One of the main assets of J. Huesa Water Technology as a company that covers the Integral Water Cycle, is the After Sales Department which is integrated by a team of professionals with extensive experience in the sector that guarantees the best solution from the technical, economic and environmental point of view.
In this post we are going to focus on the role played by the experience of the water treatment technician to be able to solve in the best possible way the incidents that occur in water treatment plants and more specifically those that have, among their main components, membranes.
Membranes are semi-permeable barriers that restrict the passage of certain substances depending on their molecular cross section and/or the technology in which they are integrated. Basically we are talking about membranes of nanofiltration, microfiltration, ultrafiltration and reverse osmosis equipment.
It should also be borne in mind that there are a multitude of membranes on the market, both in terms of the material of which they are composed (polyamides, cellulose acetate, PVDF and polysulfones, among others) and the configuration in which they are arranged. Thus, for example, in the case of ultrafiltration, we find hollow fiber, tubular and ceramic membranes, and for reverse osmosis, the most common configurations are spiral, disc and vibrating.
All these water treatment technologies have in common the need to apply a correct pretreatment, specific in each case according to the type of water or wastewater to be treated, as well as a correct preventive and, if necessary, corrective maintenance. This will maximize the useful life and efficiency of the water treatment systems.
Preventive maintenance is understood as the periodical revision to which the water treatment installation must be submitted, so that it works offering the best quality indexes. Hence it is planned to follow a maintenance plan that is adapted to the requirements of each installation, according to a schedule of visits and minimum actions to be performed, among which we can find:
- Visual inspection of the installation and the operating sequence
- Verification of operating parameters
- Calibration and verification of analyzers and control instrumentation
- Checking the condition of consumables and replacement if necessary
- Data collection and plant standardization data
In this type of actions are usually detected needs of the installation, either plant adjustments, reprogramming in the operating sequences, or as in the case in which we focus today, is motivated by the malfunction of the membranes
Corrective maintenance takes place either when any electromechanical anomaly is detected in a water treatment plant or when there is a deviation of the operating values and parameters from the design values. All this usually leads to a production stoppage or loss of efficiency of the installation.
The fact of having a preventive maintenance, in which different ranges of maintenance, plant standardization data, allow us to check deviations from design values, to avoid production stoppage and plan a corrective maintenance, avoiding major damage such as loss of membranes.
In both cases, it is essential to give a quick response to the customer to shorten downtime, for which the qualification of the maintenance technician is essential.
Causes for membrane cleaning or membrane replacement
In this specific case we are going to focus on the case of reverse osmosis membranes, but in general terms it can be extended to any other type of membranes.
Reverse osmosis membranes favor the passage of molecules from the less concentrated to the more concentrated region. This causes various problems, such as fouling, scaling and membrane degradation.
Different types of fouling:
- Biofilm fouling
- Colloidal fouling
- Organic fouling
- Salt fouling
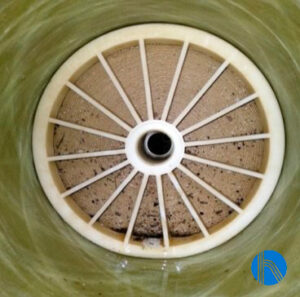
Detail of membrane with fouling
For each of these types of fouling or scaling, J. Huesa has specific and customized cleaning protocols developed based on our experience in the sector.
