On this occasion, a leading company in the production of cleaning products, detergents, capsules, and personal hygiene products has entrusted the services of J. Huesa for the treatment of effluents from production, specifically to complete the existing purification system in the factory.
To go more in depth in this sense, we will now give a background of the starting situation, since the mainstream presented high COD, A&G and SS contents that negatively affected the O&M of the existing treatment line.
To respond to this problem and taking into account that this sector has increasingly demanding requirements, the technical team proposed the installation of a pre-treatment system consisting of a tubular ultrafiltration capable of eliminating practically all the AG and SS, while at the same time significantly reducing the COD load entering the existing treatment line. To corroborate the suitability of this solution, in an initial stage of the project, a pilot test was carried out in the laboratory of J. Huesa.
Laboratory piloting
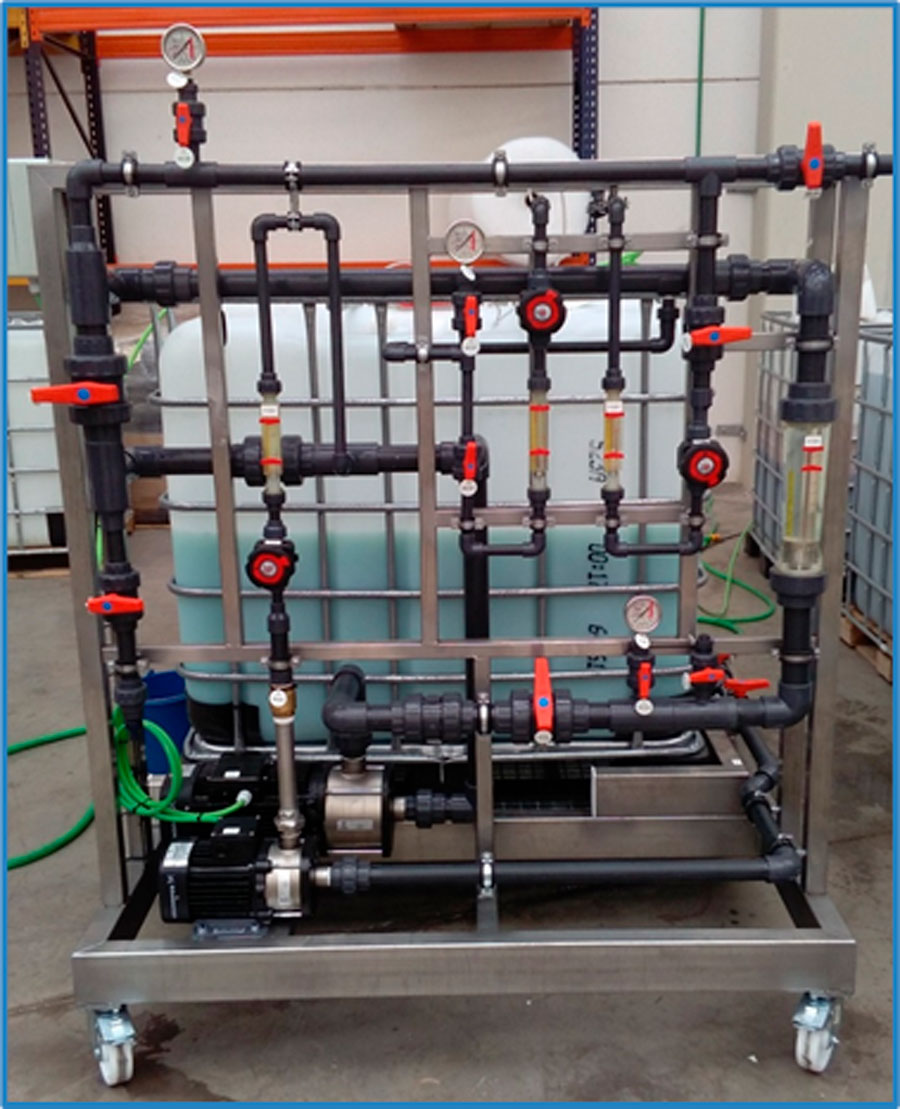
Detail of tubular UF pilot plant
This pilot project was carried out in two phases, initially several ultrafiltration membrane modules were tested to choose the appropriate model to be included in the final plant. For this purpose, different modules were tested at a crossflow velocity of 4m/s, until concentration values of maximum 16.7 at the design flux suitable for an industrial solution were reached.
