One of the premises of success in the treatment of water, both in industrial processes and its
purification, is to accurately understand the production process of each sector we are dealing with,
paying special attention to the importance of the correct characterisation of the water and,
consequently, the design of the treatment plants.
Process re-engineering is key in our sector, in which knowledge of the latest generation of water
treatment technologies and correct client-engineering feedback throughout the process guarantees
correct process re-engineering and prolongs the useful life of the manufactured products.
Continuing in this line, today we are going to focus on several success stories of J. Huesa in which the close collaboration of the technical and after-sales departments of our company with those of our customers, has allowed us to offer a complete and typical solution in each of the sectors in which we
operate.
CASE 1: SLAUGHTERHOUSE SECTOR
Background
At an initial stage of the process, our client’s facilities were audited and it was found that the existing treatment line of the WWTPi did not comply with the requirements for discharge into water courses.
The discharge comes from 3 different streams:
- Brine
- Process lines (slaughterhouse)
- Water from the cleaning of stables (slurry)
Dischargues through the processing line are carried out from Monday to friday, increasing the
slaughter days, which usually take place only two days a week, with an 8-hour shift. The
dischargue measurements for slaughter days are 15 and 19 m3.
During the visit, the option of separating the brine line and managing it independently, not including it
in the WWTPi discharged, was presented to the client.
Objective
J. Huesa’s aim was to transform the existing line into one that complied with the requirements for
discharge into the municipal sewer, adapting the existing equipment and including the necessary
ones.
To this end, the characteristics of the raw water of the water supplied to each of the two lines to be
considered were taken into account. Since the amount of discharge from each stream was unknown,
the most unfavourable data for each line were taken as the design data.
The requirements for treated water are as follows:
Conductivity | 3.500 μs/cm2 |
ph | 5,5 – 9 |
COD | 1.400 mg/L |
BOD | 700 mg/L |
Oils and fats | 150 mg/L |
SS | 500 mg/L |
Ammoniacal N | 85 mg/L |
Nitric N | 65 mg/L |
P total | 30 mg/L |
In this regard, the following considerations had to be taken into account:
- The temperature of the biological reactor should be kept in the range 20-35 ºC.
- The capacity of the aeration system should be adequate to reach 125 mg/l COD at the outlet.
- The A&G concentration of the raw water should be less than 100 mg/l
- The pH of the mixed liquor should be kept in the range 6.5 – 8.5.
- The biological treatment does not influence the conductivity of the raw water. However, it has to be
confirmed that the conductivity of the raw water streams is within the law. In addition,
conductivities in the raw water above 7,500 μs/cm2 are not recommended, as from this value
onwards the biological activity is reduced proportionally and becomes inactivated at the
15,000 μs/cm2 horizon.
Adopted solution
Finally, with j. Huesa´s work, we were able to transform the client´s old WWTPi into a treatment system
using SBR (sequential biological reactor), making the most of existing equipment and thus reducing the
cost of the project.
The parameters under which the new treatment plant was designed are:
Design flow | 10 m3/día |
Working hours industry | 8 h/día |
Working hours WWTP | 24 h/día |
Peak flow | 4 m3/h |
Used of treated water | Vertido |
The main components of the system are described below:
- Pumping and screening pit (existing), with a capacity of 1,500 l/hour and a 1 mm beam.
- Biological treatment (existing), so that the existing pond is transformed into an SBR (sequential
biological reactor), installing a system of agitation, biological control, and extraction of sludge and
clarified sludge consisting of:
– Sumersible agitator
– pH and redox control
– Floating radial aerator (existing)
– Floating weir for clarified sludge extraction
– Sludge extraction pump
- Sludge line: sludge will only be accumulated in the existing decanter with a capacity of about 72 m3. With this capacity and the amount of sludge production (approximately 0.75 m3/d),
there is a hydraulic sludge retention time of 96 days, which allows sufficient autonomy for
sludge management.
