En esta ocasión os presentamos el proyecto ejecutado para la compañía que explota la desaladora de
Al Ghubrah II, ubicada en la ciudad de Mascate en el Sultanato de Oman. Nuestro cliente precisaba de una planta piloto para el testeo de membranas de ósmosis inversa que le permitiese realizar pruebas de rendimiento en condiciones estándar, así como pruebas de lavado, con el fin de evaluar la idoneidad de los químicos utilizados y mejorar la planificación de la reposición de membranas requerida.
Una vez conocidos los requerimientos de partida, J. Huesa se puso manos a la obra para el diseño,
fabricación a medida, pruebas FAT y suministro de una planta de testeo de membranas de ósmosis
inversa capaz de operar y mantener en automático las condiciones standard de testeo para membranas de osmosis para agua de mar establecidas en 32,000 mg/l de salinidad, 800 psi (55 bares) de presión de alimentación a 25° C y una conversión del 8%.
Todos los parámetros arriba indicados pueden ser ajustados para pruebas en otras condiciones.
Vista panorámica de la desaladora de Al Ghubrah II
Requisitos de la planta piloto
La planta piloto debe ser capaz de realizar pruebas de rendimiento en las cuales se puedan analizar
parámetros de operación como caudal de permeado, rechazo, caída de presión, ensuciamiento de la membrana, etcétera, determinando las prestaciones y vida útil de las membranas en función del fabricante.
Los requisitos del testeo se detallan a continuación:
Caudal de alimentación máximo | 17 m3/h |
Máximo flujo de permeado | 1,5 m3/h |
Presión máxima de operación | 800 psi |
Solución de alimentación | 32.000 mg/L NaCl |
Tª de alimentación | 25 º C |
pH | 8,0 |
Recuperación | 8% |
Prueba de limpieza química:
Presión de alimentación | 4 bar |
Solución de alimentación | Depende del producto químico |
Tª de alimentación | 35-45 ºC |
pH | 2,0 – 13,0 |
Principales componentes de la planta
El agua de alimentación se acumula en un tanque de PRFV de 1000 litros de capacidad que está
provisto de distintos instrumentos analíticos para el control de las condiciones operativas del testeo, así como preparado para adecuar la temperatura de inicio de la prueba.
Sistema de refrigeración
Puesto que la temperatura de operación es 25 º C y el testeo se realiza en un circuito cerrado en el
que los equipos de bombeo aportan energía al sistema, es necesario la instalación de un sistema de refrigeración que sea capaz de adecuar la temperatura a la requerida para el inicio de las pruebas y adicionalmente mantenga la mantenga estable durante todo el proceso de operación.
Para resolver esta cuestión se ha instalado un sistema de refrigeración compuesto por los siguientes elementos:
- Enfriadora de 35 kWt integrada en la línea de proceso principal, encargada de mantener estable la temperatura
en las condiciones máximas de operación. - Enfriadora de 8 kWt integrada en un sistema de recirculación sobre el depósito para adecuar la temperatura
de inicio de operación mediante un intercambiador de placas y servir de respaldo a la máquina enfriadora principal.
Una vez que el transmisor de temperatura muestra el valor establecido, puede iniciarse el proceso de ensayo.