From this factor, the flux decrease dropped drastically, and abundant foam formation occurred, affecting the recirculation of the system. In addition, the almost total elimination of SS and A&G and a drastic reduction of COD in the ultrafiltered water obtained were verified.
In a second stage, a pilot unit was manufactured with a MO P1 (1,2 mm) 66.03 PVDF 18, consisting of an IBC for concentration pond and a 200-litre treated water tank, in order to verify the behaviour of the solution in a plant similar to the industrial solution, as well as to evaluate the performance over a longer period of time than in the initial test.
The objectives set for this plant were as follows:
- Under initial filtration conditions:
- To verify the removal of A&G and SS in the filtrate obtained
- To verify the COD removal performance of the filtrate obtained
- To reach a concentration factor of approx. 10, and work for a week in stationary design conditions to evaluate:
- If the quality of the filtrate maintains the performance levels in A&G, SS and COD
- Effect of one week operation on TMP and flux
Since the customer’s raw water contains water from different streams in the proportions normally used in the production process, a specific analysis of the permeate quality was carried out for each of the streams individually, with the same objectives as in the previous case.
Once the pilot plant was set up, the piloting was carried out in three different phases:
- Phase 1: concentration of the raw water in order to bring the feed pond to the same conditions as the industrial plant. This phase took place for 4 weeks, 24 hours a day.
- Phase 2: stationary piloting under conditions like the industrial process. This phase was carried out for three weeks, 24 hours a day.
- Phase 3: spot test with CIP water samples, 24 hours a day for two days.
The conclusions obtained in both cases are detailed below:
- Both SS and H&G were practically retained in the tested ultrafiltration and under conditions like the industrial design.
- The average COD removal in this test during the stationary phase was 70 %, which implies that the organic matter load will be significantly reduced.
- The transmembrane pressure and pressure differential across the UF membrane did not indicate any need for cleaning or premature clogging during the pilot run.
Solution installed
As a conclusion of the pilot study carried out, it was decided to implement an ultrafiltration system, which is a membrane separation system under controlled pressure that generates a permeate free of SS, bacteria, and viruses.
As a brief presentation of this technology, it can be said that there are two types of membrane modules: Dead-end and crossflow. The latter can be either an inside-out or an outside-in system.
Due to the conditions of the process and the water to be treated, as well as being the only system that guarantees control of fouling and clogging of the membranes, the type of UF to be used will be an inside-out crossflow system with a capacity to produce 15 m3/hour of permeate.
Since the permeate obtained in the ultrafiltration will be the input to the existing treatment line, a batch-type plant has been set up, so that its operation is regulated according to the level of this existing treatment line.
All the system’s operation is controlled from the electrical panel, where the automaton that governs the installation is located, as well as the touch screen on which the different operating variables are displayed and parameterised.
Treatment System
The water to be treated is stored in a 30 m3 capacity truncated cone-shaped GRP tank from which the water is pumped by means of a 50 m3 /hour capacity pump. A battery of two self-cleaning ring filters will be placed on the impulsion line itself, prior to the tank inlet, which have the capacity to retain the larger particles that may come with the raw water.