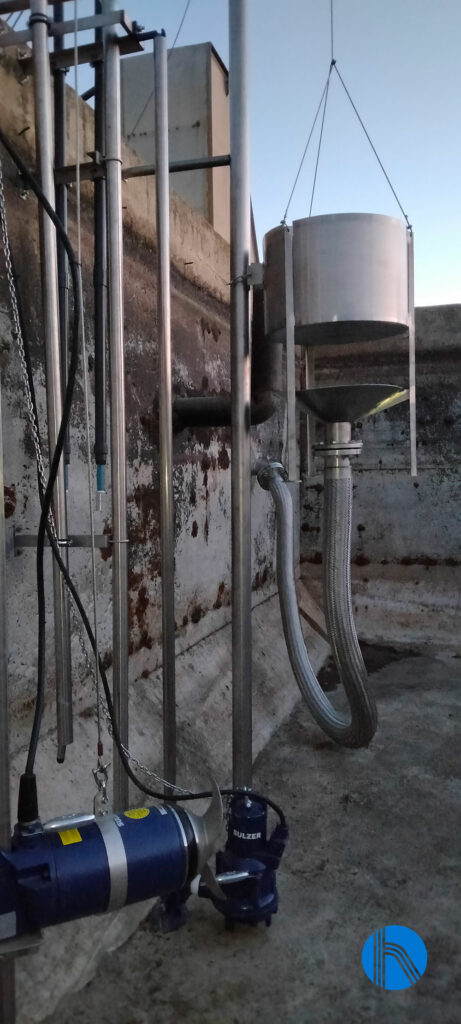
Detail of floating spillway
CASE 2: RENDERING SECTOR
Background
On this occasion, we are dealing with a company in the rendering sector that has a tertiary treatment
system to use the water from the WWTPi in the cooling system of the production plant.
After a series of technical assistance visits by the after-sales department of J. Huesa, it was found that the aeration system installed in the SBR aeration basin was not sufficient for the workload of the plant.
Specifically, the following was observed:
- One of the turbines suffers repetitive incidents of overturning, and
- In addition, the installed aeration capacity is insufficient for the desired workload
Both reasons generate an oxygen deficit in the reactor that limits the reuse capacity.
Objective
To establish the aeration system that guarantees the necessary aeration in the SBR basin installed at
the client, so that its reuse capacity is not limited.
Adopted solution
The technical team of J. Huesa has opted for the supply, installation and commissioning of 3 aerators
of 75 kW nominal power that make it possible to increase the treatment capacity of the biological
system in place.
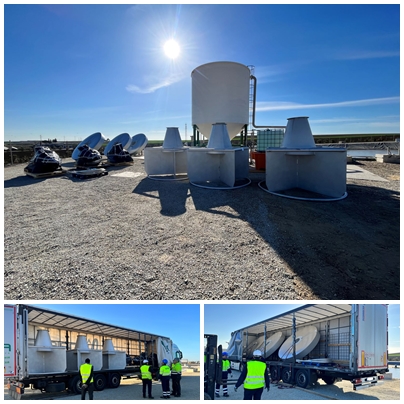
Detail of aerator
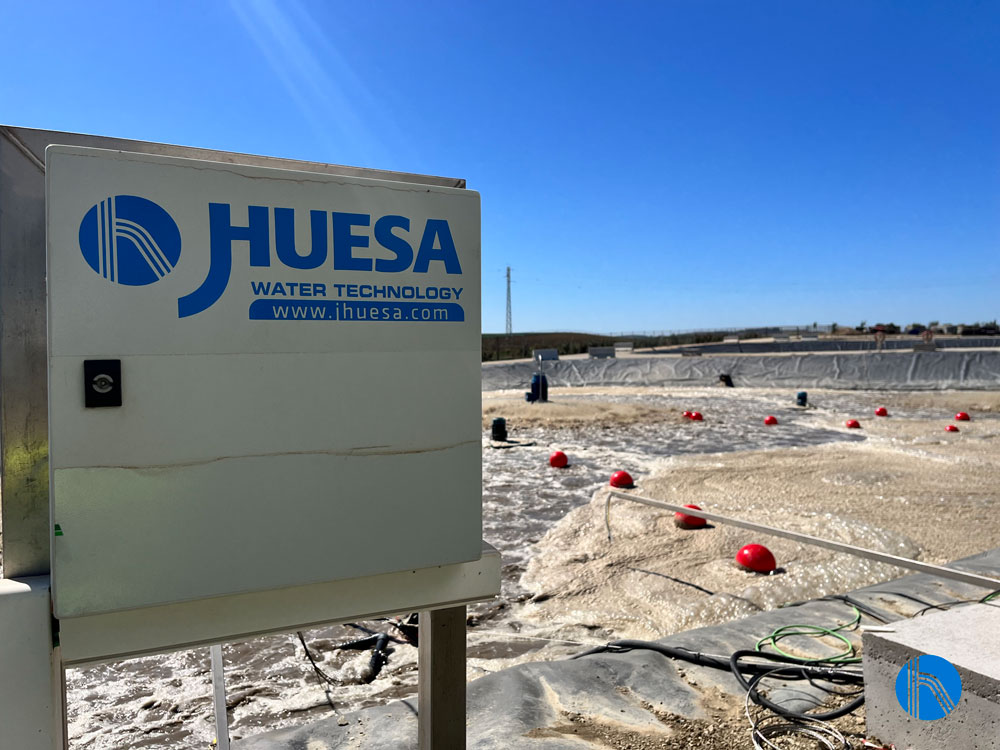
Detail of the commissioning
CASE 3: AGRO-FOOD SECTOR
Background
Our client, a leading brand in the manufacture of natural beverages, has a factory in Spain with a
process water treatment plant whose main sub-process is reverse osmosis fed by mains water.
