En esta ocasión compartimos un nuevo caso de éxito de J. Huesa, en el que se ha llevado a cabo el proyecto llave en mano de una planta de reutilización de aguas para una multinacional líder en la producción y suministro de productos de detergencia que, dentro de su propósito estratégico, está avanzando hacia un modelo de vertido cero.
Introducción del sector y del caso que nos ocupa
Antes de avanzar en el proyecto en cuestión, vamos a presentar el contexto del sector en España, donde la producción de productos de limpieza ha crecido considerablemente, impulsada en parte por la pandemia y el aumento de la demanda de desinfectantes y productos de limpieza en los hogares. De esta forma, en 2020, este sector generó un valor aproximado de 2.320 millones de euros, con un incremento del 6% en la producción nacional y un aumento del 16.1% en las exportaciones de estos productos, que alcanzaron los 627 millones de euros.
Además, se estima que aproximadamente 120 empresas españolas se dedican exclusivamente a la fabricación de productos de limpieza para uso doméstico.
Desde el punto de vista del consumo de agua, y en función del tipo de producto de limpieza, se estima que del total del agua que consume la industria, entre el 75 y el 98 % del contenido del producto final está compuesto por agua, por lo que el objetivo del sector es reutilizar el agua para incorporarla en los principales usos que puede tener:
- Proceso productivo (arrastre)
- Torres de refrigeración
- Baldeos
- Riego
Pilotajes y ensayos de laboratorio
En el caso que hoy presentamos, nos encontramos ante un cliente con el que llevamos colaborando varios años. Fruto de esa colaboración ha resultado una simbiosis entre ambas compañías, por la que hemos puesto a disposición de nuestro cliente nuestro Know-How en el tratamiento del agua.
Hay que tener en cuenta que este proyecto viene a completar el tratamiento ya existente en la fábrica. Hace tres años J. Huesa concluyó la instalación de una planta de ultrafiltración tubular cuyo objetivo era eliminar la práctica totalidad de AyG y SS, reduciendo notablemente la DQO de la planta existente.
En una etapa posterior, se llevó a cabo la instalación y puesta en marcha de un evaporador de simple efecto, con una capacidad de 25 m3/día y con un 70-80 % de rendimiento.
Llegar a este punto ha sido factible gracias al trabajo conjunto del equipo técnico de J. Huesa y de nuestro cliente, por el que se han desarrollado una serie de pilotajes y ensayos de laboratorio que nos han permitido ir esgrimiendo cuáles son las tecnologías más adecuadas a desarrollar en cada etapa del proyecto por la que hemos ido avanzando.
Hoy nos vamos a centrar en las plantas de ósmosis inversa instaladas. Previamente a su instalación, se llevó a cabo el diseño y fabricación de una planta piloto semi industrial que se implantó en las instalaciones del cliente in situ, para tratar el permeado de la UF tubular.
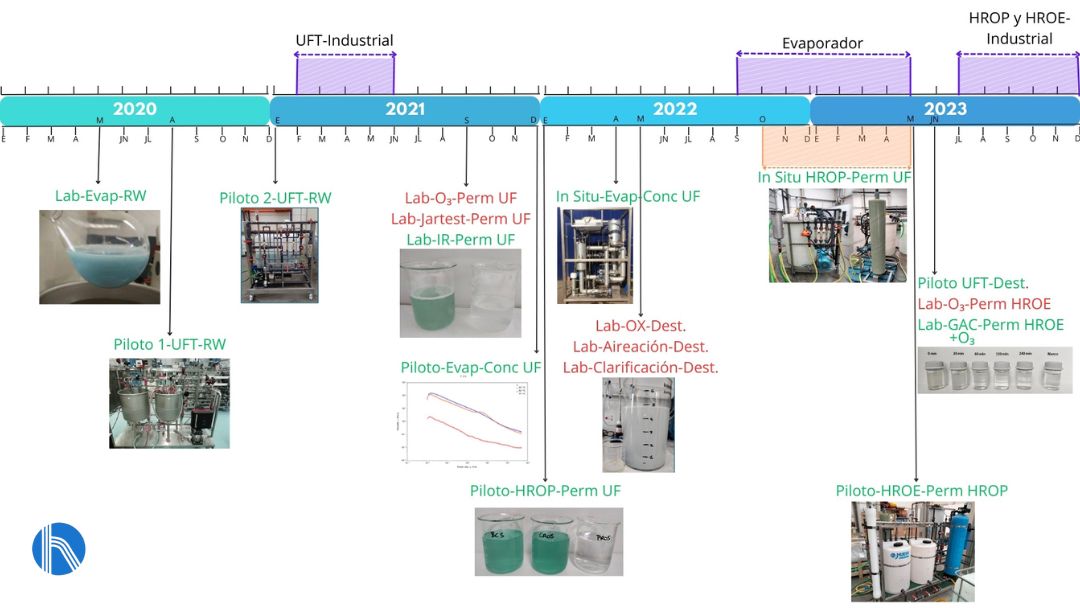
Resumen de pilotajes realizados
Datos y características del agua a tratar
A continuación, se muestra una analítica del agua bruta a tratar:
Parámetro | Unidades | Valor |
---|---|---|
Conductividad | μS/cm | 6.800 |
DQO | mg/L | 8.000 |
SS | mg/L | < 10 |
AyG | mg/L | < 10 |
El objetivo de la planta es establecer una solución global al tratamiento terciario de un agua de
permeado de una ultrafiltración tubular.
