J. Huesa successfully completes the commissioning of a water treatment installation for a Spanish multinational leader in the manufacture and distribution of innovative and sustainable surfaces for architecture and design of recognized prestige worldwide.
Our client is a company committed to the Environment and the Integral Water Cycle, which is immersed in a continuous process of expansion and improvement of its facilities. For that reason, has been needed to incorporate a new water treatment plant to obtain certain quality water which use of will intend for a new production line of ultra-compact surfaces.
Once the analytical parameters of the inlet water and the requirements of the company were known, the technical team of J. Huesa together with the specialist team of our client got down to work to study and design a tailor-made solution to obtain the water necessary for their production process.
Data and water properties
Main target of the water treatment plant is obtaining an excellent quality water in terms of conductivity (conductivity values obtained below of 100µS/cm) and organic matter.
The starting data are as follows:
Flow rate for treatment | 2 x 28, 6 m3/h |
RO permeate flow rate | 2 x 20 m3/h |
Reject flow rate RO | 2 x 8,56 m3/h |
Conversion | 70% |
Water source | Mains water |
Used of treated water | Raw material |
Required water flow rate | 2 x 20 m3/h |
Adopted solution
Considering values of conductivity required by the client as well as environmental engagement of the company, it has been decided to design two treatments lines composed each by double-stage reverse osmosis plant.
Each of the lines is composed of the following sub-processes:
Pretreatment
At the first stage, water from raw water tank is pumping to two-layer filtration system composed by two bottles which enable to filtrate a flow rate of 30 m3/h. Each bottle is loaded with different sizes of silex.
