Introducción del caso que nos ocupa
En la industria de fragancias y aromas moleculares, la calidad del agua juega un papel fundamental tanto en los procesos productivos como en el funcionamiento de las calderas industriales. La presencia de impurezas, sales disueltas y contaminantes microbiológicos puede afectar directamente a la calidad del producto final y a la eficiencia operativa de los equipos.
En este caso, se ha diseñado una planta de tratamiento de agua mediante ósmosis inversa para una fábrica ubicada en Andalucía, con el objetivo de garantizar un agua de alta pureza tanto para el proceso productivo como para la generación de vapor en calderas.
Una industria que ha creado una nueva línea de producción en el centro fabril ubicado en Andalucía.
Calidad del agua de aporte a calderas industriales
El agua de alimentación de calderas debe cumplir con ciertos parámetros para evitar problemas de corrosión e incrustaciones. Según la norma UNE-EN 12953-10:2003, se establecen los siguientes requisitos:
- Dureza total: Idealmente cero o muy baja, medida en mg/L de CaCO₃, para prevenir la formación de incrustaciones.
- pH: Mantener un rango óptimo entre 10.5 y 11.5, con un máximo permisible de 12.5, para minimizar la corrosión y optimizar la eficacia de los tratamientos químicos.
- Oxígeno disuelto: Debe ser eliminado o reducido a niveles mínimos (<0.007 mg/L) para prevenir la corrosión.
- Conductividad: Controlada para evitar acumulación de sales que puedan afectar el rendimiento de la caldera.
Calidad del agua en la producción de fragancias
En la industria de fragancias, la pureza del agua es crucial para garantizar la calidad del producto final. Se recomienda utilizar agua desionizada o, preferiblemente, purificada.
Los parámetros a tener en cuenta son:
- Carga microbiológica: El agua debe tener una carga microbiológica baja para evitar la contaminación del producto.
- Ausencia de iones y aditivos: El agua no debe contener iones o aditivos que puedan interferir en la formulación de las fragancias.
- Reducción de materia orgánica: La presencia de materia orgánica puede alterar la estabilidad de las fragancias, por lo que se requiere un proceso de eliminación eficiente.
Solución adoptada
Tras el estudio de las características del agua bruta de aporte al sistema y teniendo en cuenta las necesidades específicas de nuestro cliente, el equipo técnico de J. Huesa ha optado por el diseño y fabricación a medida de una planta de tratamiento de agua compuesta por los siguientes subprocesos:
– Pretratamiento mediante un sistema de filtración previa mediante lechos bicapa, encargado de llevar a cabo la eliminación de los sólidos más gruesos que puedan estar presente en la corriente de agua que se alimenta al sistema.
– Ósmosis Inversa estará compuesto por dos etapas, la primera de ellas, compuesta por 3
tubos de 4 membranas y, la segunda, compuesto por 2 tubos de 4 membranas.
Como base del diseño de la planta que nos ocupa se han tomado los siguientes datos:
Datos de diseño | |
---|---|
Caudal de aporte | 28,6 m³/h |
Caudal punta (contralavado) | 50,3 m³/h |
Caudal permeado | 20 m³/h |
Caudal permeado diario | 400 m³/día |
Horas de trabajo | 20 h/día |
Pretratamiento
El agua que se quiere tratar se bombeará a través de un filtro bicapa a baja velocidad y de lavado automático, donde se retendrán los sólidos en suspensión que pueda traer dicha agua.
Este filtro tiene un sistema de válvulas independientes para realizar la operación de lavado del filtro. La maniobra sobre la valvulería se realiza de manera automática.
