An important leading group in the manufacture and marketing of natural ingredients has culminated its strategic growth programme with the start-up of a new production centre on the Iberian Peninsula. Considering that the production of plant extracts produces wastewater with a high pollutant load (COD > 25,000 mg/l), low biodegradability and a wide range of pH values, it was necessary to treat the wastewater to comply with the limits for discharge into public waterways.
Wastewater piloting at laboratory and semi-industrial scale.
The case study that we present on this occasion is the result of the work carried out by the staff of the technical and R&D&I department and the laboratory of J. Huesa. This sector is characterised by producing wastewater with low biodegradability, which is why after analysing the performance of biological treatment in a pilot plant on a semi-industrial scale, manufactured and piloted for three months at the J. Huesa production centre, the technical team has opted for the design, manufacture and commissioning of a wastewater treatment plant using an MBR with a capacity of 30 m3/day.
In an initial stage of the project, piloting was carried out using two work plants, a semi-industrial plant where work was carried out in the situations closest to the design conditions of the industrial project, and a laboratory plant where different variations on the design were tested.
With this pilot project it was possible to analyse the behaviour of each of these extracts and their mixtures, in a reliable way, before biological treatment, establishing their maximum performance and the most influential variables depending on the nature of the extracts, with the final objective of complying with the limits for discharges into public watercourses and fine-tuning the treatment to be implemented.
Characterisation of the discharge and plant design parameters
Once the pilot test had been carried out, using maximum raw water values for each of the process streams, the following plant design parameters were established to comply with the limits for discharge into watercourses set out in the applicable legislation:
Hourly Peak Flow |
2,5 m3/h |
Average Daily Flow |
30 m3/day |
Hourly Average Flow |
1,25 m3/h |
Working Hours |
24 h/day |
Treated water Use |
Spill |
Treatment Line
As concluded after the pilot test, an MBR (Membrane Biological Reactor) has been chosen, which results from the combination of biological wastewater treatment and microfiltration membrane filtration.
This system is based on the filtration of the wastewater or mixed liquor through the membranes, which is made possible by the vacuum generated by a centrifugal pump. The filtered water is extracted from the system and the sludge is retained or returned to the biological reactor. So, we distinguish between two main parts:
- Biological reactor in which the degradation of organic compounds takes place.
- Membrane module: responsible for carrying out the solid-liquid separation.
There are two basic configurations in which this biological treatment can be presented:
- Submerged membrane: in this configuration the membranes are located inside the biological reactor. This eliminates the need for pumping and takes advantage of the mechanical agitation of the aeration.
- External membrane: the contents of the biological reactor are pumped into the membrane module. The main advantage of this configuration is that the membrane module serves as a container for cleaning.
In this project, given the conditions of the sector, J. Huesa’s technical team has opted for a submerged membrane system.
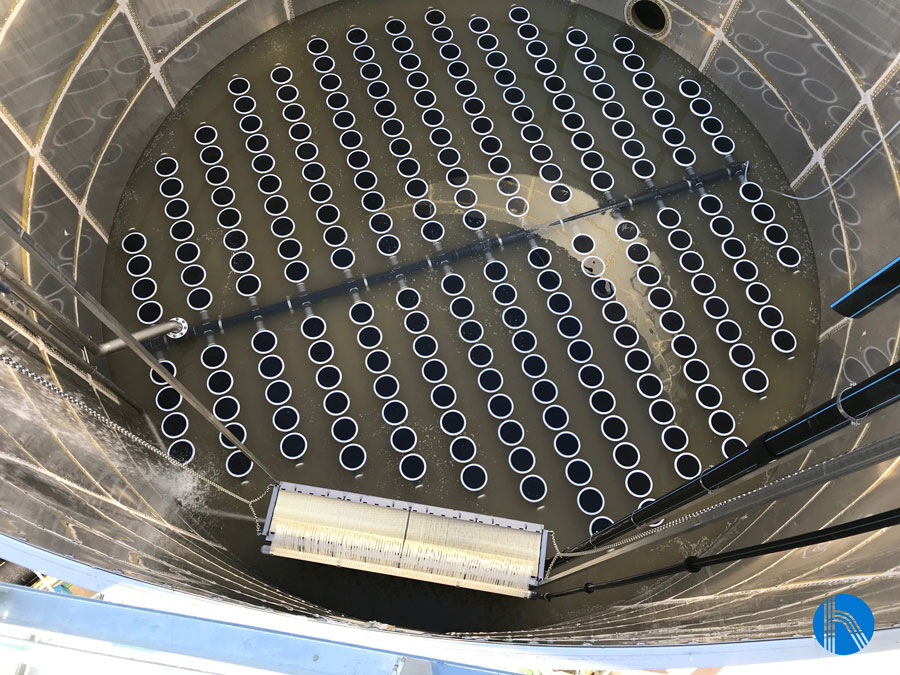
Detail of submerged membranes
Pre-treatment
The different discharge flows from the different areas of the factory are collected in the homogenisation basin, where they pass through a 150 mm wide roughing basket as soon as they enter, which retains all the coarse material that may be dragged along by the discharge flows.