System not only works with one filter in reserve and the other one in service but also both can operate at the same time.
Filtration system is able to work carrying out the clean of the system which it has been taken into account once per day (at night) and, also considering pressure drops in the system (value of 25 m3/h backwashing speed has been considered).
Inlet water which is pumped and filtrated by two-layer filter mentioned, enters a cartridge-holder filter made of PVC with polypropylene wound cartridges to retain any leaks of suspended particles that may be contained in the water and then passes to the reverse osmosis modules.
Filter is composed by replaceable 1μm cartridge which is controlled by pressure drops in the system measured by pressure gauges that it has been installed at the inlet and outlet of the filter.
The frequency of cartridge replacement depends on the colloid content of the water.
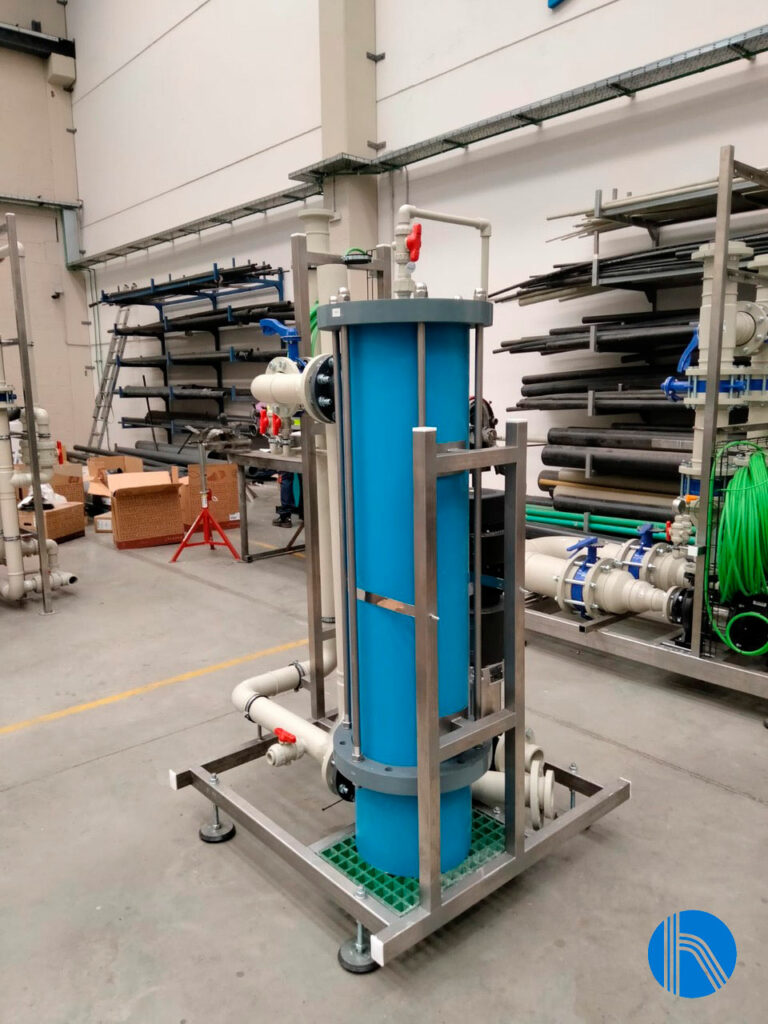
Cartridge filter detail
Reverse Osmosis System
Treated water is then pumped to the reverse osmosis system by the action of a high-pressure vertical pump made of AISI 316 stainless steel, which guarantees the operating pressure and allows the production flow rate required. Its function is maintaining a constant inlet pressure at the osmosis system, using a control loop composed by a pressure transmitter and frequency driver.
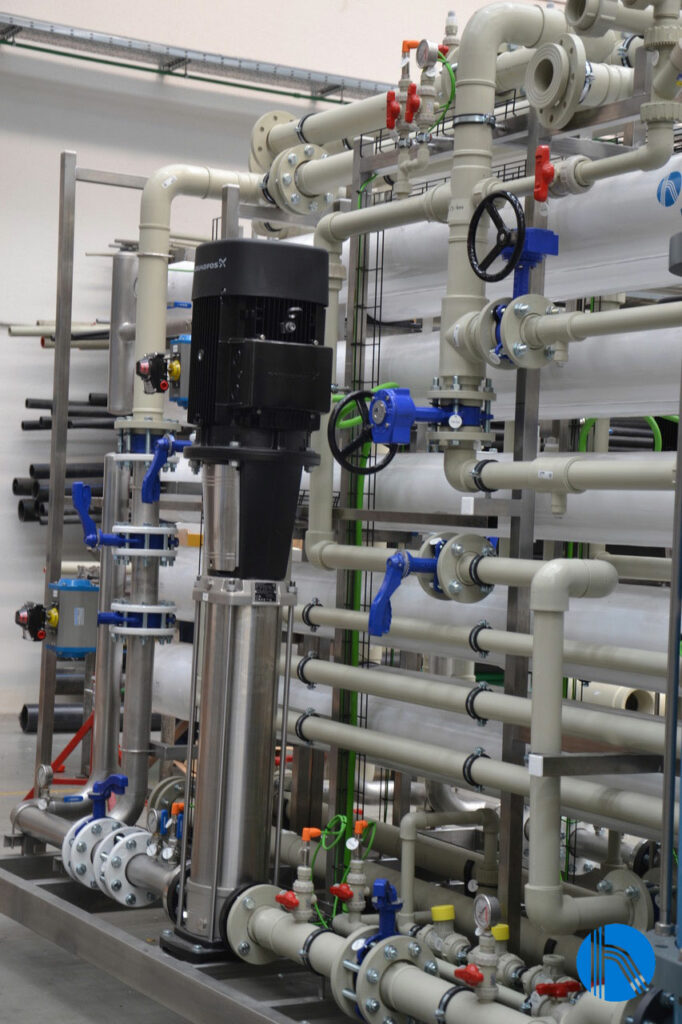
Detail of high-pressure satinless steel pump
Reverse osmosis system is composed by two stages, considering 3-2 configuration with water recovery rate nearly to 70% and input flow rate of 28.6 m3/h obtaining a permeate flow of 20 m3/h. Installation is equipped with spiral wound membranes, made of polyamide, and specially designed for brackish water up to 8000 ppm and working particularity at low pressure. They are installed in pressure housings, made of coiled GRP.