In an initial visit, the different elements of the water treatment plant were reviewed, among which we
highlight:
- The storage tank for the mains water feeding the reverse osmosis lacked a continuous
disinfection system. They have a capacity of 3 m3. - The osmosis water storage tanks, which are mixed with the mains water to obtain the desired
quality, also lack a continuous disinfection system - Before being used as raw material, the treated water is passed through an ultraviolet system with a capacity of 87W.
Objective
To establish a disinfection system that guarantees the absence of pathogens in the feed water
used in the manufacture of beverages.
Adopted solution
On this occasion, a recirculation and ultraviolet disinfection system was chosen:
Design flow | 8 m3/day |
Radiation dosis | 46 mJ/cm2 |
UV unit power | 105 W |
Recirculation hours | 24 hours/day |
- Since the hydraulic retention time in the mains water storage tank is low, a recirculation
system is not required. - However, in the osmosis water storage tanks the retention time is quite long, so we
recommend a continuous disinfection system. - We have opted for an ultraviolet radiation system with a continuous recirculation system, 24
hours/day, which is the most technically and economically effective option.
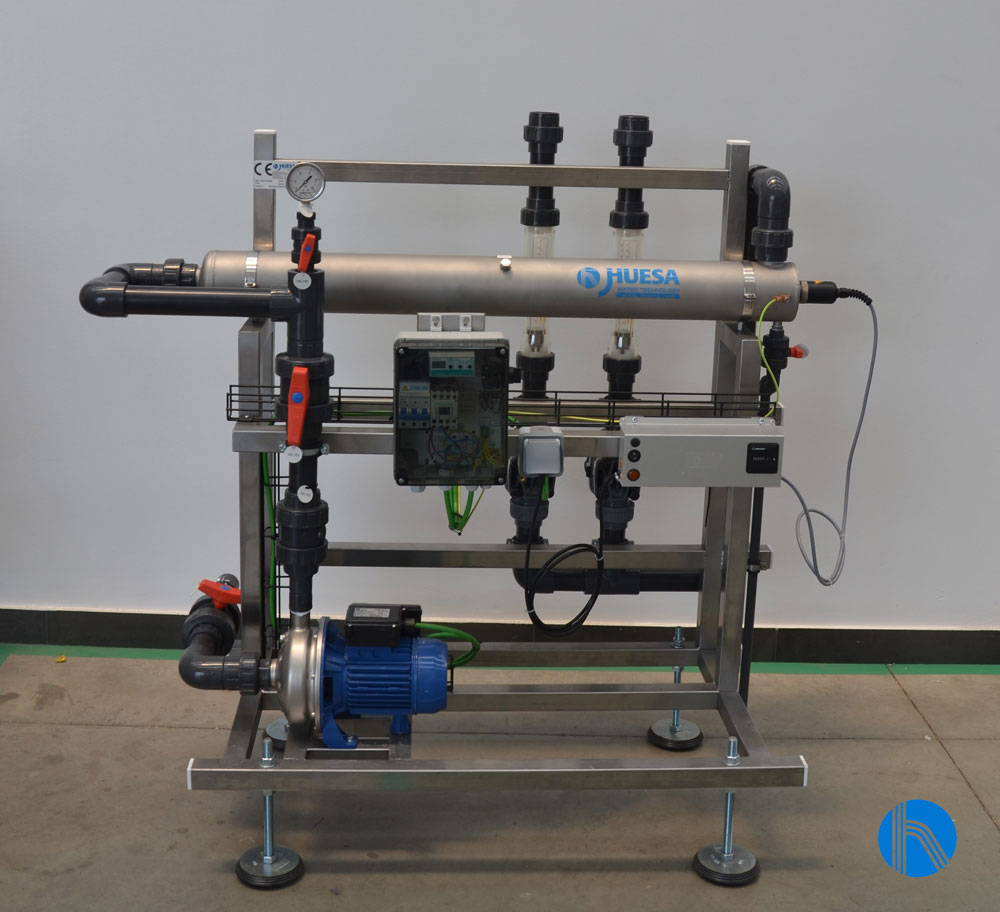
Detail of the skid with UV lamp