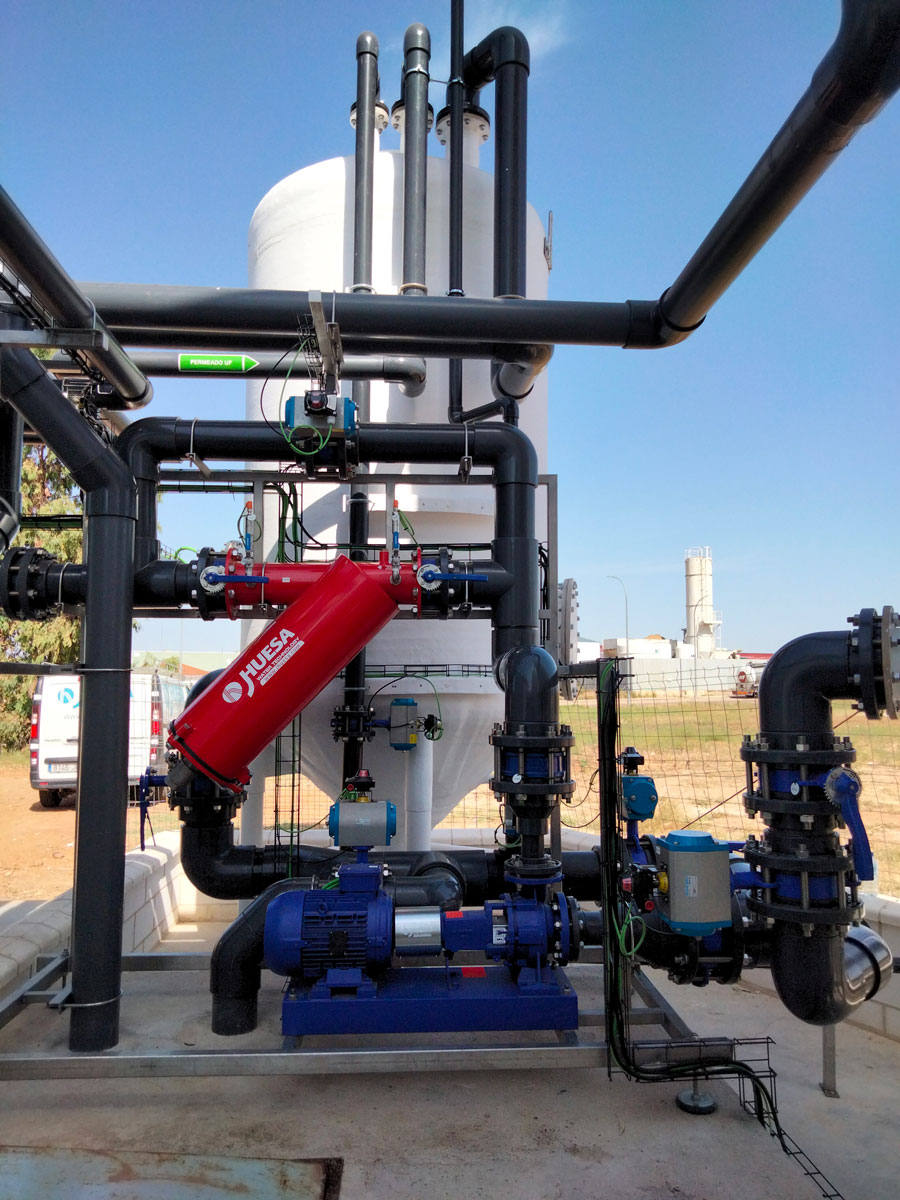
Mesh filter detail
The pumped water passes through a mesh filter with a pore size of 150 microns. This is followed by the 90-kW recirculation pump. This pump supplies the water to be treated to the ultrafiltration modules.
This pump moves both the water driven by the feed pump and the ultrafiltration concentrate recirculation itself, with a flow rate of up to 400 m3/h
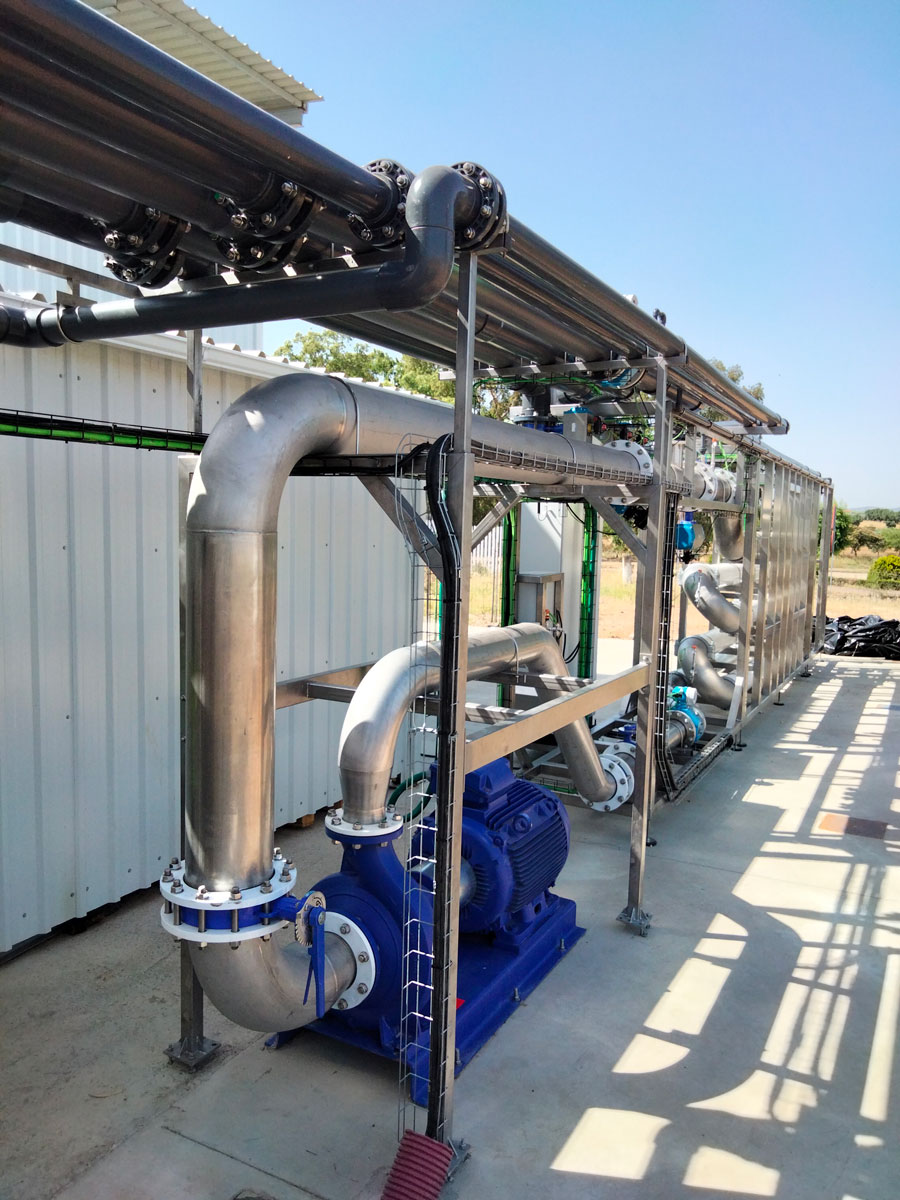
Detail of the impulsion pump
Ultrafiltration Skid
The ultrafiltration plant has 5 modules composed of PVDF membranes with a pore size of 30 nm. The dimensions of each module are 4 m and 10″ in diameter. In addition, after the 5 modules, the plant has a 10″ stainless steel pipe which serves as a reserve for possible expansion of the plant. This pipe is known as a « dummy ».
In the inlet line to the UF skid, as well as at the outlet of each module, we find a series of analytical instrumentation with the aim of always parameterising the conditions of the plant, specifically:
- Flow meters
- Temperature transmitters
- Pressure transmitters
After the ultrafiltration modules, the concentrate returns through a 10″ stainless steel line to the suction of the recirculation pump.
On the outside of each module is the permeate outlet, made of PVC-U by means of a 2 ½ » vitaulic connection to the module. On the permeate side of each module there is a sight glass that allows the permeate obtained to be inspected visually and to detect possible pore breakage if turbidity is observed. This part also has instrumentation to measure parameters such as transmembrane pressure or TMP and dP.