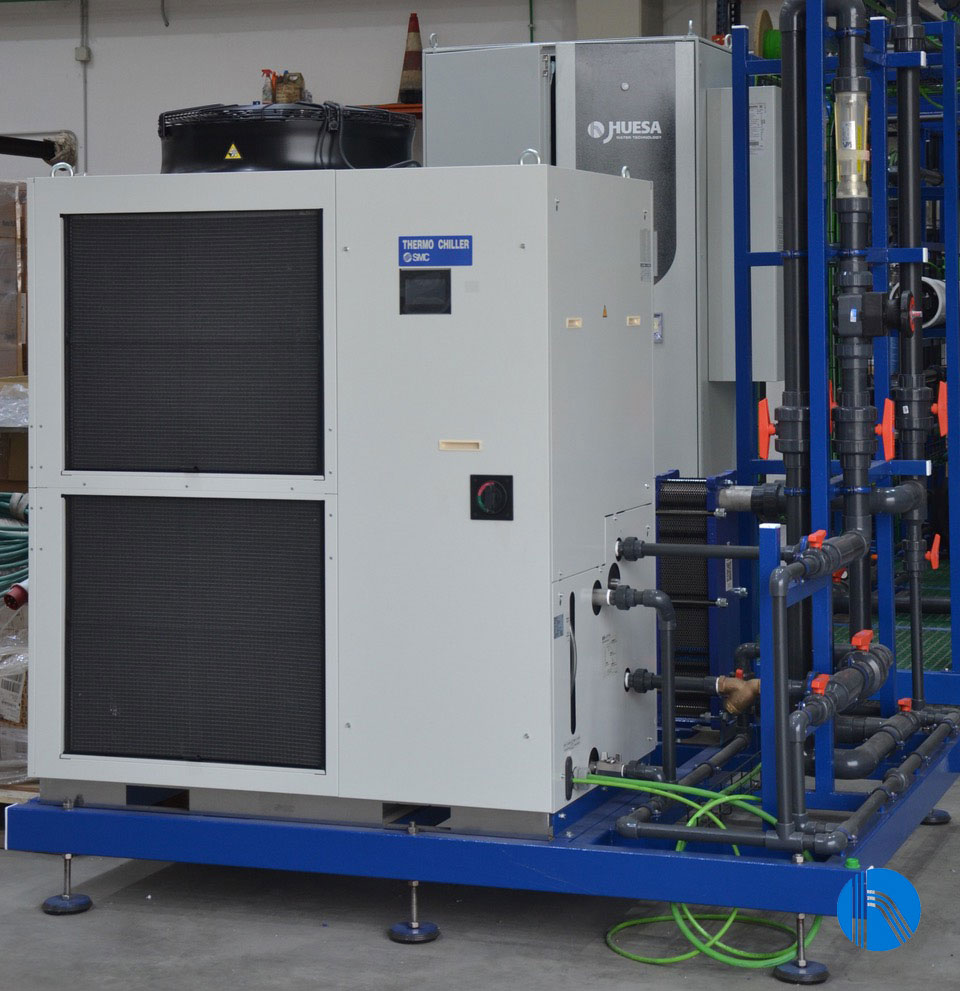
Detalle máquina enfriadora principal
Sistemas de bombeo y prefiltración
Dadas las condiciones del proyecto para la bomba de alimentación nos hemos decantado por una
bomba centrífuga de aporte construida en acero inoxidable que impulsa el agua de alimentación hasta la bomba de alta presión, pasando previamente por dos filtros de cartucho de 5 y 1 micras respectivamente, instalados en serie, previos a la ósmosis inversa.
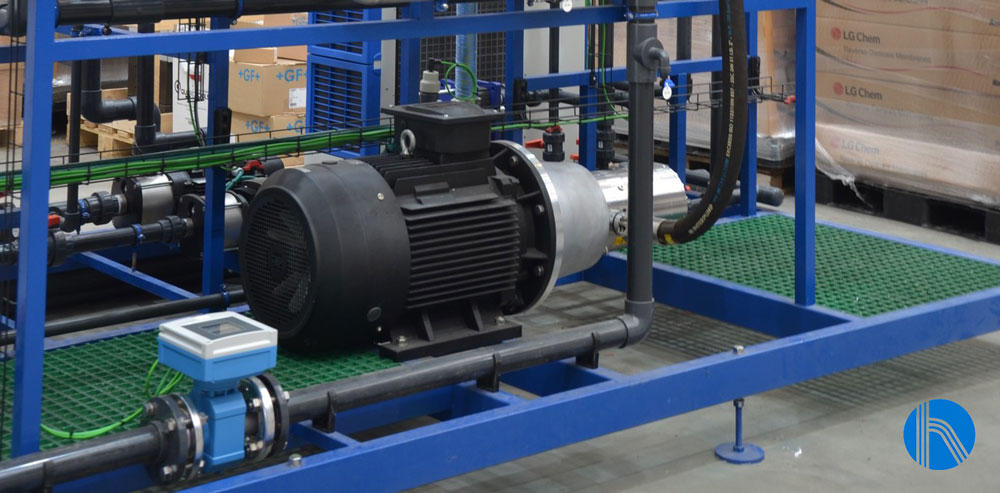
Detalle bomba alta presión
Para controlar el ensuciamiento de los filtros, se ha instalado a la entrada y a la salida de cada uno, un transmisor de presión y un manómetro. La función principal de estos filtros es la eliminación de partículas y contaminantes no deseados, aumentando la vida útil tanto de la bomba de alta presión como de la membrana.