Solución adoptada
Planta de Ósmosis Inversa de membrana plana
Nuestra propuesta pretende alcanzar el objetivo de disminuir la salinidad y la DQO del agua a tratar, para lo que se establecieron los siguientes datos de diseño de la planta:
Datos de diseño | |
---|---|
Caudal de aporte RO | 3 m³/h |
Caudal de rechazo RO | 0,75 m³/h |
Caudal de permeado RO | 2,25 m³/h |
Conversión | 75% |
Horas de trabajo | 20 h/día |
Caudal diario | 60 m³/día |
Acumulación agua bruta | 60 m³ |
Acumulación agua permeada | 60 m³ |
Acumulación rechazo | Balsa evaporador |
En una etapa inicial, el agua procedente del tanque de acumulación del permeado de la ultrafiltración tubular se somete a una filtración con dos filtros de anillas de 10 micras y posteriormente a una serie de dosificaciones químicas que dependerán de las necesidades del agua de entrada.
Tras ser sometida a un tratamiento de químicos, el agua se introduce en dos filtros de tela de 5 micras colocados en paralelo.
Los filtros de tela se emplean para retener partículas sólidas antes de entrar en la membrana de ósmosis inversa.
En una etapa previa a la ósmosis inversa, el permeado de UF se puede introducir en un intercambiador de calor multitubular con flujo contra-corriente. El objetivo de este proceso es mejorar el rendimiento de la planta de ósmosis inversa. En los pilotajes realizados se demostró que el aumento de la temperatura mejoraba el rendimiento de la planta de ósmosis inversa.
