Introduction to the case
In the molecular fragrance and flavour industry, water quality plays a fundamental role in both production processes and the operation of industrial boilers. The presence of impurities, dissolved salts and microbiological contaminants can directly affect the quality of the final product and the operating efficiency of the equipment.
In this case, a reverse osmosis water treatment plant was designed for a factory located in Andalusia, with the aim of guaranteeing high purity water both for the production process and for steam generation in boilers.
Specifically, this is an industry that has created a new production line in the Andalusian manufacturing centre.
Feed water quality for industrial boilers
Boiler feed water must meet certain parameters to avoid corrosion and scaling problems. According to standard UNE-EN 12953-10:2003 standard, the requirements are as follows:
- Total hardness: Ideally zero or very low, measured in mg/L of CaCO₃, to prevent the formation of incrustations.
- pH: Optimum range between 10.5 and 11.5, with a maximum permissible of 12.5, to minimise corrosion and optimise the effectiveness of chemical treatments.
- Dissolved oxygen: Must be eliminated or reduced to minimum levels (<0.007 mg/L) to prevent corrosion.
- Conductivity: Controlled to prevent the accumulation of salts that can affect boiler performance.
Water quality in the fragrance production
In the fragrance industry, water purity is critical to ensure the quality of the final product. The use of purified water is recommended.
The parameters to consider are:
- Microbiological load: The water should have a low microbiological load to avoid contamination of the product.