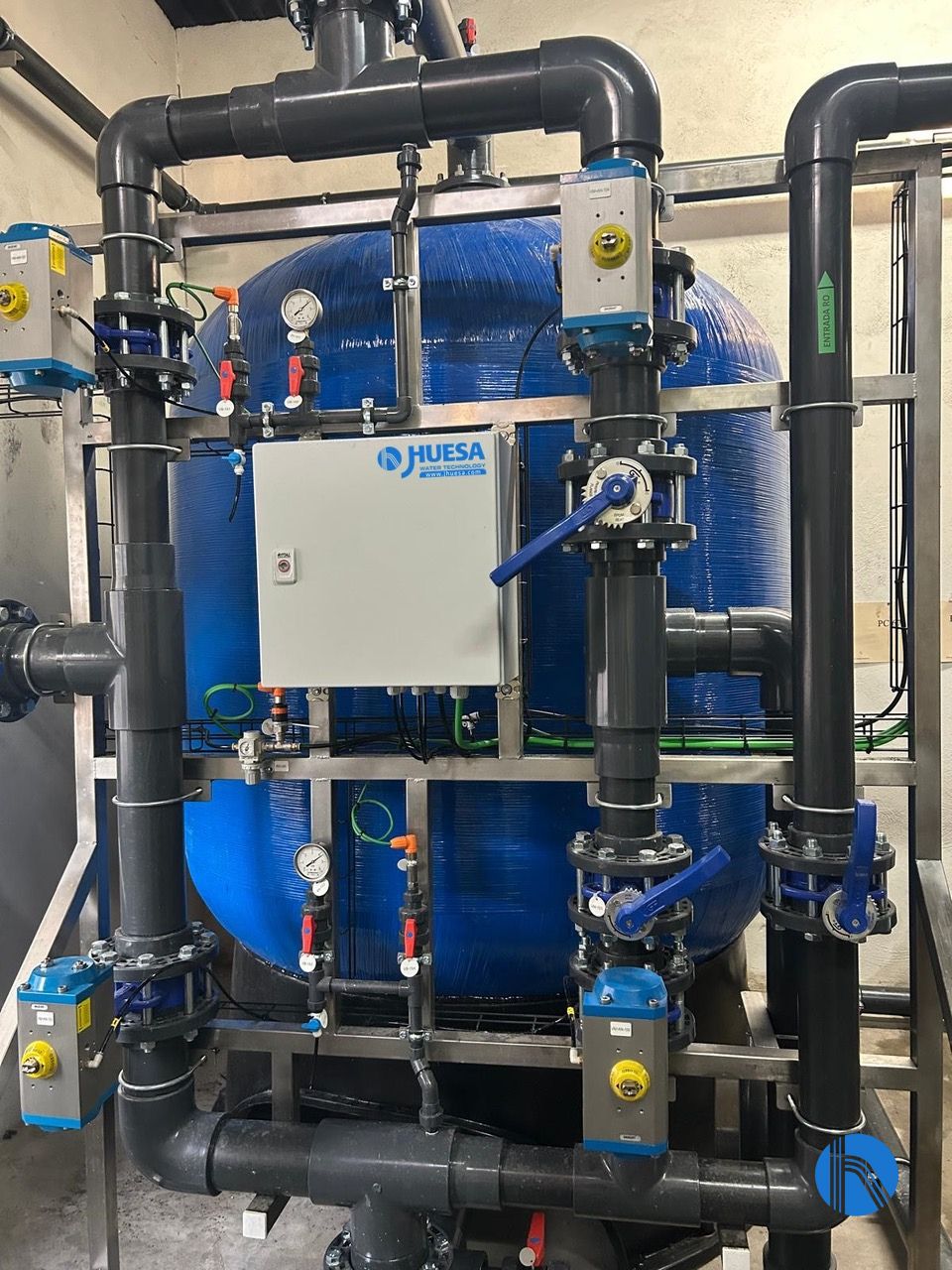
Filtro bicapa
Este proceso de limpieza consta de dos etapas:
Contravalado: Para la limpieza de la carga, se emplea la misma agua de entrada, se introduce en el filtro por la parte inferior, y en cantidad suficiente para remover la carga de manera vigorosa, pero sin que esta se llegue a acumular en la parte superior. El agua empleada se manda a desagüe.
Asentamiento: Tras el contralavado, es necesario que la carga se prepare para la vuelta al servicio del filtro. Para ello se emplea esta fase de asentamiento, donde la misma agua se introduce por la parte superior y, al igual que pasaba con el contralavado, la salida se redirige hacia el desagüe, produciendo un efecto de “apriete de la carga”.
Este proceso de limpieza se realiza por tiempo y/o por máxima pérdida de presión en la línea de agua entre la entrada y salida al mismo. A continuación, el agua se somete a una dosificación de antiincrustante y secuestrante. Posteriormente, el agua así tratada, será alimentada a un prefiltro de seguridad, previo a su entrada al sistema de ósmosis inversa, que servirá como afino de aquellos pequeños sólidos que no hayan podido ser retenidos por el filtro bicapa.
