J. Huesa finaliza los trabajos de instalación de la línea de baja carga y la puesta en marcha de la línea de alta carga, dos de las líneas de tratamiento que componen la planta de tratamiento de aguas residuales industriales del nuevo Centro de Tratamiento Integral de Residuos lndustriales No Peligrosos (CTRINOP) en Abajas, provincia de Burgos.
Este proyecto que fue declarado de interés regional por la Junta de Castilla y León tiene previsto ejecutarse en 6 fases y posibilitará el tratamiento de distintos caudales de agua que se dimensionan para un caudal previsto de más de 55 m3/día, procedentes de:
- Lixiviados propios del depósito de residuos no peligrosos del Centro de Tratamiento,
- Aguas Pluviales y las fecales que se originen en el propio Centro,
- Y, por último, líquidos orgánicos de baja y alta carga contaminante, procedentes de vertidos industriales no peligrosos.
En esta ocasión, el Departamento Técnico de J. Huesa ha optado por la implantación de un conjunto de tecnologías que permiten tratar agua de muy diversa índole, de forma que en función de las características del agua bruta y, teniendo en cuenta los límites de vertido, el agua a tratar seguirá un tratamiento u otro.
Línea de Baja Carga
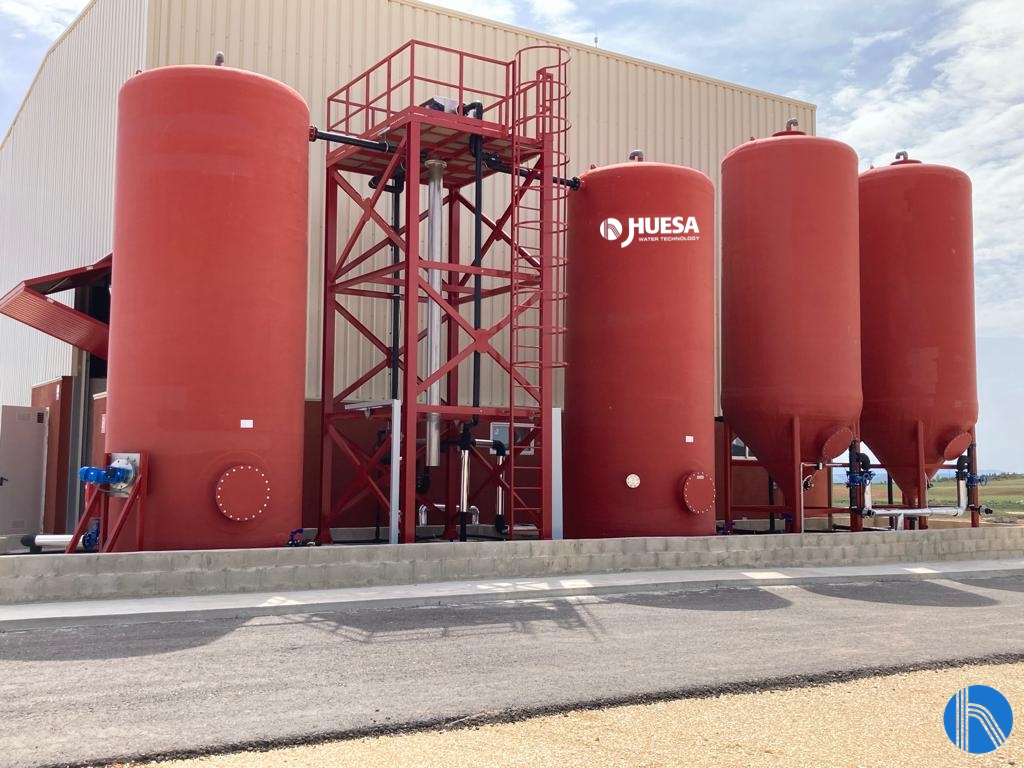
Vista depósitos de almacenamiento y homogeneización
En primer lugar, vamos a describir la línea de baja carga que, como su propio nombre indica, se empleará para tratar las aguas de baja carga contaminante. También se usará como pretratamiento de los vertidos de alta carga que tengan un alto contenido en sólidos en suspensión y Aceites y Grasas.
