Today we share with you a new case of success executed by J. Huesa for the treatment of industrial
wastewater from the industrial laundry sector, in the specific case of our client who has a wide network of laundries in Spain, Portugal and Andorra.
During their production process, the laundries generate wastewater with similar qualitative qualities,
characterized by a high content of surfactants and organic matter, so, in an initial stage, a pilot project has been carried out to determine an effective treatment that can be applied repeatedly in all their centers.
Thanks to the joint work of the laboratory of J. Huesa J. Huesa and the technical department, a turnkey project has been developed that allows the treatment of wastewater by means of biological treatment by MBR.
Wastewater piloting at laboratory and semi-industrial scale
Once the technical requirements of our client were known, the technical team of J. Huesa’s laboratory
began by carrying out a pilot test in which the direct treatment of the discharge with ultrafiltration
ceramic membranes was tested. During this pilot test, the best applicable physical-chemical pre-treatment was previously analysed, concluding that the best alternative was a coagulation pre-treatment.
Once a test was carried out with the complete treatment line selected (coagulation plus ceramic
ultrafiltration), a rejection of around 10 % was obtained, which was characterised by high values of
organic contamination (always within the law).
In any case, the rejection represented a very high operating cost in the solution proposed, so it was
decided to pilot alternatives that would improve the quality of the treated water and significantly reduce the operating costs for rejection management.
For this reason, a battery of tests was started in pilot plants using MBR, which combines biological
treatment that increases the yields of organic pollution and surfactant elimination and reduces the
operating costs of reject management, with clarification using membranes, taking advantage of the good
results detected in the previous pilot project described above.
The aim of this new treatment is to determine the best technology from a technical and environmental
point of view, comparing clarification with submerged membranes and external tubular membranes,
extending the piloting over a period such that the need for nutrients and sludge production in the
biological reactor can be determined on a full-scale basis.
Thus, both pilot plants are of MBR type, the biological part being identical for both. Clarification is carried out by means of membranes, so that the best possible clarification is guaranteed, using external tubular membranes in one plant and internal microfiltration membranes in the other plant.
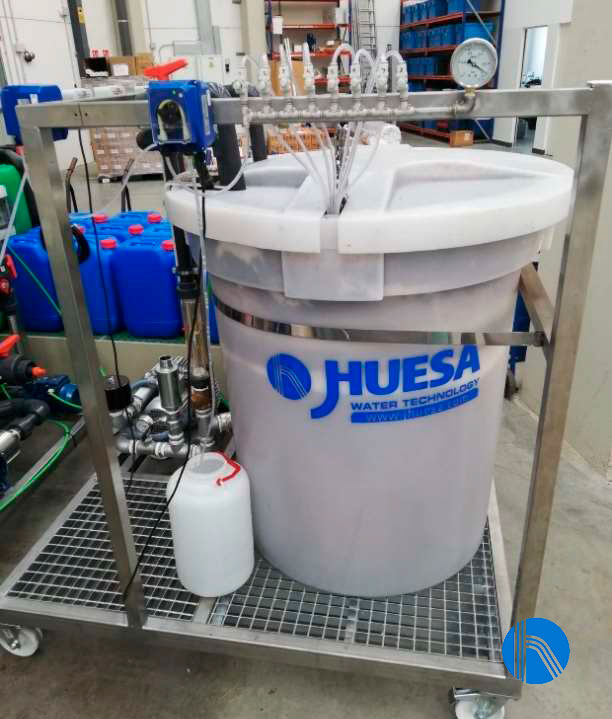
MBR reactor with submerged membranes
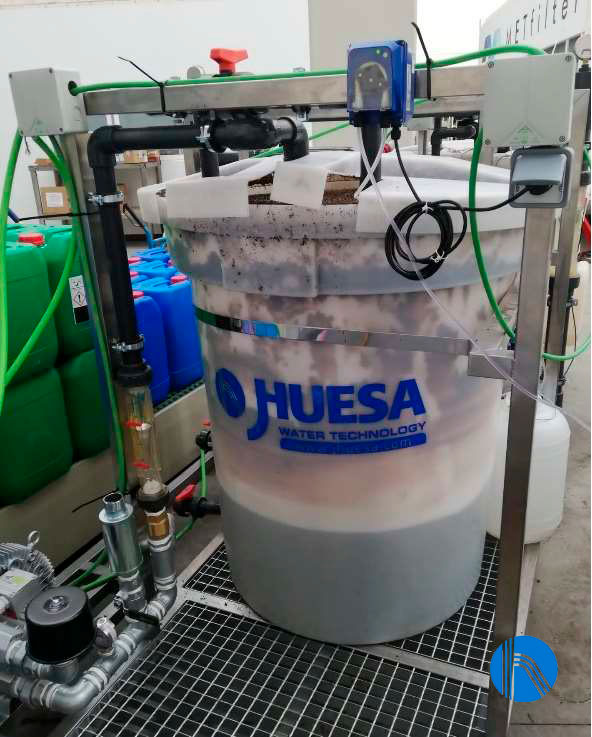
Skid pilot plant MBR external membrane
The main conclusions of this pilot plant are detailed below:
- The quality of water treated with MBR is significantly improved compared to direct treatment
with ultrafiltration membranes. - The analytical quality is very similar for the two membrane alternatives tested in MBR treatment
in terms of COD, BOD5 and surfactants, the success of the treatment being due to the biological
treatment. - The most relevant difference between the two technologies was that the submerged membranes
required three cleanings due to the drastic loss of filtration capacity, while the external
membranes did not require any cleaning during the whole pilot.
Adopted solution
In view of the pilots carried out, the technical department of J. Huesa opted for the design and
customized manufacture, installation and commissioning of a purification line consisting of an MBR with external ultrafiltration membranes and a sludge line.
The analytical design values considered are the average values of the raw water analyses received for
the piloting with a 20% safety margin.
Average design flow (m3 /day) |
150 |
Peak design Flow rate (m3 /h) |
6,25 |
The main components of the system are detailed below.
Pretreatment
Since different types of discharges are identified and all converge in the wastewater treatment plant,
the homogenisation of the characteristics, both in capacity and load, is a key factor for the correct
operation of the treatment design, so the water is pumped from the pumping chamber to the
homogenisation basin, existing at the client’s site.
This basin is equipped with a continuous pH measurement system and pH correction by the addition of
hydrochloric acid.
To reduce the entry of particles in suspension, in a stage prior to its arrival in the biological reactor, and
as an additional screening, the water is pumped to a battery of ring filters equipped with a controller
and automatic cleaning by means of compressed air.
In this type of installation, filtration is carried out in the rings, which act as a strainer that only allows the passage of water and suspended solids with a diameter smaller than the diameter of the pore of the
ring, which has a light passage of 0.200 mm.