- Absence of ions and additives: The water must not contain ions or additives that could interfere with the formulation of the fragrances.
- Reduction of organic matter: The presence of organic matter can alter the stability of the fragrance, so an efficient removal process is required.
Adopted solution
After studying the characteristics of the raw water supplied to the system and considering the specific needs of our client, J. Huesa‘s technical team opted to design and build a customised water treatment plant consisting of the following sub-processes:
- Pre-treatment by means of a pre-filtration system using two-layer beds, responsible for carrying out the removal of the coarsest solids that may be present in the water flow that is fed to the system.
- The reverse osmosis is made up of two stages, the first of 3 tubes with 4 membranes and the second of 2 tubes with 4 membranes.
The following data have been taken as the basis for the design of the plant in question:
Design data | |
---|---|
Input flow | 28,6 m³/h |
Peak flow (backwash) | 50,3 m³/h |
Permeate flow | 20 m³/h |
Daily permeate flow | 400 m³/day |
Working hours | 20 h/day |
Pre-treatment
The water to be treated is pumped through a low-speed automatic backwashing two-layer filter, where any suspended solids in the water will be retained.
This filter has a system of independent valves to carry out the filter washing process. The valves are automatically operated.
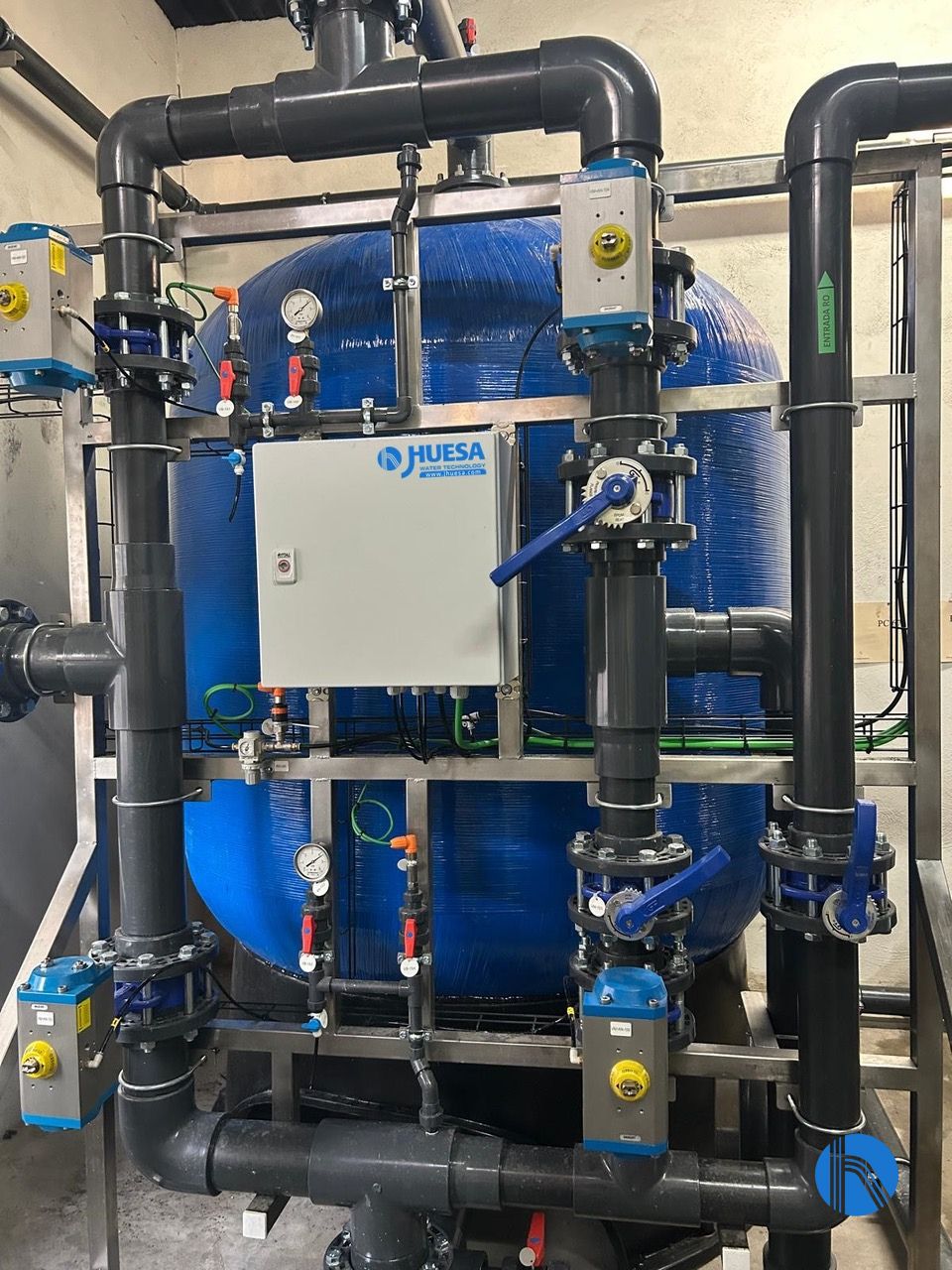
Two-layer filter
This cleaning process consists of two stages:
Backwashing: To clean the load, the same inlet water is used, which is introduced into the filter at the bottom, and in sufficient quantity to remove the load vigorously, but without it accumulating at the top. The water used is discharged.