A continuación, se detallan los equipos que componen esta línea de tratamiento:
En función del origen del vertido de baja carga contaminante, éste puede llegar a la línea de dos formas distintas:
- Cuando se corresponden con vertidos producidos en el vertedero, pasan directamente al tamiz rotativo.
- Cuando proceden del exterior, en una etapa inicial son almacenados en un tanque de fondo cónico dotado de todos los elementos de conexión camión-depósito.
En ambos casos, el agua tamizada es acumulada en un depósito de PRFV dotado de agitación para evitar la decantación de las partículas en suspensión. Nos referimos al depósito situado a la izquierda en la imagen de arriba.
El tamiz rotativo es un dispositivo de funcionamiento auto – limpiante capaz de operar durante largos periodos de tiempo sin necesidad de atención.
El líquido para filtrar entra en el tamiz rotativo por la tubería de entrada y se distribuye uniformemente a lo largo de todo el cilindro filtrante que gira a baja velocidad. Las partículas sólidas quedan retenidas en la superficie de este y son conducidas hacia el rascador, que es el encargado de separarlas y depositarlas sobre una bandeja inclinada para su caída por gravedad.
Físico – Químico tipo DAF
A continuación, el vertido entra en la siguiente etapa de tratamiento, el físico -químico tipo DAF (Dissolved Air Flotation). Para garantizar la separación de los sólidos en la cámara de flotación, el vertido pasa por las cámaras de coagulación y floculación (fabricadas en PRFV y dotadas de la agitación necesaria), en las que se lleva a proceso de coagulación y floculación, inyectando coagulante y floculante, por un lado y sosa para el control de pH, por otro.
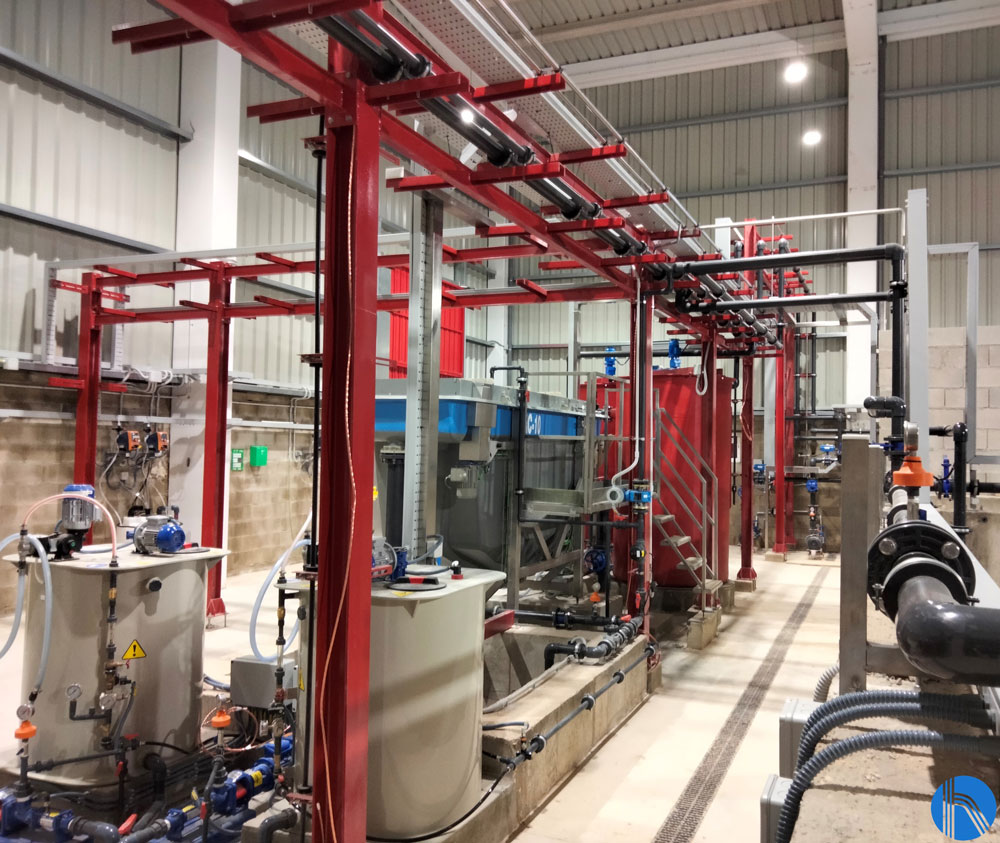
Vista planta DAF
Una vez entra en el DAF, y gracias al régimen laminar y al efecto de las microburbujas que en él se inyectan junto con el vertido en la entrada, los flóculos formados en la etapa anterior ascienden a la superficie formando el fango y dejando el agua clarificada libre de partículas sólidas. En la superficie del DAF existen unos rascadores que eliminan el fango y lo retiran del equipo.