Some of the symptoms of a reverse osmosis plant with “dirty membranes” are:
- Decreased permeate flux
- High pressure differentials
- Loss of salt retention performance (reverse osmosis)
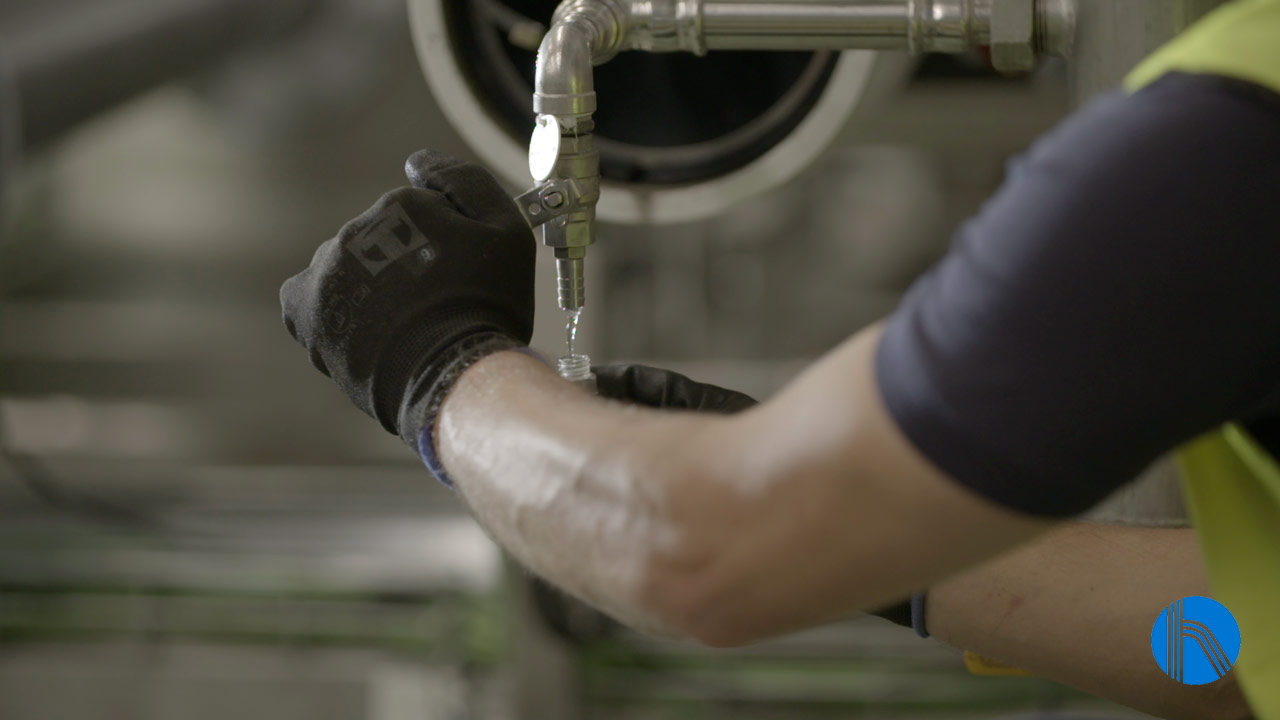
Detail of osmosis permeate water inlet
All these symptoms ultimately lead to performance losses in water treatment equipment, generating cost overruns in their operation or even prolonged production stoppages.
Solutions to improve the performance of a membrane water treatment plant
Our technical after-sales service will evaluate, according to the data collected within the range of maintenance, check lists, plant normalization data and various follow-up analyses and actions:
- Feed water studies: complete analysis, Jar – Test, SDI and membrane autopsy
- SDI and SDI Membrane Autopsy
- Membrane cartridge autopsy
- Membrane screening with specific software
- Projection of chemical dosage based on studies performe
Based on the results obtained and the monitoring of the plant, the After Sales technical team will prepare a report that will conclude with a decision, which will provide the best solution from the technical, economic, and environmental point of view, depending on the real situation in which the water treatment plant is.
And so, we find ourselves with this battery of possible solutions:
- Re-engineering of the water treatment plant, redefining treatment flow rates, dosages and even an adequate pre-treatment of the reverse osmosis line.
- Load changes of the filtration system prior to reverse osmosis
- Optimization of the dosages of plant chemicals (biocide, antiscalant, and sequestrant). This action is possible when it is confirmed that the misuse of chemicals is the cause of production stops and that the membranes are in good condition
- Chemical cleaning of the membranes in cases where it is confirmed that the membranes have fouling that can be removed by applying different cleaning protocols that ensure a recovery of more than 80 %
- Replacement of membranes in cases where fouling has caused such porosity that the permeate obtained is characterized by high conductivity, making its recovery unfeasible.
- Membrane autopsy. This action is left in last place because it involves, among other things, the loss of the membrane to be treated. This resource is used to find out with greater accuracy what is the exact cause of the malfunction of a water treatment facility that has many membranes
For all the above mentioned in this text, we insist on the importance of having a qualified after-sales service that can give a quick and adequate response to each of the situations encountered by the water treatment plants of the different industries.