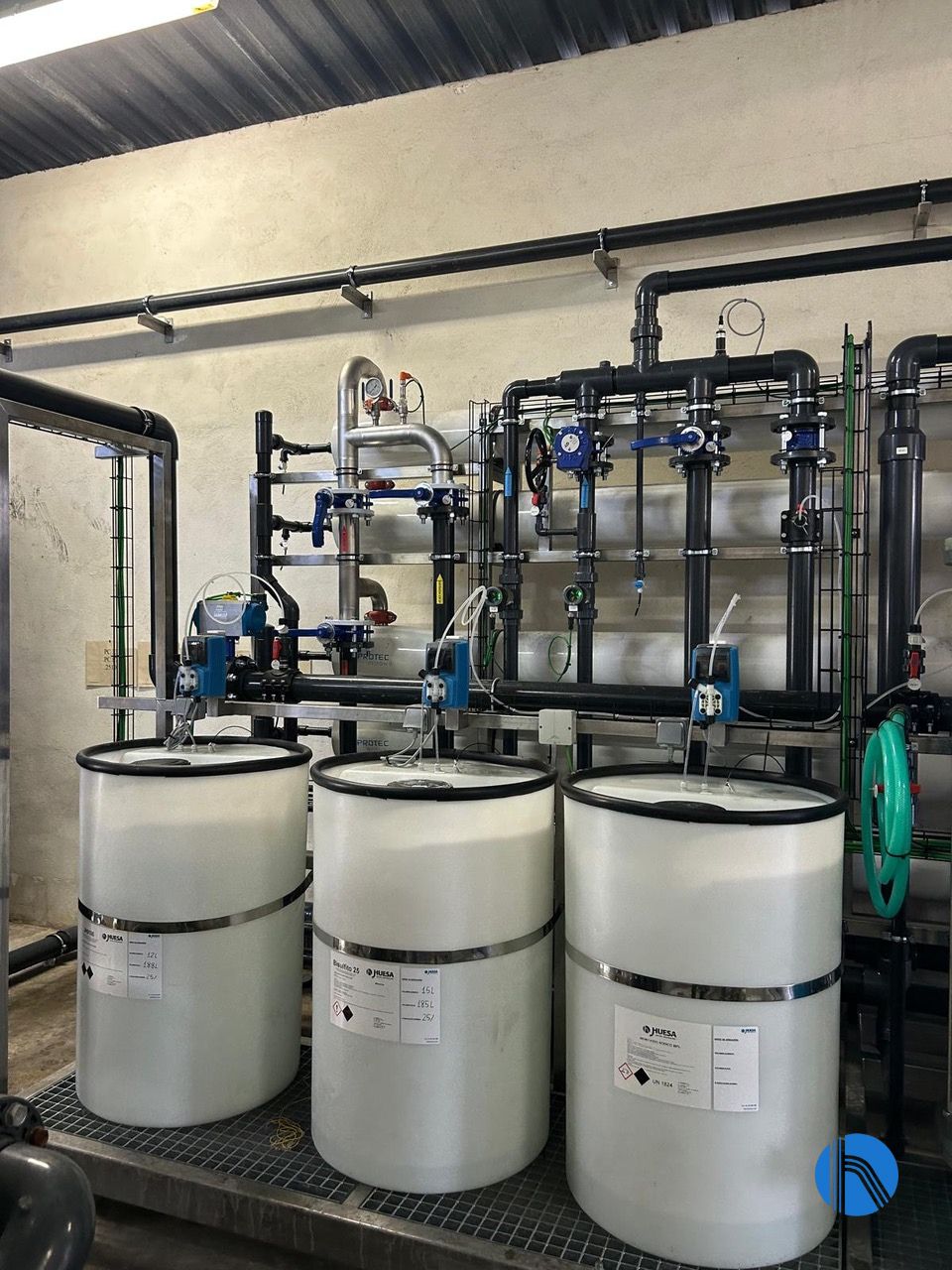
Sistema de dosificación
El filtro de seguridad consta de cartuchos recambiables de 5 micras, cuyo control se realiza mediante diferencia de presión controlada por dos manómetros colocados a la entrada y salida de este. La frecuencia de recambio de los cartuchos dependerá del contenido en coloides del agua.