Vista decantador centrífugo
Los vertidos así tratados pasan a la balsa de almacenamiento, desde la que se tratarán en la línea biológica que está prevista instalar cuando el vertedero esté al 100 % de funcionamiento.
Esta instalación está provista de un cuadro eléctrico de control provisto de un autómata programable y una pantalla táctil para el manejo y configuración de la planta. El equipo de Instrumentación y Control de J. Huesa ha diseñado el cuadro de control para que pueda ser integrado en el sistema SCADA del cliente.

Vista CE
Línea de alta carga
Al igual que con los vertidos de baja carga, los de alta carga contaminante pueden tener una doble procedencia:
- Los generados en el propio vertedero son bombeados desde la balsa de lixiviados al tamiz rotativo, en el que se eliminan los sólidos de mayor tamaño. La salida del tamiz va directamente al depósito de homogeneización de PRFV y 25 m3 de capacidad.
- Al igual que los vertidos de baja carga, los de alta carga procedentes del exterior en una etapa inicial son almacenados en un tanque de fondo cónico dotado de todos los elementos de conexión camión-depósito. Desde este depósito son bombeados al tamiz rotativo para acabar, finalmente, en el depósito de homogeneización (depósito ubicado a la derecha de la estructura del tamiz en la imagen superior).
El tanque de homogeneización está dotado de una bomba de recirculación con una doble función:
- Mantener el vertido agitado al tiempo que se dosifica ácido sulfúrico (H2SO4).
- Llevar a cabo un control de pH gracias al phmetro insertado en esta línea de recirculación.
Hay que tener en cuenta que tener un ph ligeramente ácido en este punto es importante y mejora significativamente el rendimiento de la ósmosis inversa que está ubicada en el interior de un contenedor de 40” High Cube.
Pretratamiento
A continuación, el agua es bombeada al interior de un filtro bicapa a baja velocidad y de lavado automático donde se retienen los sólidos en suspensión que pudiera contener el agua bruta.
Concretamente, se ha dispuesto de un filtro de poliéster reforzado de fibra de vidrio (PRFV), con un diámetro de 762 mm y un caudal nominal de 3 m³ /hora. Está provisto de un sistema de válvulas independientes para realizar la operación de lavado del filtro. Este proceso de limpieza consta de dos etapas: contra lavado y asentamiento.
La maniobra sobre la valvulería se realiza de manera automática, y se encuentra gestionada por el autómata ubicado en el cuadro de control incluido y que está ubicado en una sala independiente dentro del propio contenedor. La producción de agua filtrada se interrumpe cuando el filtro solicite limpieza que puede ser por tiempo en horas de servicio y/o diferencia de presión detectada entre entrada y salida.
A continuación, se dosifica productos químicos, concretamente biocida y secuestrante y anti incrustante con el objetivo de evitar el ensuciamiento de las membranas y alargar la vida útil de las membranas de ósmosis inversa.
Ósmosis Inversa
Agua bruta | 3 m3/h |
Alimentación tubos | 40 m3/h |
Concentrado recirculado | 37 m3/h |
Conversión RO | 65 % |
Horas de trabajo | 24 h/día |
Uso del agua tratada | Vertido |
Teniendo en cuenta la carga contaminante del agua bruta, la ósmosis inversa se caracteriza por tener que trabajar con altas presiones para poder tratar el agua correctamente.
