact and fully accessible for cleaning and preventive maintenance. A standard that meets industry requirements for sanitary safety, corrosion resistance and ease of integration into certified production environments.
- State-of-the-art treatment technologies, such as dual stage reverse osmosis and membrane contactor degassing, that deliver exceptional water quality, resulting in a more natural, safer and competitive end product.
- Advanced automation and intelligent instrumentation systems that provide the plant with fully monitored operation, with critical data logging for traceability, real-time alarms, self-diagnostic capability and direct communication with SCADA or plant MES systems.
Moreover, J. Huesa’s approach is not limited to the supply of equipment: it covers the entire water cycle, from source quality analysis to post-treatment, integrating customised engineering, in-house manufacturing, validation pilots, commissioning and after-sales technical assistance, all carried out by a multidisciplinary team with extensive experience in regulated environments.
A commitment to quality, constant innovation and a vision focused on sustainability make J. Huesa a key ally in ensuring the competitiveness of the food industry in an increasingly demanding regulatory, technical and environmental environment.
With this solution, J. Huesa reaffirms its ability to offer turnkey plants with food standards, ready to respond reliably to the challenges of the global market for beverages and human consumption.