Ósmosis Inversa
El sistema de ósmosis inversa está compuesto por dos etapas, la primera de ellas, compuesta por 3 tubos de 4 membranas y, la segunda, compuesto por 2 tubos de 4 membranas. Con el objetivo de tener controlado los flujos y presión dentro del sistema, se dotará al equipo con caudalímetros y transmisores de presión. Así mismo, se llevará a cabo la instalación de un sistema de CIP/Flushing, encargado de realizar el lavado de las membranas de forma periódica.
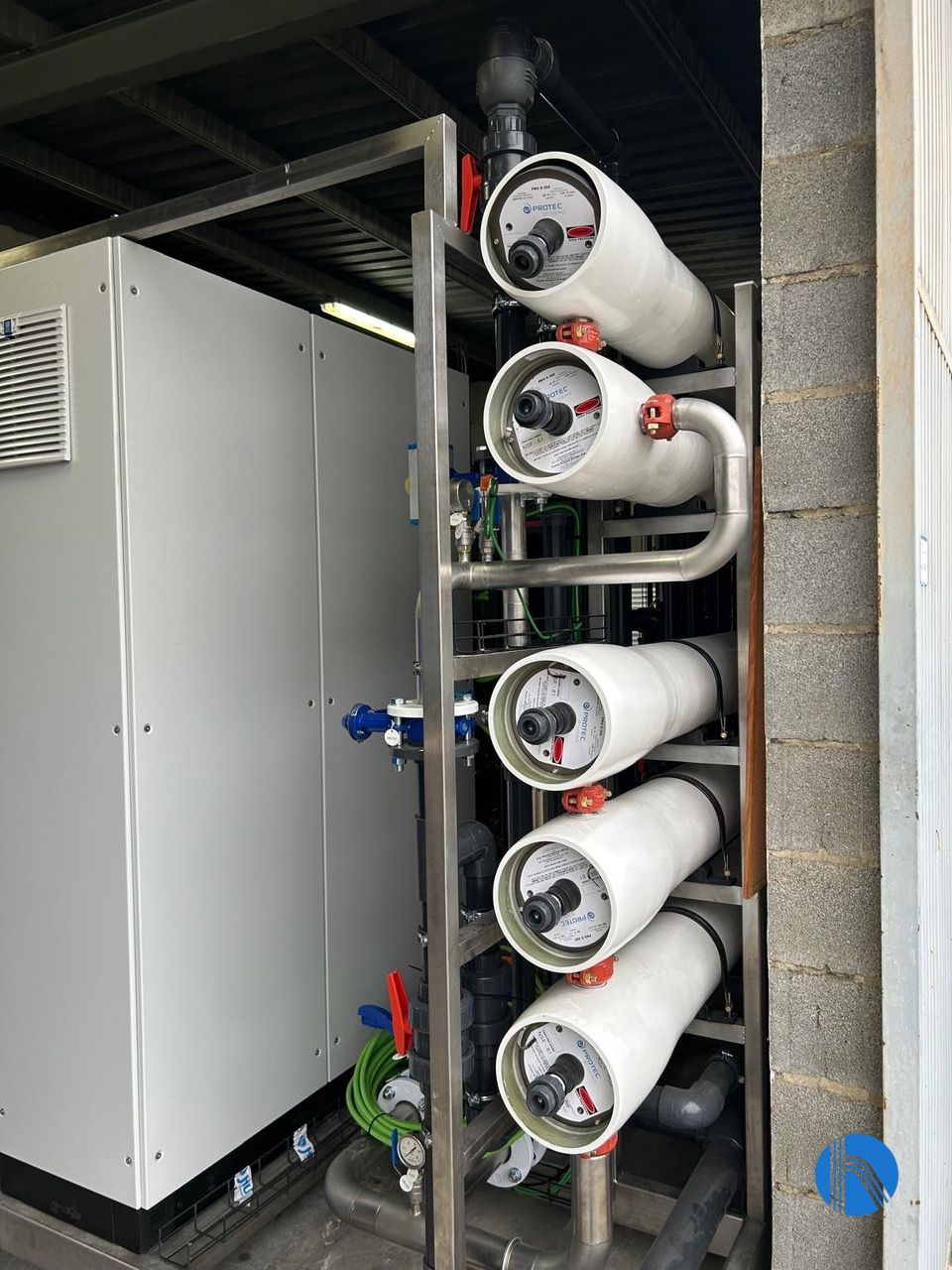
Vista dos pasos de la Ósmosis Inversa
Los elementos fundamentales para llevar a cabo la ósmosis inversa son:
Bomba de alta presión: La presión osmótica es una característica física que depende de la concentración de cada solución y que crece en función de ésta. El agua para tratar tiene una presión osmótica natural de aproximadamente 0,7 kg/cm². Esta presión natural más la presión neta necesaria para la obtención del caudal de producción (que se denomina presión de operación) se obtiene mediante el empleo de una bomba centrífuga vertical de alta presión en acero inoxidable AISI 316.
