J. Huesa successfully completes the commissioning of a water treatment plant in an industry dedicated
to the manufacture of personal hygiene products.
On this occasion, our client, a leading company in its sector, has relied on us to improve the quality of
the feed water to its production process.
Adopted solution
Once the raw water samples taken at different points of the production process were analysed, we
concluded that they had a high content of salts, organic matter and suspended solids.
At this point, the technical department of J. Huesa opted for the design and manufacture, customised,
installation and commissioning of a water treatment plant using reverse osmosis as the central element,
whose objective is to clarify and desalinate the water and reduce the colloid content present in it, improving the quality
of the feed water and reducing operating costs.
Filtration flow rate | 25,7 m3 /h |
Backwash flow rate | 40-50 m3 /h |
Flow rate RO | 25,7 m3 /h |
RO permeate flow | 18,0 m3 /h |
Conversion | 70 % |
Working hours | 24 h/day |
Total daily production flow | 432 m3 /day |
Used of treated water | Raw material |
Pretreatment
The raw water to be treated is stored in an accumulation tank from which it is pumped to the pretreatment room.
Ring Filtration
In an initial stage of the pre-treatment and to make easier the elimination of solids in the filtration stage,
the raw water passes through a static mixer in which flocculant and sodium hypochlorite are injected, in such a way as to guarantee the necessary contact time between the chemical and the water to be treated. This sub-process allows
the formation of flocs of the appropriate size.
The water then passes through a double-stage ring filtration system that removes the flocs formed in
the mixer:
- Stage 1: two 200-micron ring bells in parallel.
- Stage 2: three 50-micron ring bells in parallel.
This filter battery is equipped with a controller and automatic cleaning, which is started either by time
in service hours and/or pressure difference detected between inlet and outlet, starting the cleaning
sequence of each of the filtration hoods. These are cleaned individually one after the other. For cleaning,
the water accumulated in the boiler is used, while previously filtered and dried compressed air is
injected. While one hood is being cleaned, the others are kept in operation.

Pre-treatment room view: mixer and ring filter system
Zeolites Filter
Working in series with the ring filter, and to adjust the turbidity of the water (removal of finer solids), the system has a fixed bed filter of porous solids. This filter has a system of independent valves to carry out the washing operation of its load. The operation of the valves is automatic and is managed by the automaton located in the control panel included in the reverse osmosis system container.
Specifically, there is a glass fibre reinforced polyester (GRP) filter with a diameter of 1800 mm. As soon
as this filter requests cleaning, due to time in service hours and/or pressure difference detected
between inlet and outlet, production is interrupted. This cleaning process consists of two stages:
- Backwashing: for cleaning the load, using the same water used in service and the same
pumping system. The duration of this phase can be modified, and the water used is sent
