Hoy hablamos de reingeniería. Una de las premisas del éxito en el tratamiento del agua, tanto de procesos industriales, como su
depuración es comprender con precisión el proceso productivo de cada sector al que nos
enfrentamos, prestando especial atención en la importancia de la correcta caracterización de las
aguas y, en consecuencia, del diseño de las plantas de tratamiento.
La reingeniería de procesos es clave en nuestro sector, en el que el conocimiento de tecnologías de
tratamiento de aguas de última generación y una correcta retroalimentación cliente – ingeniería
durante toda el proceso, garantiza una correcta reingeniería de procesos y prolonga la vida útil de los
fabricados.
Siguiendo en esta línea, hoy nos vamos a centrar en varios casos de éxito de J. Huesa en los que la colaboración estrecha de los departamentos técnico y de postventa de nuestra empresa con el de nuestros clientes, ha permitido ofrecer una solución completa y típica en cada uno de los sectores de actuación.
CASO 1: SECTOR MATADERO
Antecedentes
Como punto de partida, se procedió a auditar las instalaciones de nuestro cliente y se pudo
constatar que la línea de tratamiento existente de la EDARi no cumplía con los requisitos de vertido a
cauce.
Dicho vertido proviene de 3 corrientes distintas:
- Salmueras
- Líneas de proceso (matadero)
- Aguas procedentes de la limpieza de establos (purines)
Los vertidos a través de la línea de proceso se realizan de lunes a viernes, incrementándose éste los días de sacrificio que habitualmente tienen lugar solo dos días a la semana, con un turno de trabajo de 8 horas. Las mediciones de vertido de días de sacrificio son de 15 y 19 m3.
Tras la visita se expone al cliente la opción de separar la línea de salmueras y gestionarla de forma
independiente, no incluyéndose en el vertido de la EDARi.
Objetivo
J. Huesa tuvo como propósito transformar la línea existente en una que cumpliera con los requisitos
de vertido a cauce, adaptando los equipos existentes e incluyendo los necesarios.
Para ello se tuvieron en cuenta las características del agua bruta del agua aportada, de cada una de
las dos líneas a considerar. Puesto que se desconocía la cantidad de vertido procedente de cada
corriente, se tomaron como datos de diseño los más desfavorables de cada línea.
Los requisitos del agua tratada son los siguientes:
Conductividad | 3.500 μs/cm2 |
ph | 5,5 – 9 |
DQO | 1.400 mg/L |
DBO | 700 mg/L |
Aceites y grasas | 150 mg/L |
SS | 500 mg/L |
N amoniacal | 85 mg/L |
N nítrico | 65 mg/L |
Fósforo total | 30 mg/L |
En este sentido, hubo que tener en cuenta las siguientes consideraciones:
- La temperatura del reactor biológico debe mantenerse en el rango 20-35 ºC
- La capacidad del sistema de aireación debe ser adecuada para alcanzar 125 mg/l de DQO en salida
- La concentración de AyG del agua bruta debe ser inferior a 100 mg/l
- El pH del licor mezcla debe mantenerse en el rango 6,5 – 8,5.
- El tratamiento biológico no influye en la conductividad del agua bruta. Si bien, hay que confirmar que la conductividad de las corrientes de agua bruta están dentro de la ley. Además, no se recomiendan conductividades en el agua bruta superiores a 7.500 μs/cm2, ya que a partir de este valor la actividad biológica se va reduciendo proporcionalmente llegando a inactivarse en el horizonte de 15.000 μs/cm2
Solución adoptada
Finalmente, con los trabajos de J. Huesa se consiguió transformar la antigua EDARi en un sistema de depuración mediante SBR, aprovechando al máximo los equipos existentes y disminuyendo así el coste del proyecto y las molestias por las posibles obras a realizar en las instalaciones de nuestro cliente.