El agua pretratada pasa a la ósmosis inversa que está precedida de dos prefiltros de seguridad, uno de 10 micras y otro de 5 micras en el que quedan retenidos posibles escapes de partículas y SS. Una vez el agua está preparada, se impulsa mediante una bomba de alta presión de pistón en acero inoxidable AISI 316 con una capacidad de 8 m3/hy capaz de proporcionar una presión máxima de 60 bar aproximadamente.
Es sistema de ósmosis inversa está configurado en una única etapa, constituido por dos tubos de presión que contienen, cada uno de ellos, 5 membranas, consiguiendo una conversión en torno al 65 %. Para garantizar el aporte de presión suficiente, se ha diseñado el sistema con una recirculación de 37 m3/h, de forma que a la planta entran 40 m3 a la hora.
La instalación está provista de membranas de configuración en espiral, construidas en poliamida y especial para aguas y con la característica de trabajar a alta presión, alto flujo y resistentes al ensuciamiento. Están montadas en carcasas de presión, fabricadas en PRFV bobinado.
Se ha instalado en el contenedor un sistema de barrido o flushing – CIP que garantiza la limpieza automática de las membranas del interior del tubo. Estas limpiezas se programan desde la pantalla táctil, atendiendo a las necesidades de los operadores y/o cada vez que se produce una parada de la planta.
Adicionalmente se ha incorporado un sistema de limpieza química o CIP que se produce de forma semi automática cuando lo requiere el cliente en función de las exigencias de producción.
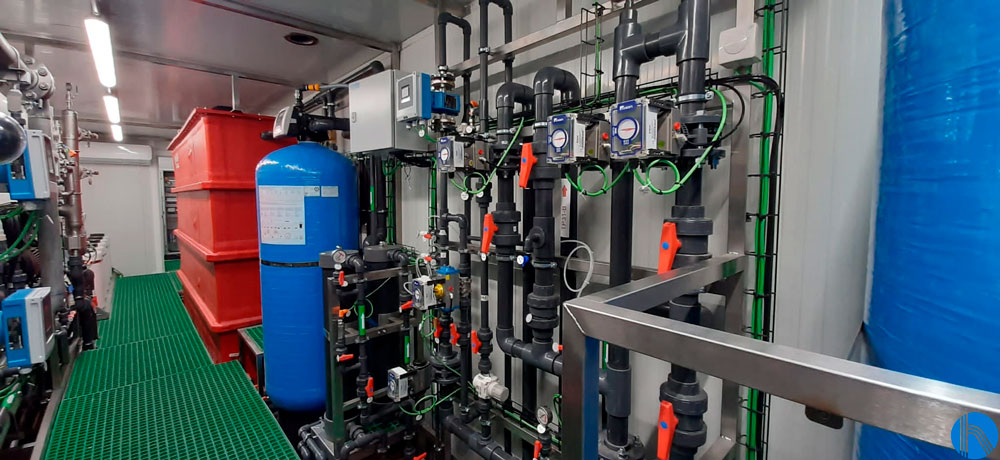
Vista flushing – CIP
La planta de ósmosis inversa está equipada con elementos de instrumentación y control (válvulas automáticas, presostatos, transmisores de presión, caudalímetros, medidores de conductividad y pH…) que se centralizan en un cuadro eléctrico, ubicado en el contenedor.
Así mismo, el cuadro incluye un autómata lógico programable y una pantalla táctil para el manejo y configuración de la planta. El equipo de Instrumentación y Control de J. Huesa ha diseñado el cuadro de control para que pueda ser integrado en el sistema SCADA del cliente.