Settling: After backwashing, the load must be prepared for the filter’s return to service. For this purpose, this settling phase is used, where the same water is introduced at the top and, as with backwashing, the outlet is redirected to the drain, producing a ‘load tightening’ effect.
This cleaning process is carried out by time and/or maximum pressure loss in the water line between the inlet and outlet.
The water is then subjected to a dosage of antiscalant and sequestrant. Subsequently, the treated water will be fed to a safety pre-filter before entering the reverse osmosis system, which will be used to refine those small solids that have not been retained by the two-layer filter.
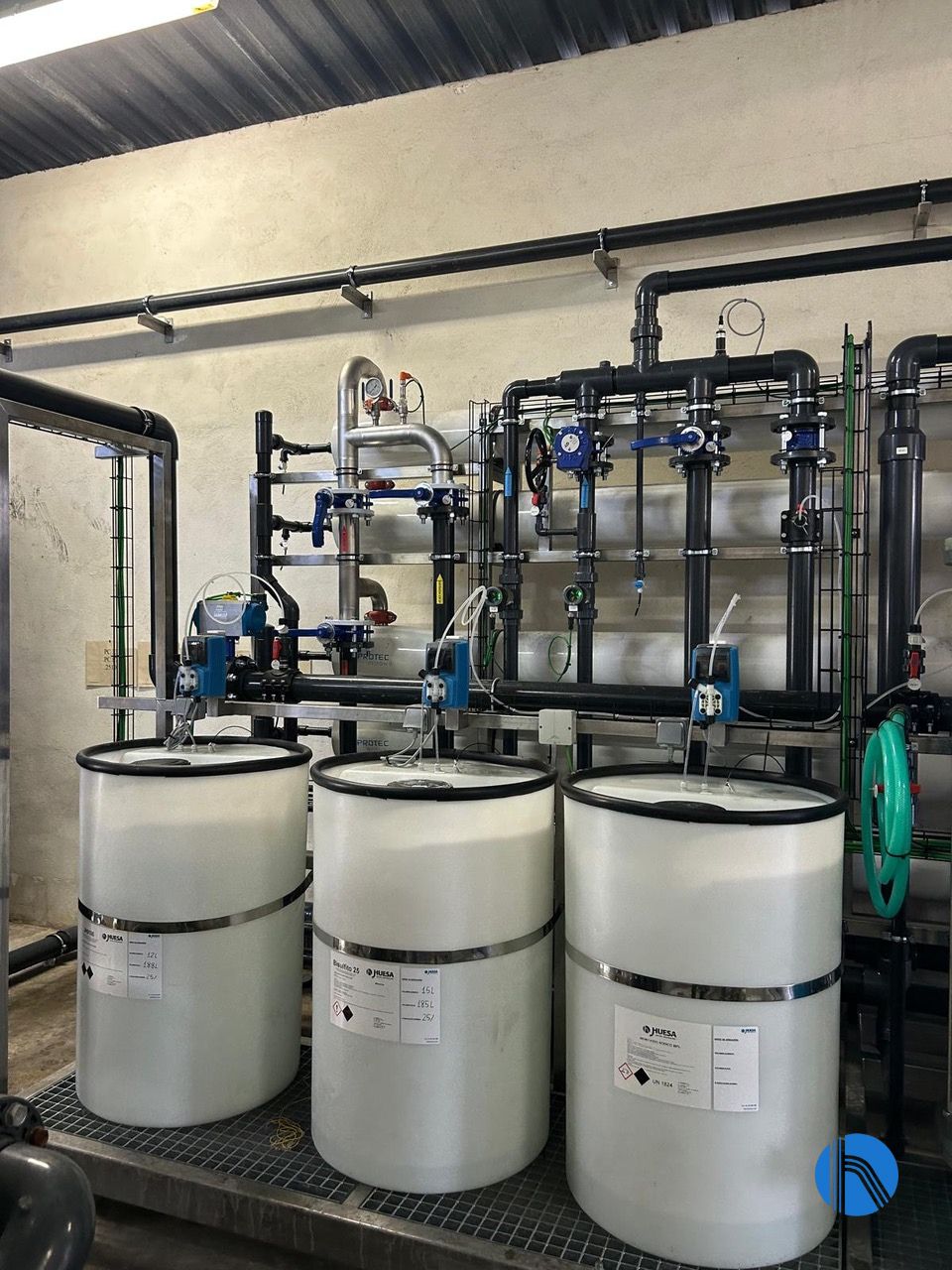
Dosing system
The safety filter consists of replaceable 5-micron cartridges, which are controlled by a pressure difference controlled by two pressure gauges placed at the inlet and outlet of the filter. The frequency of cartridge replacement depends on the colloid content of the water.
Reverse Osmosis
The reverse osmosis system is made up of two stages, the first of which consists of 3 tubes with 4 membranes and the second of which consists of 2 tubes with 4 membranes. To control the flow and pressure inside the system, the equipment will be equipped with flow meters and pressure transmitters. In addition, a CIP/Flushing system will be installed to wash the membranes periodically.
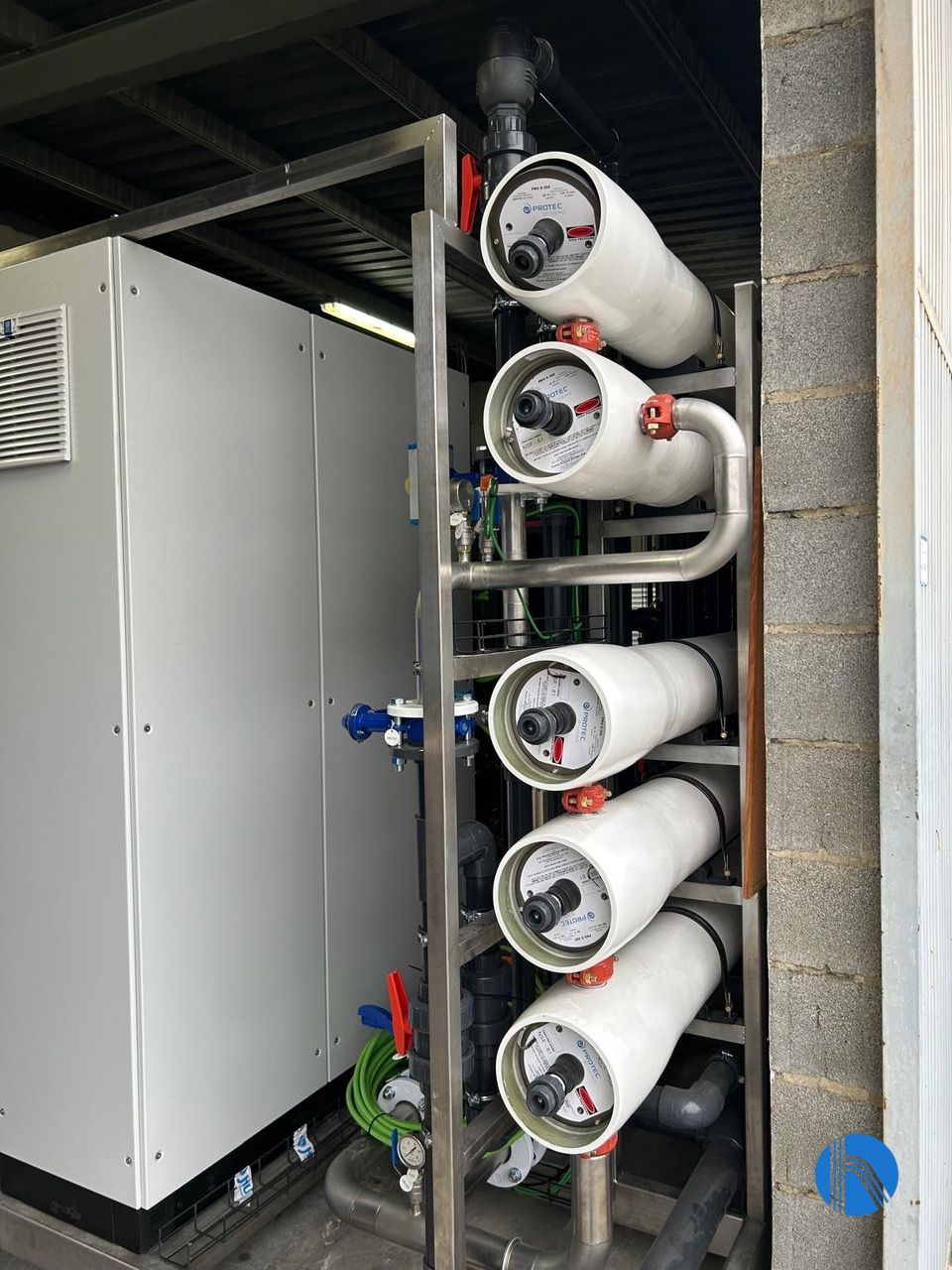
Two steps of Reverse Osmosis
The fundamental elements to carry out reverse osmosis are:
High-pressure pump: The osmotic pressure is a physical characteristic that depends on the concentration of each solution and increases as a function of this. The water to be treated has a natural osmotic pressure of approximately 0.7 kg/cm². This natural pressure plus the net pressure necessary to obtain the production flow (which is called operating pressure) is obtained by using a high-pressure vertical centrifugal pump made of AISI 316 stainless steel.
This is one of the most important parts of the equipment, as it is the only mechanical element in permanent movement, which determines the maintenance of the equipment and the cost per cubic metre of water treated as a function of the electrical energy consumed.
Reverse osmosis membranes: The installation is fitted with spiral wound membranes, made of polyamide and specially designed for brackish water up to 8000 ppm and with the characteristic of working at low pressure. These membranes have a high chemical resistance, as they can work in a pH range of 2 to 13, which makes them very easy to wash and recover, as they can accept a wide variety of washing chemicals.
The membranes will be mounted in pressure housings, made of coiled GRP.
Membrane washing equipment: All membrane installations become fouled over time, depending to a greater or lesser extent on the pre-treatment installed, requiring one to two cleanings per year. Given the size of the equipment offered, this system has been included in the offer, consisting of a reagent preparation tank, stainless steel recirculation pump and stainless-steel isolation and recirculation valves.
As a final stage in the process of adapting the water to our client’s production process, a soda dosing line has been added to the permeate to bring it up to the required pH.
Instrumentation and control
The entire operation of each of the reverse osmosis plants is controlled from the electrical panel, where the automaton that governs the installation is located, which connects to the factory’s operations centre.