The homogenisation basin is equipped with an agitator whose function is to keep the contents of the basin permanently homogenised, so that when the effluent is transferred to the biological reactor, the effluent has the most homogenous characteristics possible.
In the homogenisation basin itself, several dosages take place, specifically for the adjustment of the pH prior to entering the reactor and for the supply of nutrients, which will provide the necessary nutrients whenever the effluent is being transferred to the reactor.
MBR (Membrane Biological Reactor)
Normally the effluent is transferred to the biological reactor, but in cases where a more complex effluent or an undesired or incompatible effluent can be produced from the factory or treated in the biological reactor, there is a calamity tank that allows effluent to be discharged into the homogenisation basin if the effluent is being transferred to the biological reactor and the agitator continues to homogenise the homogenisation basin.
The biological reactor is a tank open at the top, made of 316L stainless steel with a capacity of 573 m3. It is equipped with a hydrostatic level probe that always indicates the height of the water level inside. It is this level probe that controls the discharge from the homogenisation basin to the reactor, if there is a sufficient level in the basin.
To be able to estimate the behaviour and evolution of the system, a series of lances with instrumentation probes (redox, temperature, pH and dissolved oxygen) are installed in the upper part of the reactor.
At the base of the interior of the reactor, a diffuser grid has been installed, which, thanks to the two blowers located on the outside and working constantly alternating, can introduce the amount of oxygen inside the reactor so that the organic matter inside the reactor can degrade the biological pollutants in the waste. The diffuser grate has an automatic valve for venting air from the grate.

Detail of diffuser grid at the base of the tank
In the same way, inside the reactor, the MBR equipment is located, which is responsible for filtering the mixed liquor from inside the reactor and which, thanks to a self-suction pump, passes the mixed liquor from inside the reactor through the membranes of the MBR, extracting the clarified product.
To extract the permeate correctly and so that the sludge from inside the reactor is not sucked out and sticks to the MBR wall, a small diffuser grill is installed in the lower part of the MBR equipment, which bubbles on the outer layer of the MBR, favouring a correct extraction of the permeate.
When the permeate is extracted from the biological reactor, it is taken to an effluent tank where it is stored and treated with an ozone system before being discharged into a public watercourse.
Sludge treatment
Inside the reactor a series of sludge is also formed, which must be removed and treated. For this reason, one of the lower outlets of the reactor leads to a sludge treatment line by means of a centrifugal decanter.
This sludge operation is programmed in the automaton so that it will be in operation during the programmed hours and whenever necessary (parameters to be defined by the plant personnel).
The dry sludge falls into a collection tank, which must be checked and replaced whenever necessary, and the liquid resulting from the separation inside the centrifugal separator is channelled to the headworks, falling by gravity back into the homogenisation basin.
The entire operation of the system is controlled from the electrical panel, where the automaton that governs the installation is located, as well as the touch screen with which we visualise and parameterise the different operating variables.
Advantages of MBR over other biological treatment systems
The Biological Membrane Reactor with submerged system has a series of advantages over conventional treatments, among which the following stand out:
- They allow operate the planta with higher sludge concentrations, but always in a controlled manner, as an excess can reduce the performance of the membranes.
- Membrane filtration guarantees a high quality of treated water.
- They allow high sludge ages, so that slow-growing species can develop
- Retention of all biomass.
- Lower sludge production.
- The volume of the reactor is smaller than the activated sludge reactor.
With this project, J. Huesa consolidates its position in the Integral Water Cycle market, betting on wastewater treatment.