In addition, each permeate line has an adjustable single acting pneumatic valve. These valves allow partial openings of each permeate line and their main purpose is to equalise the TMPs of each module as much as possible.
Flushing
In a UF plant it is necessary to move the main discharge from the membranes once the process is stopped. In this way, we ensure that the membranes are « soaked » with clean liquid, such as osmosis water, mains water, or even the plant’s own permeate. On this occasion, after several pilot studies in the laboratory, it was decided to use the UF’s own permeate water as flushing water.
Flushing is also used in the filtration stage as a preventive measure against possible clogging of the membrane pores and recovery of membrane performance. Flushing is also often used prior to the start of filtration, with the aim of ensuring the total displacement of the effluent prior to the start of filtration.
To be able to flush the plant when it is shut down, a 5 m3 truncated cone-shaped GRP tank has been included in the system, from which the feed pump sucks in ultrafiltered water and introduces it into the plant. The rest of the permeate is collected in two 40 m3 GRP tanks that collect the inlet water from the factory’s existing treatment line.
Cleaning (CIP)
The chemical cleaning or CIP mode is a mode that comes into play when the performance of the membrane has decreased due to fouling. In order to know this drop in performance, it is important to monitor the following parameters:
- Permeate flow rate
- Pressure drop in each module (dP)
- Transmembrane pressure (TMP)
- Energy consumption