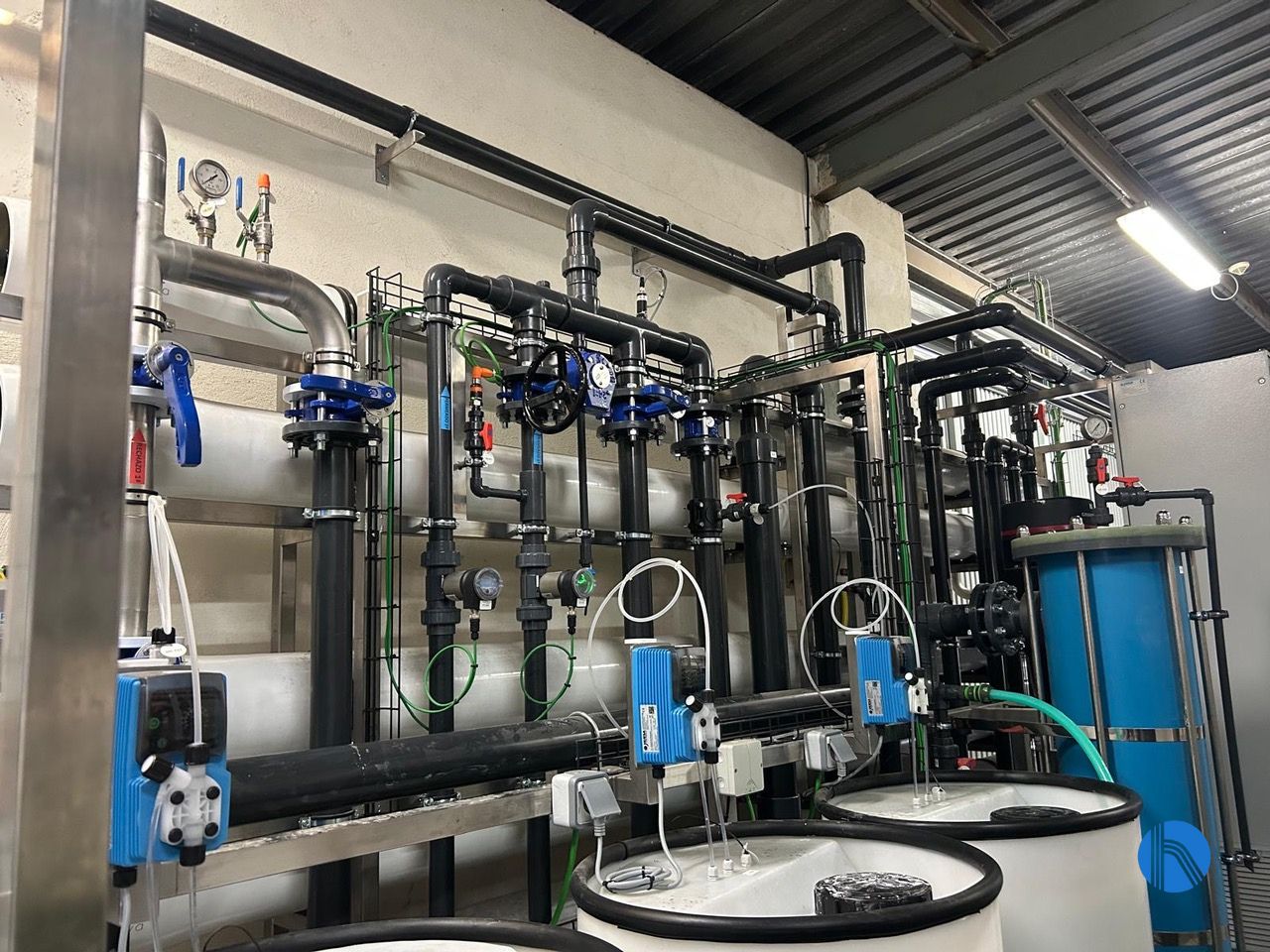
View of pumps and control elements
It controls conductivity and redox at the RO inlet and conductivity and pH at the RO outlet.
It also has an AISI 316 needle type rejection control valve to achieve optimum process efficiency.
The flow rates of the treated water in both reverse osmosis stages and the rejection flow rate are continuously measured by flow meters, allowing us to know the flow rates at which the plant is operating.
The pressures are controlled by manometers and pressure transmitters in the double layer filter, cartridge holder, high pressure pump and membranes.