Esta es una de las partes más importantes del equipo, ya que es el único elemento mecánico en movimiento permanente, el cual determina el mantenimiento del equipo y el coste del metro cúbico de agua tratada en función de la energía eléctrica consumida.
Membranas de ósmosis inversa: La instalación está provista de membranas de configuración espiral, construidas en poliamida y especiales para aguas salobres de hasta 8000 ppm y con la característica de trabajar a baja presión.
Estas membranas tienen una gran resistencia química, pues pueden trabajar en un rango de pH de 2 a 13, lo que les confiere una gran facilidad de lavado y recuperación, al admitir gran variedad de productos químicos de lavado. Las membranas irán montadas en carcasas de presión, fabricadas en PRFV bobinado.
Equipo de lavado de membranas: Todas las instalaciones de membranas con el tiempo sufren un ensuciamiento, dependiendo en más o menos del pretratamiento instalado, necesitándose efectuar de una a dos limpiezas por año. Dado el tamaño del equipo ofertado, se ha incluido en la oferta dicho sistema, constituido por depósito de preparación de reactivos, bomba de recirculación en inoxidable y válvulas de aislamiento y de recirculación en inoxidable.
Como etapa final al proceso de adecuación del agua al proceso productivo de nuestro cliente, se ha incorporado una línea de dosificación de sosa al permeado para que éste alcance el pH necesario.