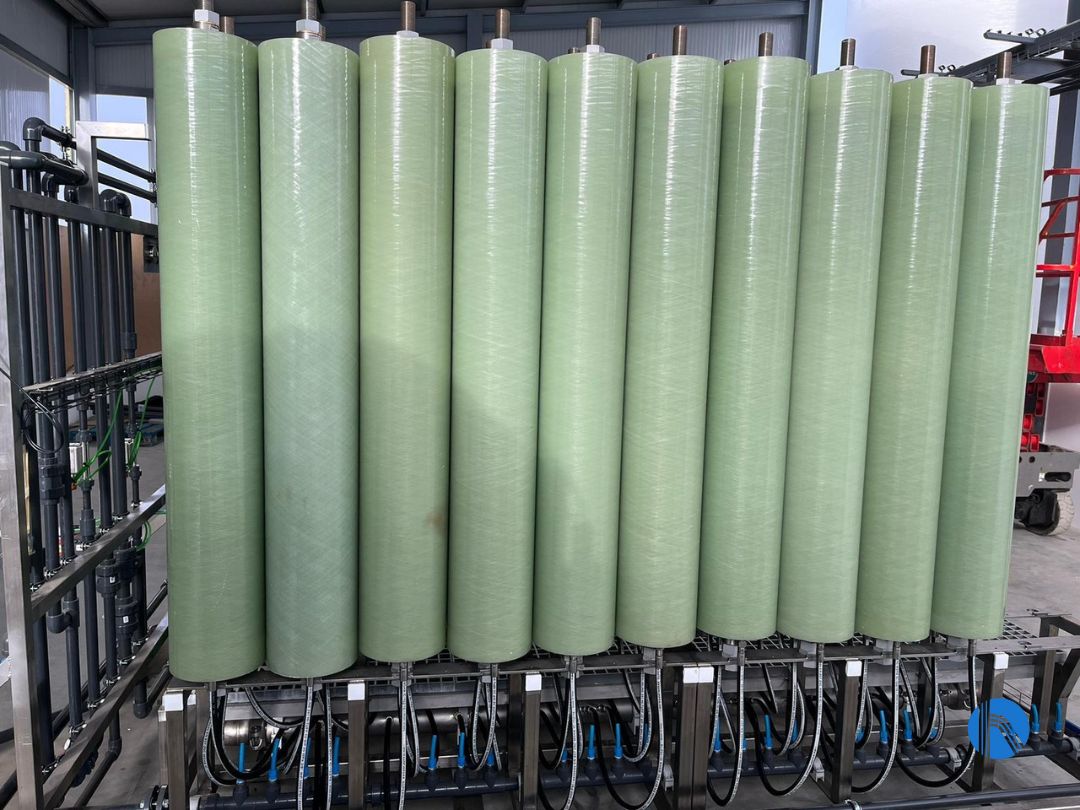
Vista módulos de membrana plana
En esta planta se utilizan módulos de ósmosis inversa de membrana plana. Los módulos de membrana plana permiten reducir la contaminación y la incrustación que son comunes en otros módulos de ósmosis inversa.
Estos módulos están diseñados para trabajar con:
- Agua altamente contaminada
- Altas presiones
La temperatura de trabajo del módulo es de 30ºC- 35ºC de forma continua, siendo la temperatura máxima durante la limpieza de 40ºC.
La planta está provista de un sistema de limpieza de membranas (flushing), que es de secuencia automática y, además, lleva un sistema de limpieza química de forma manual, tipo CIP.
Planta de Ósmosis Inversa de membrana en espiral
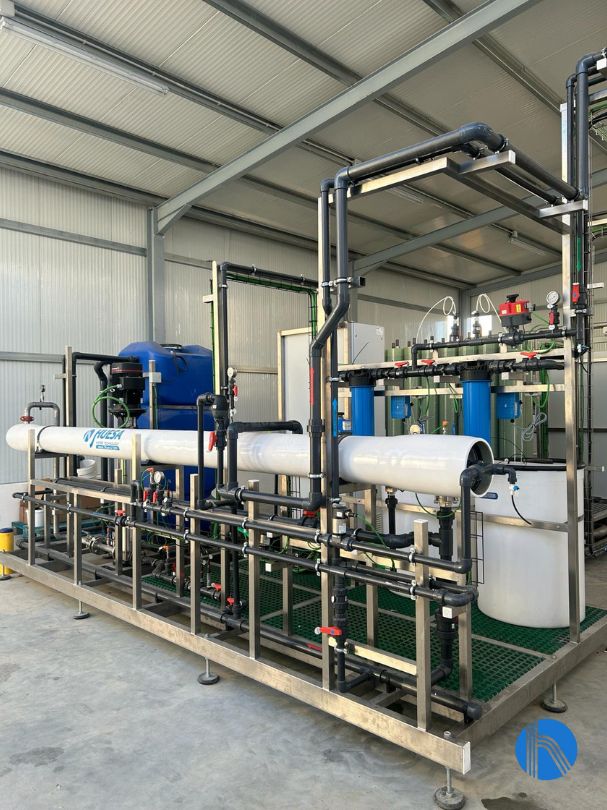
Vista planta ósmosis inversa en espiral
Datos de diseño | |
---|---|
Caudal de aporte RO | 3 m³/h |
Caudal de rechazo RO | 0,9 m³/h |
Caudal de permeado RO | 2,1 m³/h |
Conversión | 70% |
Horas de trabajo | 20 h/día |
Caudal diario | 60 m³/día |
Acumulación agua bruta | 60 m³ |
Acumulación agua permeada | 60 m³ |
Acumulación rechazo | Balsa evaporador |
El objetivo de esta planta de tratamiento de aguas es establecer una solución global al tratamiento terciario de un agua de permeado de una osmosis de platos planos, de forma que se obtenga agua exenta de salinidad y contaminación orgánica.