Para garantizar el correcto funcionamiento del sistema, también se ha incluido, aguas arriba de la
bomba de alta presión, un transmisor de temperatura, un manómetro, un medidor de pH y un transmisor de
presión. Este último elemento se utiliza para detectar la falta de presión a la entrada de la bomba, de
forma que, si esto sucediese, el sistema se detiene inmediatamente e intenta restablecerse un número
definido de veces.
Para garantizar la obtención de agua libre de sales a partir del agua de mar, se ha instalado una bomba de alta presión alternativa para aumentar la presión osmótica, que es de acero inoxidable super dúplex y está controlada por un variador de frecuencia, de manera que permite ajustar la presión de operación por pantalla en función de las necesidades. El punto de funcionamiento será de 17 m3/h a 50 – 55 bar.
Ósmosis Inversa
La ósmosis inversa es un proceso por el que se desmineraliza el agua empujándola a presión a través
de una membrana semipermeable de ósmosis inversa. Funciona utilizando una bomba de alta presión
para aumentar la presión en el lado salino de la ósmosis inversa y forzar al agua a atravesar la
membrana semipermeable de ósmosis inversa, dejando casi todas las sales disueltas (entre el 95% y
el 99%) en el flujo de rechazo.
La cantidad de presión necesaria depende de la concentración de sal del agua de entrada. Cuanto más
concentrada sea el agua de entrada, más presión se necesitará para superar la presión osmótica.
La instalación estará provista de membranas de poliamida de configuración en espiral y construidas
especialmente para agua de alta concentración de sales de hasta 8000 ppm. Estas membranas tienen
una alta resistencia química, pueden trabajar en un rango de pH de 2-13, lo que les confiere una gran
facilidad de lavado y recuperación, admitiendo variedad de productos químicos de lavado.
El proceso de ósmosis inversa produce dos flujos diferentes:
- Agua permeada: Esta línea está fabricada en PVC y provista de instrumentos analíticos para
controlar la calidad del agua. - Línea de rechazo: Esta línea es de acero inoxidable y está dividida, a su vez, en tres líneas:
– Una línea con una válvula de aguja de regulación manual: para regular el caudal de rechazo
durante la producción en modo manual.
– Una línea con una válvula reguladora accionada eléctricamente: para regular el caudal
de rechazo durante la producción en modo automático.
– Una línea con una válvula manual: para abrir durante el lavado o CIP.
Ambas líneas se mezclan de nuevo con la ayuda de un mezclador estático y se recirculan al depósito
de alimentación.