Ring filtration system
In our case, the system implemented has a programmer that carries out the washing automatically,
thanks to a set of individual cleaning solenoid valves for each filtration hood, allowing each filter to be
cleaned individually, without having to stop the production of the rest.
The water is then sent by means of a submersible pump to the biological reactor, which is a tank open
at the top, built with prefabricated AISI 316 stainless steel panels and with a gross capacity of 182 m3.
It is equipped with a hydrostatic level sensor that always indicates the height of the water level inside.
MBR (Membrane Biological Reactor) with outer membranes
The discharge of the project requires a drastic removal of the organic load to meet the requirements in
the discharge water. The most economical and efficient alternative, under the assumption of a
biodegradable organic load, is a biological treatment.
In this case, biological treatment with membrane clarification (MBR) has been selected since the water
is ultrafiltered and therefore meets the requirements for discharge into a public watercourse.
Given the great variability in the nature of the discharges, external tubular clarification membranes have
been selected, which are the most robust in MBR type solutions.
The raw water is deficient in nutrients, so the biological reactor has equipment for nutrient preparation
and dosing. It also has an anti-scalant dosing system to prevent the formation of scum.
The oxygen supply necessary for the biological process to be carried out satisfactorily is provided by a
trilotubular rotary piston blower. The air is distributed inside the reactor by means of a grid of diffusers,
which allows us to supply the air by generating a fine bubble that improves the transfer of oxygen. The
diffuser grid has an automatic valve for venting air from the grid.

Grille diffusers at start-up time
Sludge Treatment
A few sludges are also formed inside the reactor, which must be removed and treated. To keep the
bacterial population in the reactor under control, a sludge purge system is implemented.
The purged sludge is sent to a sludge tank where it is kept agitated to avoid settling. Once the sludge
has been homogenized, it is sent to a sludge dewatering unit using filter bags.
The sludge is pumped to the dewatering equipment and conditioned by adding polyelectrolyte to
promote separation. The flocculated sludge enters the dewatering equipment at the top and is
distributed among the six bags located on a frame at the bottom.
A level detector in the inlet tray will warn us of the filling of the sacks, which will be removed by means
of a manual forklift and stored to finish the drying process.
Water at the UF outlet
Instrumentation and control
The treatment plant is equipped with instrumentation and control elements (automatic valves, pressure
switches, pressure transmitters, flow meters, conductivity, and pH meters…) which communicate with
the programmable logic controller, included in the control and command panels, through IO-Link
technology.
Likewise, the panels include a touch screen for the operation and configuration of the plant. J. Huesa’s
Instrumentation and Control team has designed the control panel so that it can be integrated into the
customer’s SCADA system. It also includes a remote-control system.

Overview of the EC