Los parámetros bajo los que se diseñó la nueva planta de tratamiento son:
Caudal diseño | 10 m3/día |
Horas de trabajo industria | 8 h/día |
Horas de trabajo depuradora | 24 h/día |
Caudal punta | 4 m3/h |
Uso del agua tratada | Vertido |
Los principales componentes del sistema se describen a continuación:
- Arqueta de bombeo y tamizado (existente), con una capacidad de 1.500 l/hora y un haz de luz
de 1 mm. - Tratamiento biológico, de forma que la balsa existente se transforma en un SBR
(reactor biológico secuencial), instalando un sistema de agitación, control biológicos y extracción de fangos y clarificados formado por:
– Agitador sumergible
– Control pH y redox
– Aireador radial flotante (existente)
– Vertedero flotante para extracción de clarificados
– Bomba extracción de fangos
- Línea de fangos: se va a proceder únicamente a la acumulación de fangos en el decantador
existente de una capacidad de unos 72 m3. Con esta capacidad y la cantidad de producción
de fangos (aproximadamente 0,75 m3/d) se tiene un tiempo de retención hidráulico de los
fangos de 96 días, que permiten una autonomía suficiente para su gestión.
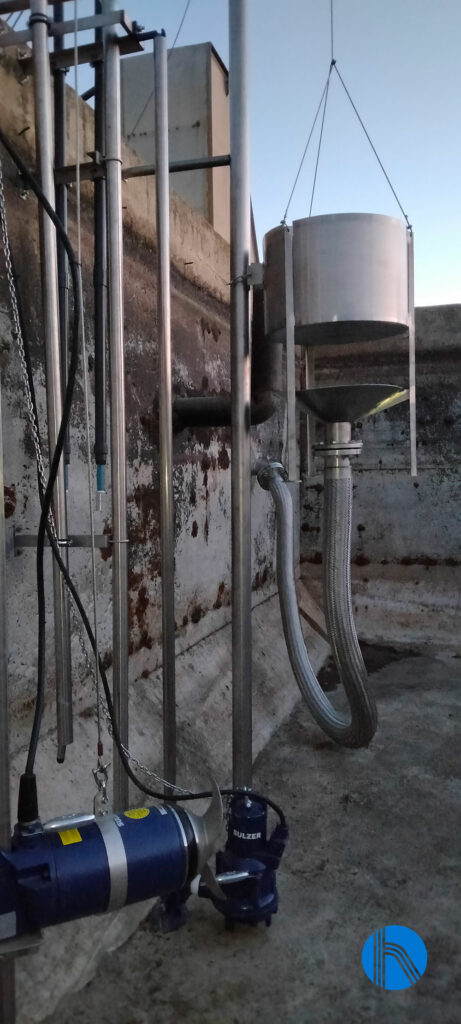
Detalle vertedero flotante
CASO 2: SECTOR RENDERING
Antecedentes
En esta ocasión nos encontramos con una empresa del sector rendering que cuenta con un
tratamiento terciario para aprovechar las aguas procedentes de la EDARi en el sistema de
refrigeración de la planta de producción.
Tras una serie de visitas de asistencia técnica por parte del departamento de postventa de J. Huesa,
se pudo constatar que el sistema de aireación instalado en la balsa de aireación del SBR no era
suficiente para la carga de trabajo de la planta.
Concretamente se pudo constatar lo siguiente:
- Una de las turbinas sufre incidentes repetitivos de volcado, y
- Adicionalmente, la potencia instalada de aireación es insuficiente para la carga de trabajo
deseada.
Ambos motivos, generan un déficit de oxígeno en el reactor que limita la capacidad de reutilización.
Objetivo
Establecer el sistema de aireación que garantice la aireación necesaria en la balse del SBR instalado
en el cliente, de forma que no se vea limitada su capacidad de reutilización.
Solución general adoptada
El equipo técnico de J. Huesa ha optado por el suministro, instalación y puesta en marcha de 3
aireadores de 75 kW de potencia nominal que posibilitan el incremento de la capacidad de
tratamiento del sistema biológico implantado.