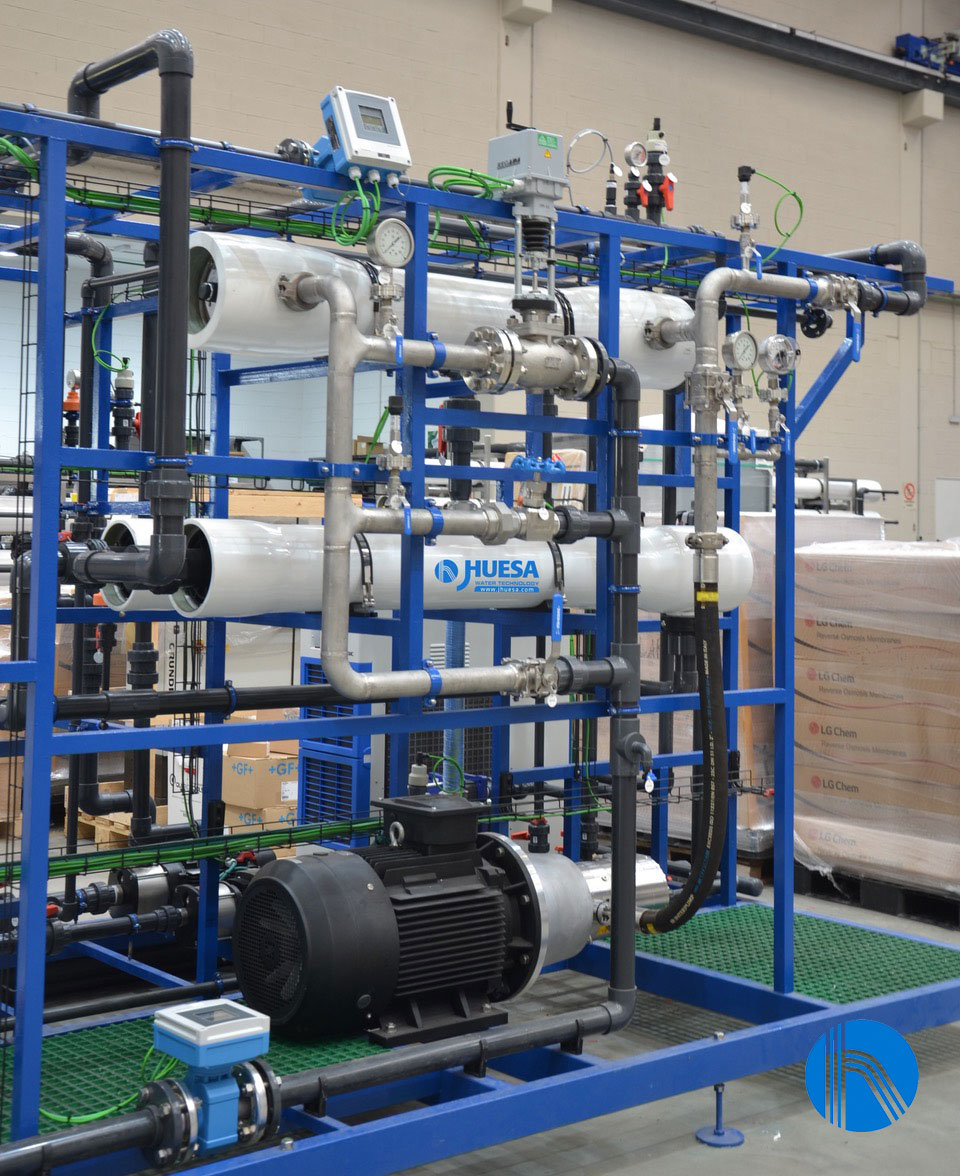
Detalle carcasas ósmosis inversa
Sistema CIP
En esta planta, la limpieza CIP y el lavado se realizan automáticamente mediante configuración por pantalla, activándose manualmente por parte del operador.
Para ello se recomienda realizar un proceso inicial de enjuague con agua de red recirculando durante un tiempo y verter a desagüe, para luego volver a llenar el depósito
y realizar la limpieza química del sistema adicionando los químicos necesarios para este propósito.
La bomba de alta presión no suele utilizarse durante estos procesos, y se suministra con una válvula
de lavado integrada que permite que el fluido fluya de la entrada a la salida, cuando la bomba no está
en marcha.
Instrumentación y control
La planta piloto está provista de elementos de instrumentación y control (válvulas automáticas,
presostatos, transmisores de presión, caudalímetros, medidores de conductividad y pH…) que se
centralizan en un cuadro eléctrico de control diseñado por el equipo de Instrumentación y Control de J. Huesa para integrar todas estas señales.
Así mismo, el cuadro incluye un autómata lógico programable y una pantalla táctil para el manejo y
configuración de la planta, lo que permite establecer parámetros de operación y monitorizar la planta en tiempo real.