La instalación irá provista de membranas de configuración espiral, construidas en poliamida y especiales para aguas salobres de hasta 8000 ppm y con la característica de trabajar a baja presión.
Estas membranas tienen una gran resistencia química, pues pueden trabajar en un rango de pH de 2 a 13, lo que les confiere una gran facilidad de lavado y recuperación, al admitir gran variedad de productos químicos de lavado.
Para los iones monovalentes la selectividad de separación varía entre el 90% y el 95 %. Para los iones divalentes la selectividad es superior al 98 % y para los coloides minerales u orgánicos, bacterias y virus esta selectividad alcanza el 99,9 %
Las membranas irán montadas en carcasas de presión, fabricadas en PRFV bobinado.
En una etapa inicial, el agua se somete a una dosificación de antiincrustante y biocida. A continuación, se introduce en dos portacartuchos, que en su interior contienen un filtro de cartucho con un grado de filtración de 5 micras. Los filtros de cartuchos se emplean para retener partículas sólidas antes de entrar en la membrana de ósmosis inversa.
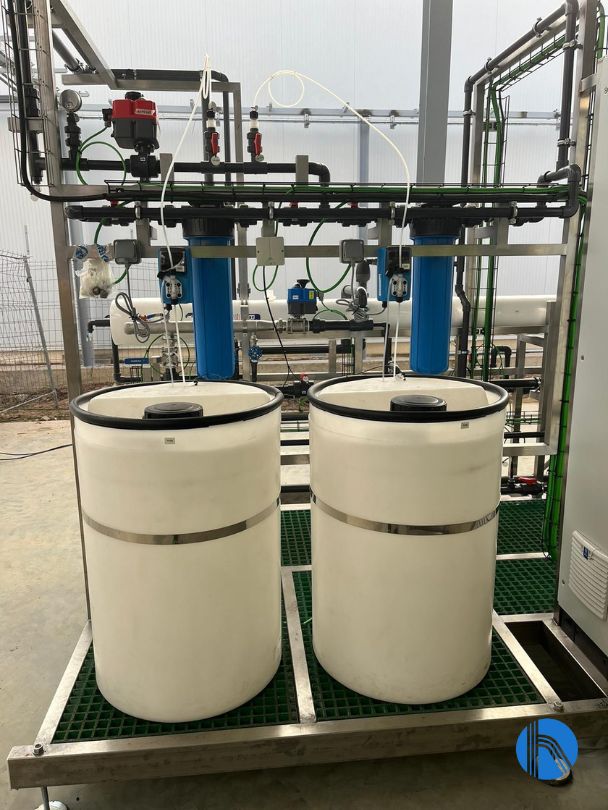
Vista sistema de dosificación y filtros de cartucho
La saturación de los filtros se puede detectar de dos formas distintas, bien a partir de la diferencia de presión marcada por los manómetros colocados a la entrada y a la salida de este o bien de forma automática, ya que también se disponen de transmisores de presión en la entrada y salida de los filtros, indicando la diferencia de presión en pantalla.
La presión osmótica es una característica física que depende de la concentración de cada solución y que crece en función de ésta. El agua que tratar tiene una presión osmótica natural de aproximadamente 0,7 kg/cm². Esta presión natural más la presión neta necesaria para la obtención del caudal de producción (que se denomina presión de operación) se obtiene mediante el empleo de una bomba centrífuga vertical de alta presión en acero inoxidable AISI 316.
Esta es una de las partes más importantes del equipo, ya que es el único elemento mecánico en movimiento permanente, el cual determina el mantenimiento del equipo y el coste del metro cúbico de agua tratada en función de la energía eléctrica consumida.
La instalación va equipada con bombas centrífugas:
- Las bombas de mayor potencia son la de suministro a la planta de osmosis.
- Las bombas de menor potencia instalada son las que se utilizarán para el barrido y el lavado químico de las membranas (flushing – CIP RO)
Instrumentación y control
Todo el funcionamiento de cada una de las plantas de ósmosis inversa se controla desde el cuadro eléctrico, donde se encuentra el autómata que gobierna la instalación, así como la pantalla táctil con la que visualizamos y parametrizamos las diferentes variables de operación.