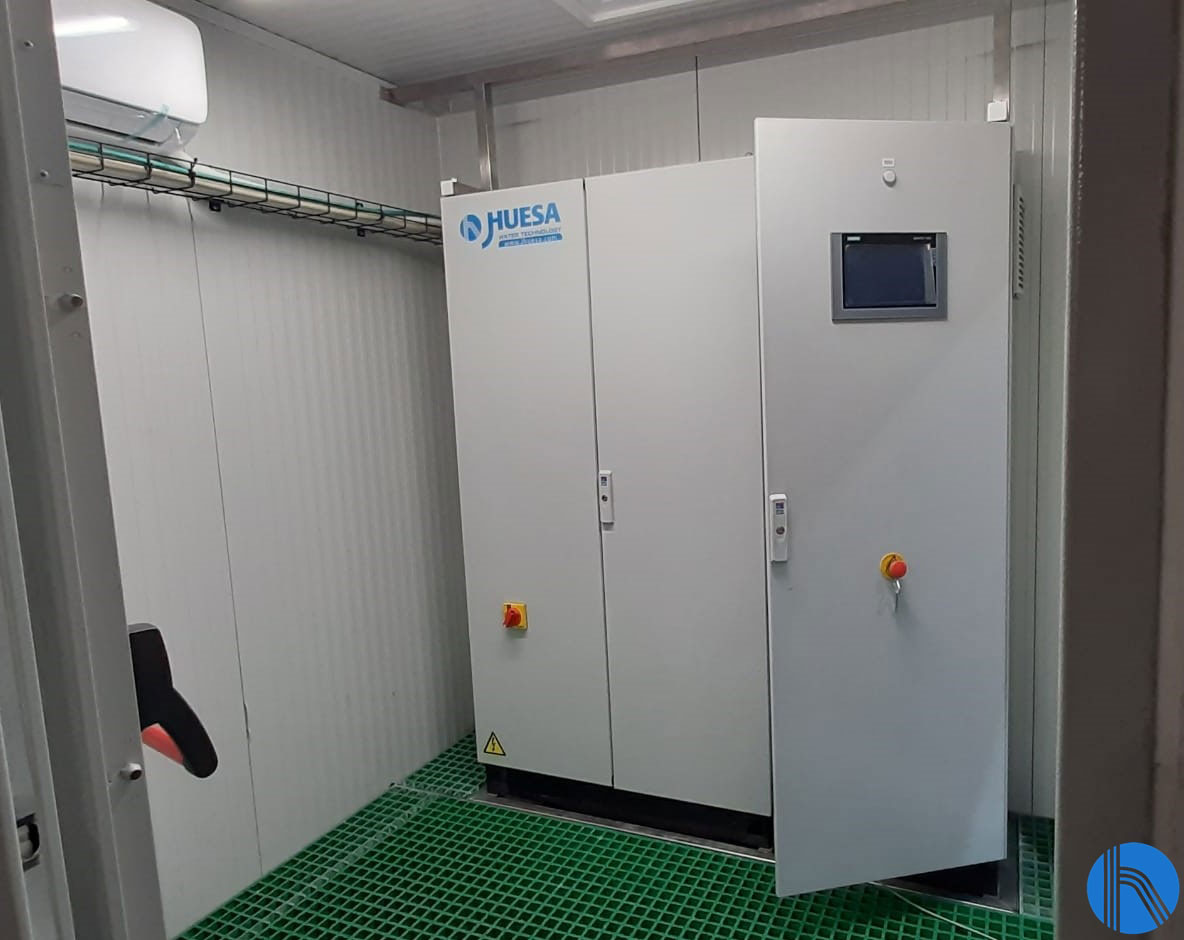
Vista CE interior del contenedor
¿Que tratamiento posterior tiene el rechazo de la ósmosis y/o a donde se conduce para su evacuación controlada?
¿que previsión existe en la reducción de nitrògeno en sus distintos compuestos (amoniacal, orgánico, nitritos, nitratos) se prevé alcanzar con la ósmosis inversa cuando se integren los lixiviados del vertedero?
¿o bien se conducirán al supuesto futuro tratamiento biológico ?
En este caso, la misma pregunta anterior: ¿que previsión existe en la reducción de nitrògeno en sus distintos compuestos?
Buenas tardes, Enric,
Gracias por la lectura exhaustiva del artículo y preguntas que plantea.
Le responderemos vía email a la mayor brevedad posible.
Un saludo y buen día,