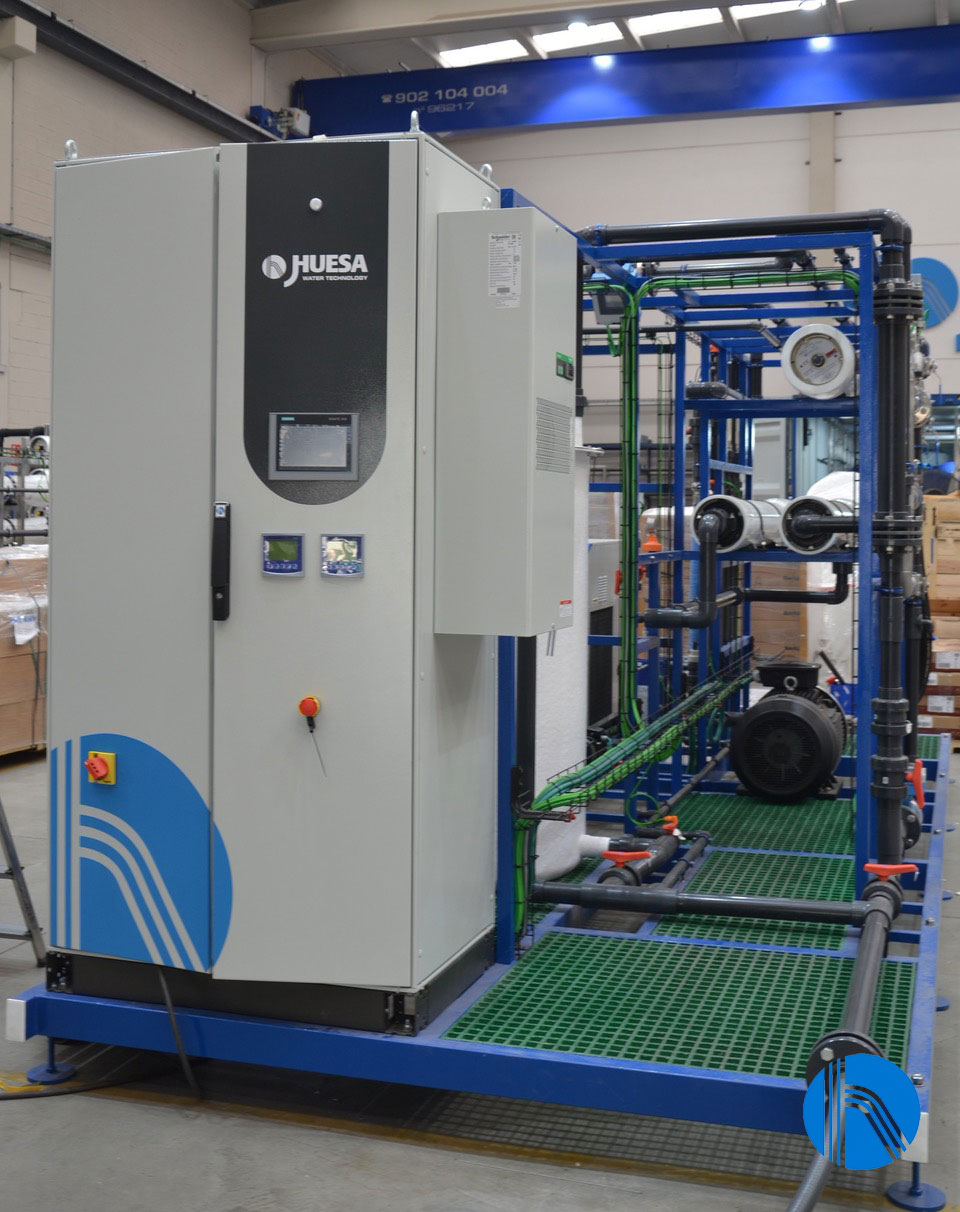
Detalle cuadro eléctrico