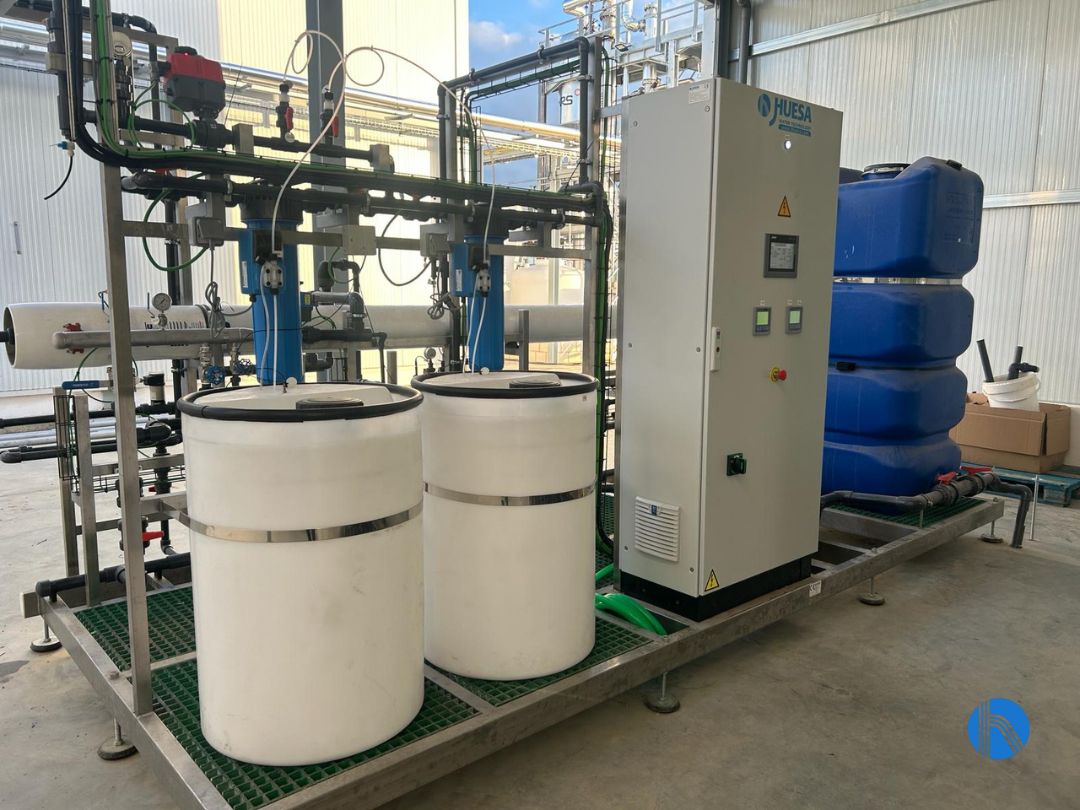
Vista CE de la planta de ósmosis inversa en espiral
Conclusiones
Este caso de éxito evidencia cómo las soluciones de tratamiento de agua avanzadas no solo resuelven desafíos técnicos, sino que también generan beneficios ambientales, económicos y sociales, alineándose con los objetivos de sostenibilidad de nuestros clientes.
A continuación, detallamos algunas de las conclusiones que se pueden extraer de este proyecto:
1. Optimización del uso de recursos hídricos
2. Cumplimiento de las normativas ambientales: el sistema cumple con los estándares de calidad del agua exigidos por las normativas nacionales e internacionales, garantizando un efluente tratado apto para usos no potables en procesos productivos.
3. Adaptación a la economía circular: Este proyecto representa un paso hacia la sostenibilidad, integrando principios de economía circular en el ciclo productivo de la industria de detergencia mediante la reducción de residuos líquidos.
4. Beneficios operativos: La solución implementada mejora la eficiencia operativa y reduce la dependencia de recursos externos, posicionando a la industria como un referente en sostenibilidad dentro de su sector.
5. Escalabilidad y replicabilidad: El diseño modular del sistema permite su escalabilidad para futuras ampliaciones, siendo replicable en otras plantas de producción del sector industrial con necesidades similares.