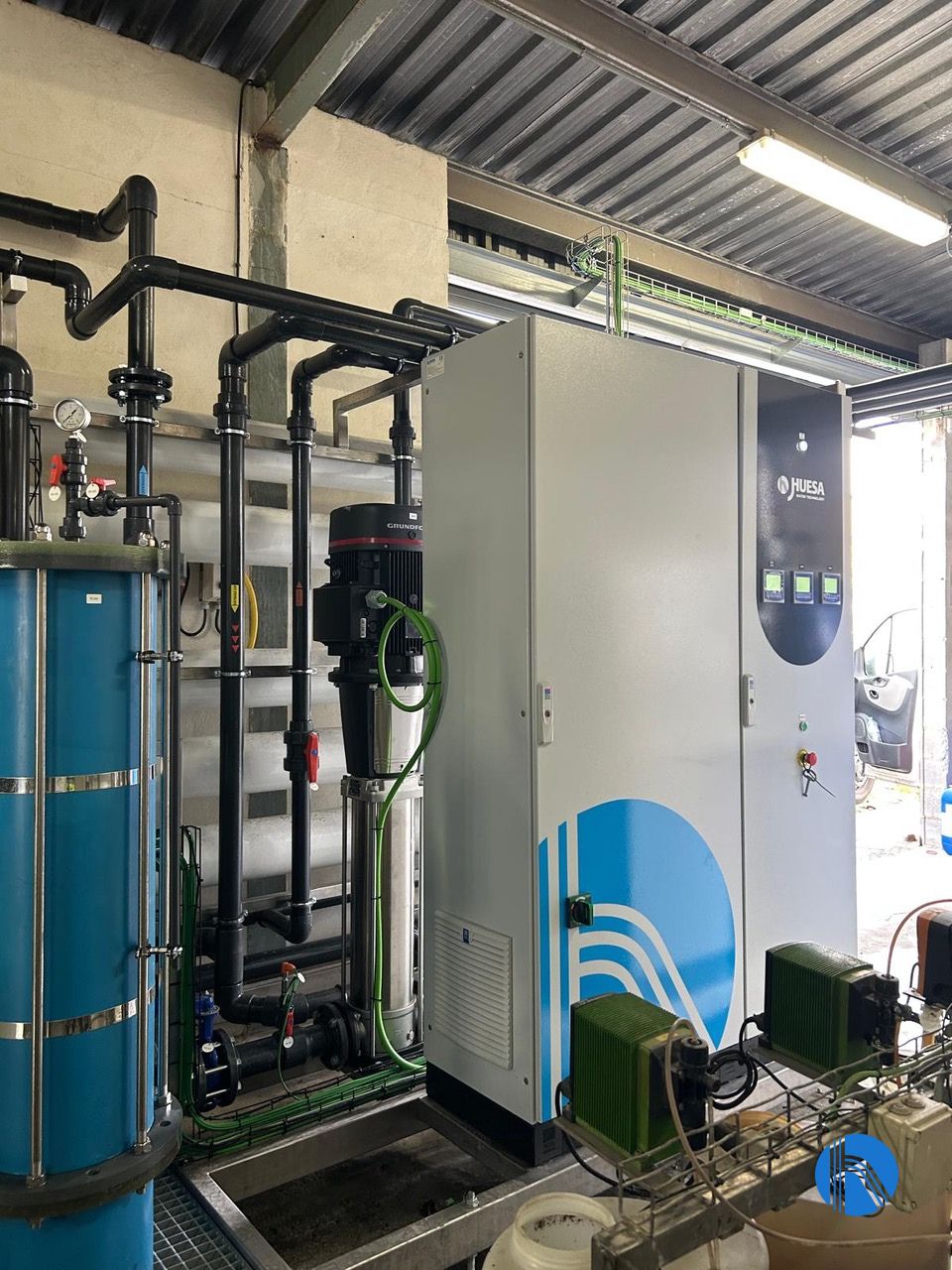
Control panel view
Advantages of using reverse osmosis
The main advantages of using reverse osmosis semi-permeable membrane separation techniques are:
- Continuous and automatic operation, without the need for regeneration.
- Reduced chemical consumption, eliminating the use of products such as caustic soda and hydrochloric acid.
- Effective microbiological barrier, ensuring contaminant-free water.
- Reduced environmental impact, as no hazardous waste is generated.
- Simple and optimised maintenance, with periodic replacement of filters and membranes.
Conclusion
The implementation of a reverse osmosis system in the fragrance industry not only guarantees a water supply of the required quality for production processes and boilers but also optimises operational efficiency and reduces the costs associated with equipment maintenance.
From a technical point of view, the elimination of impurities and the stability of physico-chemical parameters improve process reliability and ensure the quality of the final product. On a commercial level, an advanced water treatment system is a competitive advantage for fragrance companies as it ensures consistency in production and minimises environmental impact.
Specialist water treatment companies, such as J. Huesa, play a key role in developing customised solutions to meet the specific needs of each industry. Investing in reverse osmosis technology not only improves the profitability and sustainability of operations but also reinforces the sector’s commitment to quality and innovation.