to the drain. - Settling: necessary to prepare the load for the return to service of the filter. As in the
previous phase, its duration can be modified, and the water used is sent to the drain.
This cleaning process is carried out by time and/or by maximum pressure loss in the water line between
the inlet and outlet. Both parameters are modifiable on the screen. Once cleaning is requested,
production is stopped. Once this process is finished, production is resumed.
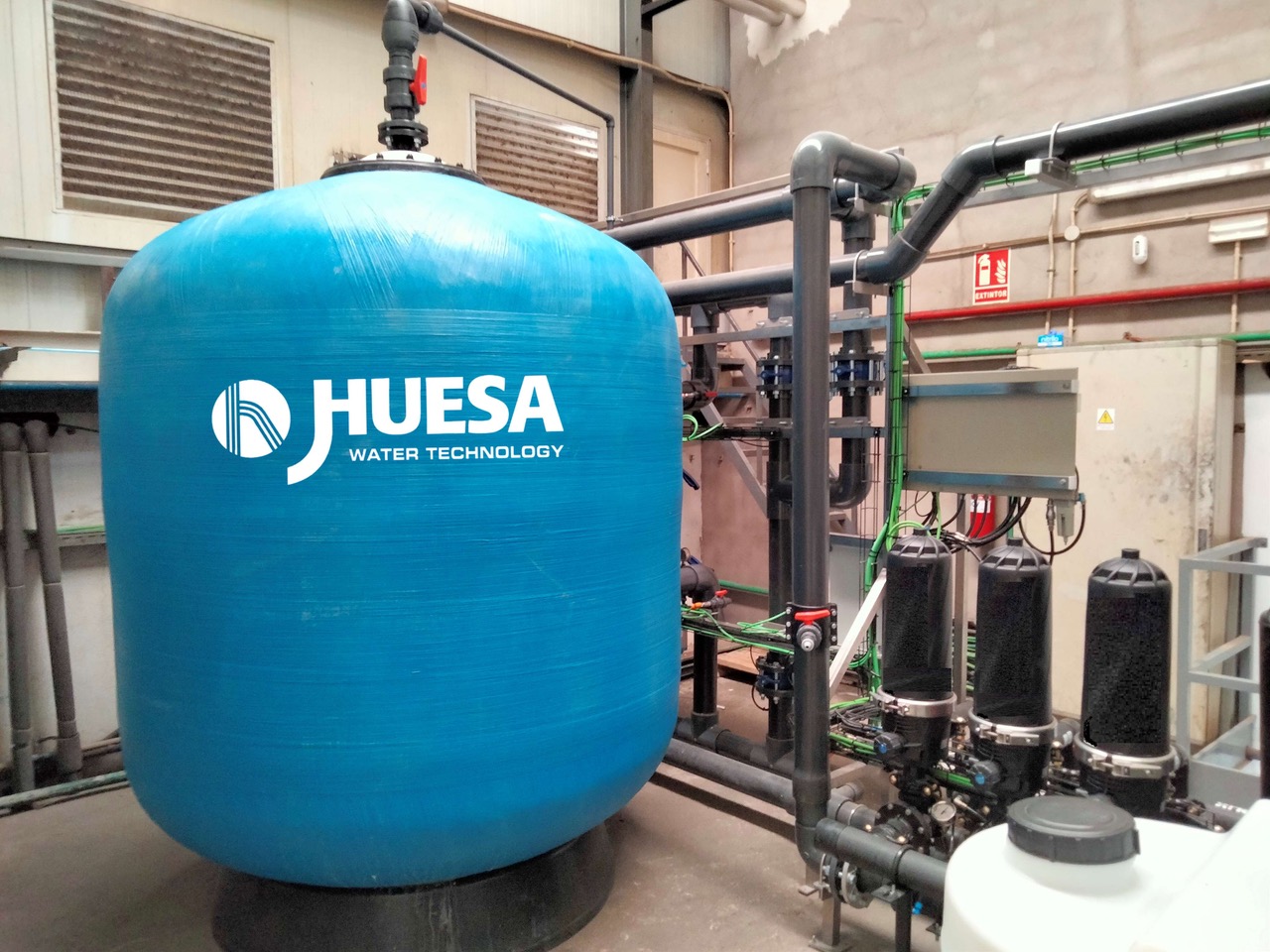
Sand filter system
Reverse Osmosis
The water then passes into the container in which the reverse osmosis system is located.
The pre-treated water passes to reverse osmosis which is preceded by the following sub-processes:
Chemical dosing system
The following chemicals are used:
- Antiscalant: which prevents the appearance of saline scale on the membranes, improving
the operation of the system in terms of flow rate. - Sequestrant: to reduce the free chlorine in the water formed by the addition of
hypochlorite during pre-treatment.
Safety pre-filter
The pre-treated water passes to the reverse osmosis module, where it is first filtered through 5 micron
pore size cartridges that will retain possible leaks of very small particles (suspended solids and colloids).
The safety filter consists of replaceable 5-micron cartridges, which are managed by means of a pressure
difference measured by two pressure gauges placed at the inlet and outlet of the filter.
Reverse Osmosis
Once the water is ready, it is pumped by means of a vertical, in-line, high-pressure centrifugal pump in stainless steel AISI
316 with a capacity of 25.7 m3/h.
The reverse osmosis system is configured in a single stage, consisting of five pressure tubes each
containing five membranes, achieving a conversion rate of around 75 %.
The installation is fitted with spiral wound membranes, made of polyamide and specially designed for
brackish water up to 8000 ppm and with the characteristic of working at low pressure.
Membrane cleaning equipment
All membrane installations become fouled over time, depending to a greater or lesser extent on the pretreatment installed, requiring one to two chemical cleanings per year. The reverse osmosis plant includes a membrane washing system consisting of a reagent preparation tank, stainless steel recirculation pump and stainless-steel stage isolation and recirculation valves. The filling of this tank is automatic thanks to a float valve connected to the same osmosis water line.
Instrumentation and control
The reverse osmosis plant is equipped with instrumentation and control elements (automatic valves,
pressure switches, pressure transmitters, flow meters, conductivity and Redox, etc.) which are
centralised in an electrical panel located in the container.
The panel also includes a programmable logic controller and a touch screen for the operation and
configuration of the plant. J. Huesa’s Instrumentation and Control team has designed the control panel
so that it can be integrated in the client’s SCADA system, allowing a customized programming of all the
operating parameters, as well as external connections of levels, alarms, pre-treatment, among others,
through different I/O modules.

Electric control panel