Instrumentación y control
Todo el funcionamiento de cada una de las plantas de ósmosis inversa se controla desde el cuadro eléctrico, donde se encuentra el autómata que gobierna la instalación, que conecta con el centro de operaciones de la fábrica.
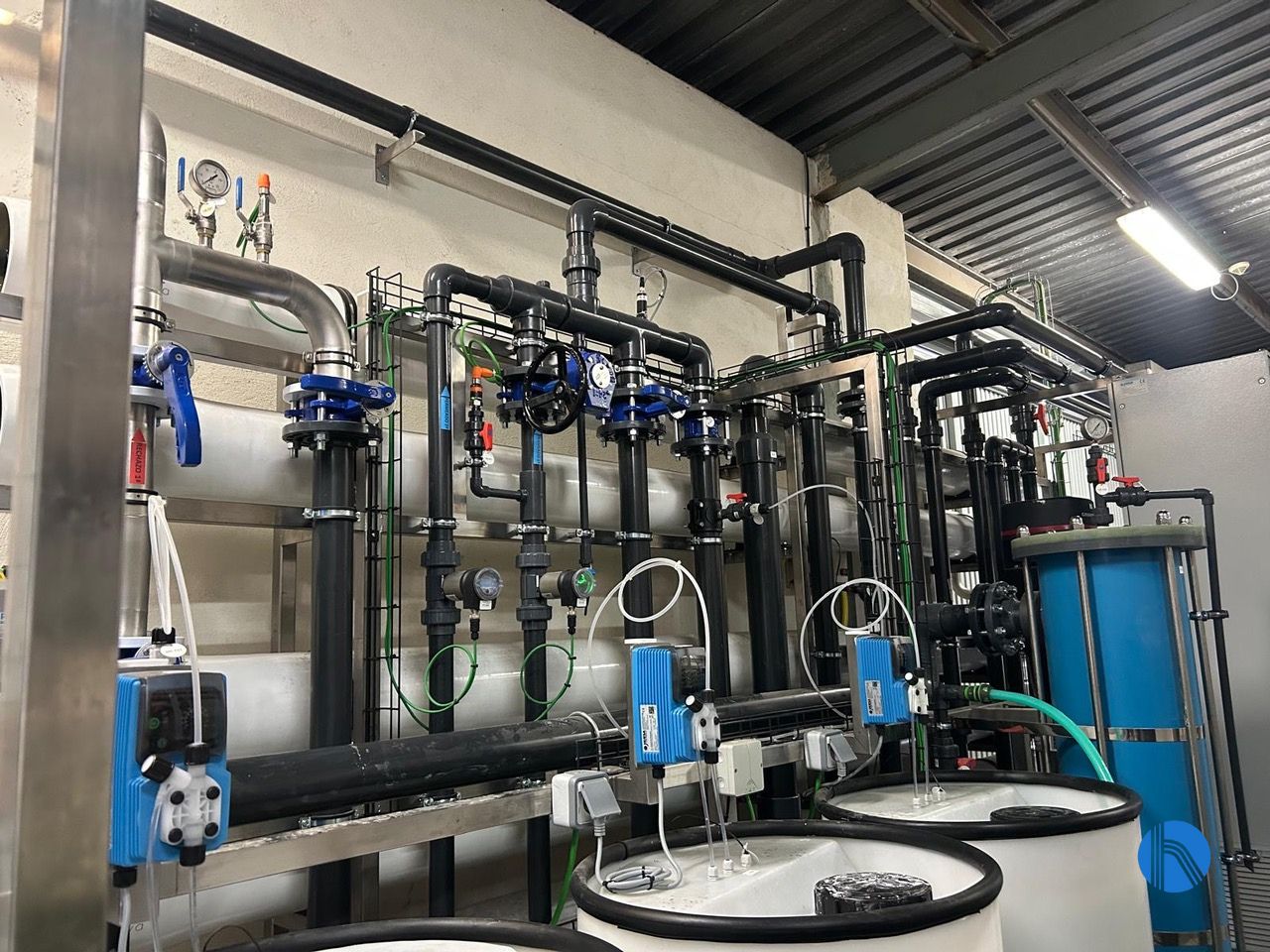
Vista bombas y elementos de control
En el caso que nos ocupa, se tiene un control de la conductividad y redox a la entrada de la osmosis inversa, así como de conductividad y de pH a la salida de agua osmotizada.
Además, dispone de válvula de regulación de rechazo de tipo aguja en AISI-316 para lograr una óptima eficacia del proceso.
Los caudales de agua tratada en ambas etapas de ósmosis inversa y el caudal de rechazo son medidos en continuo mediante caudalímetros, que nos permiten saber con qué caudales está trabajando el equipo.
Las presiones están controladas por manómetros y transmisores de presión en filtro bicapa, portacartucho, bomba de alta presión y membranas.
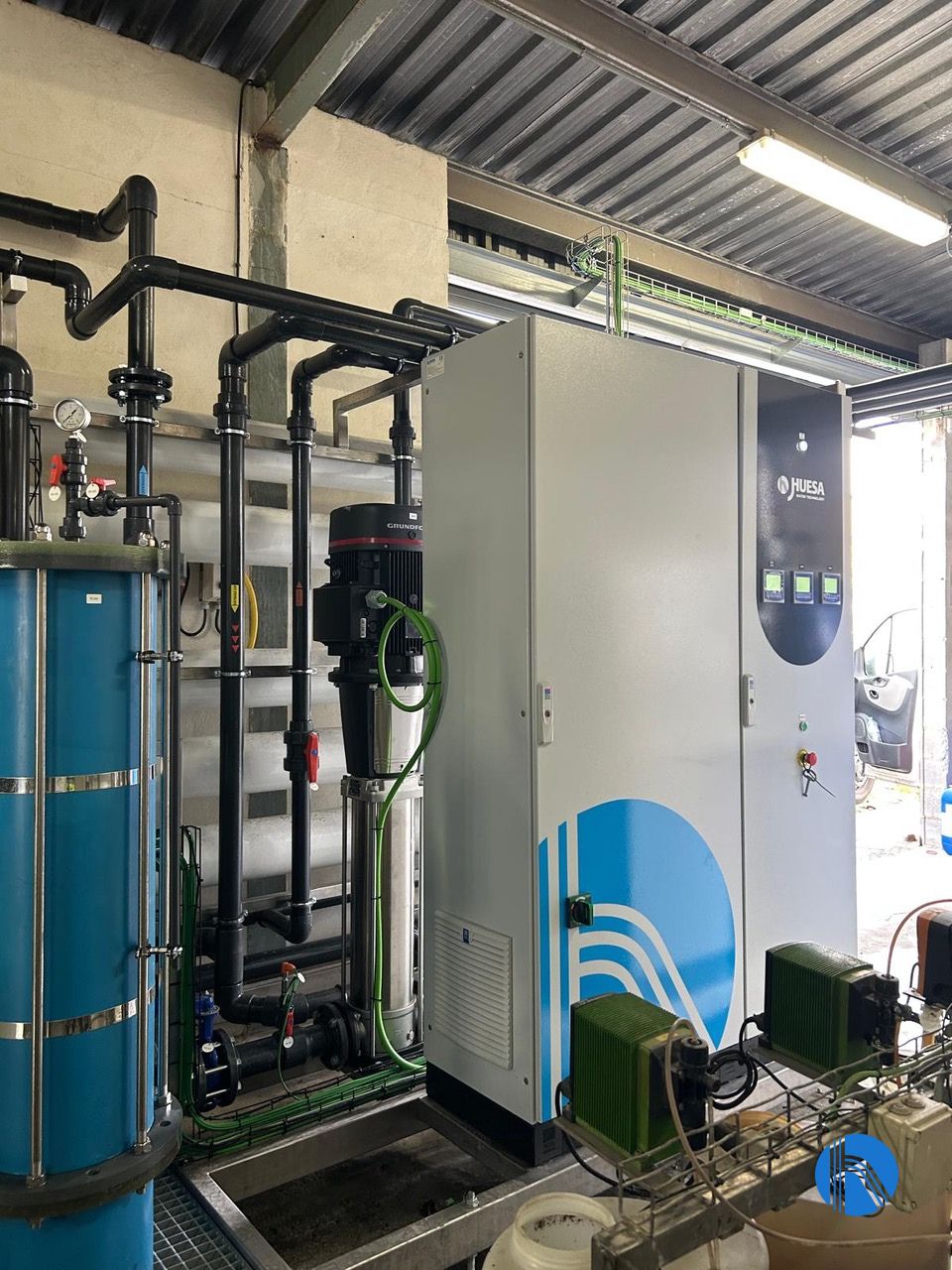
Vista Cuadro de control
Beneficios del uso de la Ósmosis Inversa
Las principales ventajas de utilizar un tratamiento mediante técnicas de separación por membranas semipermeables de ósmosis inversa son:
- Operación continua y automática, sin necesidad de regeneración.
- Reducción del consumo químico, eliminando el uso de productos como la sosa caústica y el ácido clorhídrico.
- Barrera microbiológica efectiva, garantizando agua libre de contaminantes.
- Menor impacto ambiental, sin generación de vertidos peligrosos.
- Mantenimiento sencillo y optimizado, con cambios periódicos de filtros y membranas.
Conclusión
La implementación de un sistema de ósmosis inversa en la industria de fragancias no solo garantiza un suministro de agua con la calidad necesaria para procesos productivos y calderas, sino que también optimiza la eficiencia operativa y reduce los costos asociados al mantenimiento de los equipos.
Desde una perspectiva técnica, la eliminación de impurezas y la estabilidad en los parámetros fisicoquímicos permiten mejorar la fiabilidad del proceso y asegurar la calidad del producto final. A nivel comercial, contar con un sistema de tratamiento de agua avanzado representa una ventaja competitiva para las empresas de fragancias, ya que garantiza la consistencia en la producción y minimiza el impacto ambiental.
Las empresas especializadas en tratamiento de aguas, como J. Huesa, juegan un papel clave en el desarrollo de soluciones personalizadas que se adaptan a las necesidades específicas de cada industria. Invertir en tecnología de ósmosis inversa no solo mejora la rentabilidad y sostenibilidad de las operaciones, sino que también refuerza el compromiso con la calidad y la innovación en el sector.