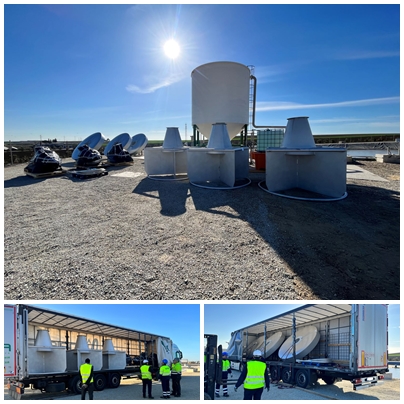
Detalle del suministro de los aireadores
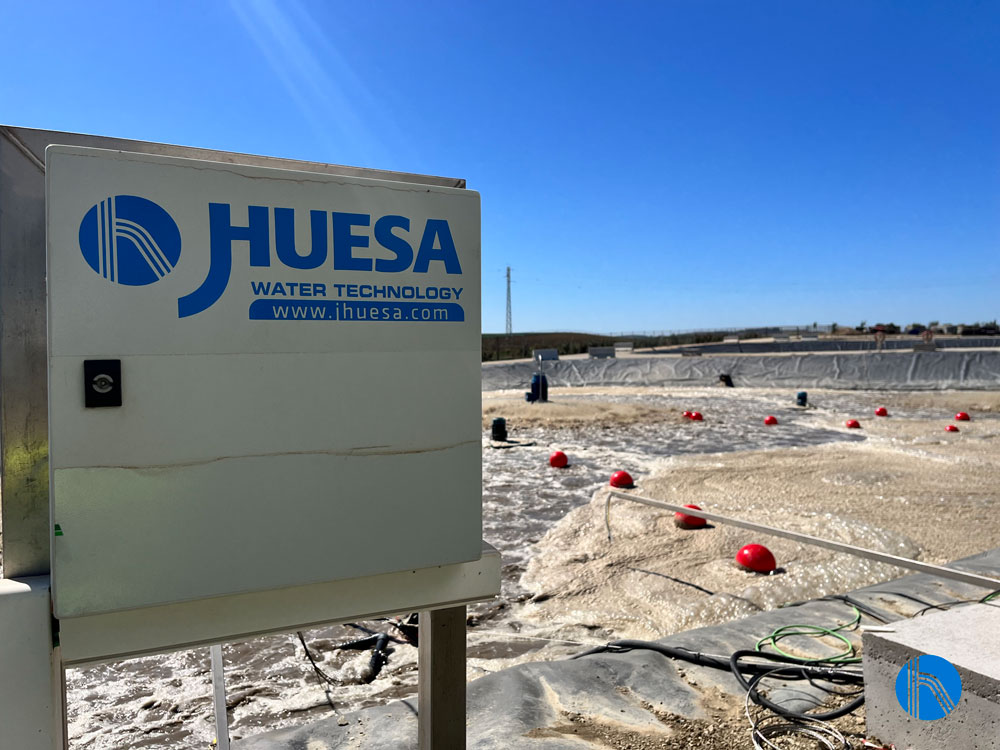
Detalle de la puesta en marcha
CASO 3: SECTOR AGROALIMENTARIO
Antecedentes
Nuestro cliente, una marca líder en la fabricación de bebidas naturales, tiene una fábrica en España
que dispone de una planta de tratamiento de aguas de proceso cuyo subproceso principal es la
ósmosis inversa que se alimenta de agua de red.
En una visita inicial, se revisaron los distintos elementos de la planta de tratamiento de agua, entre los
que destacamos:
- El depósito de almacenamiento del agua de red que alimenta a la ósmosis inversa carecía de
un sistema de desinfección en continuo. Tienen una capacidad de 3 m3. - Los depósitos de acumulación de agua osmotizada, que se mezclan con el agua de red para
obtener la calidad deseada, también carecen de un sistema de desinfección en continuo. - Previo a su aporte como materia prima, el agua tratada pasa por un ultravioleta con una
capacidad de 87 W.
Objetivo
Establecer un sistema de desinfección que garantice la ausencia de patógenos en el agua de aporte
que se emplea en la fabricación de las bebidas.
Solución general adoptada
En esta ocasión se ha optado por un sistema de recirculación y desinfección con ultravioleta:
Caudal diseño | 8 m3/día |
Dosis de radiación | 46 mJ/cm2 |
Potencia unitaria UV | 105 W |
Horas de recirculación | 24 horas/día |
- Puesto que en el depósito de almacenamiento de aguade red el tiempo de retención hidráulio
es bajo, no precisa sistema de recirculación. - Sin embargo, en los depósitos de acumulación de agua osmotizada el tiempo es bastante
elevado, por lo que aconsejamos el sistema de desinfección en continuo. - Hemos optado por un sistema de radiación ultravioleta con un sistema de recirculación en
continuo, 24 horas/día, que supone la opción más efectiva desde el punto de vista técnico
y económico.
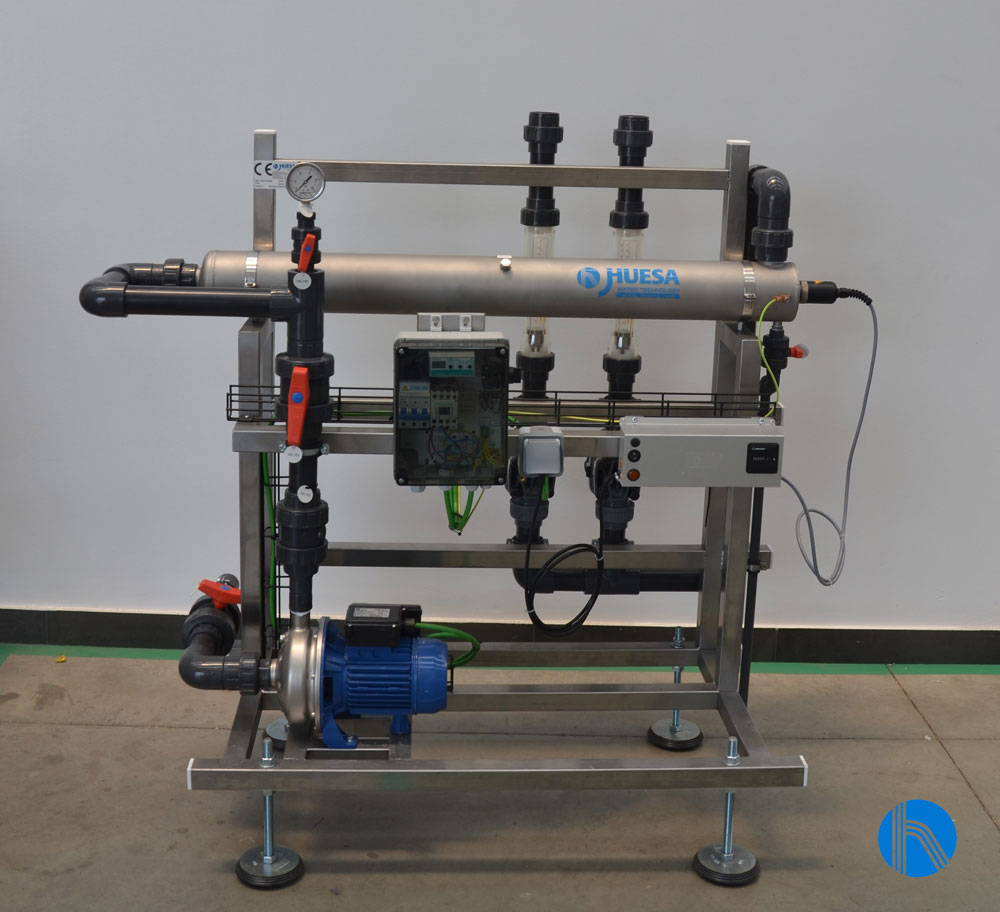
Detalle del skid con lámpara de UV