These membranes have a high chemical resistance, as they can work in a pH range of 2 to 13, which make them easily to wash and enable to obtain better recovery values due to the fact that able to work with a wide variety of washing chemicals.
All the reverse osmosis equipment are installed on AISI 304 stainless steel skid.
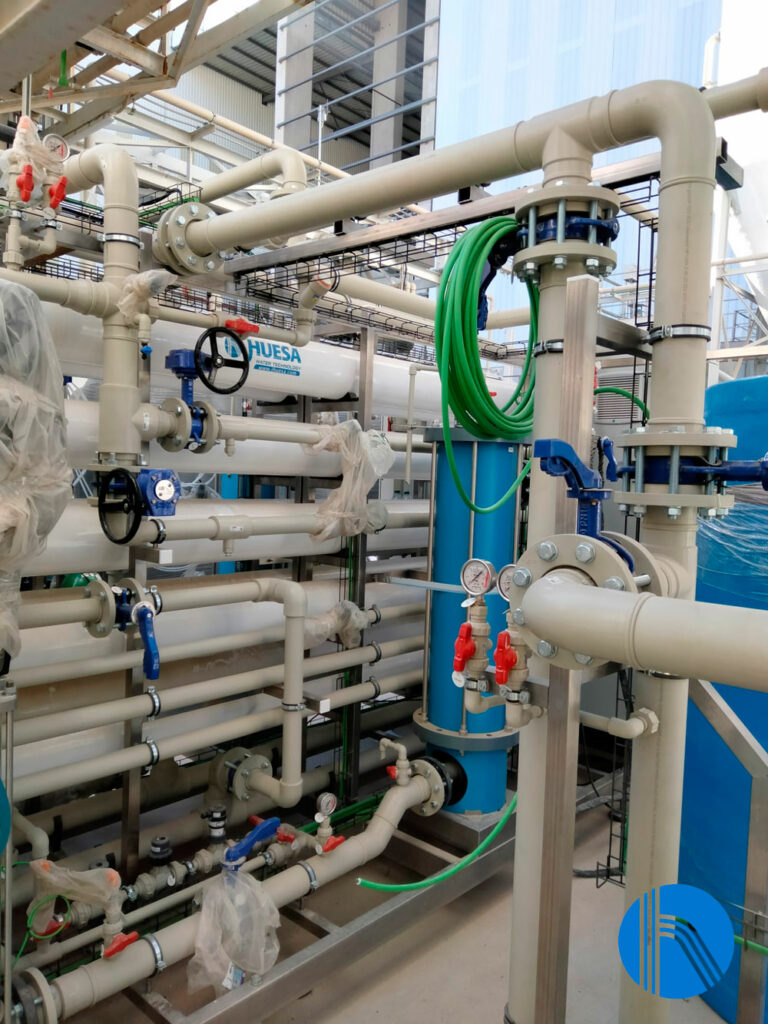
Detail of RO skid during installation
Membrane cleaning equipment
Flushing system installed ensures to making an automatic cleaning of the membranes installed inside the pressure vessels. It must be considered that this system is common to both reverse osmosis line because each cleaning is going to carry out one by one. Cleanings must be programmed from touch screen considering operators needs and plant stops.
System is equipped with a pump whose impeller and jacket are made of AISI316 which are able to work with most of chemicals used to recover properties of the membranes. Water will be sucked from a 2m3 osmotised water tank in which mix of chemical products will be diluted.
Rejected flow from reverse osmosis process (8.6 m3/H) is fed to an intermediate tank of 100 m3. Client must manage it in another area so that no discharges are produced.
Instrumentation and control
The reverse osmosis plant is equipped with instrumentation and control elements (automatic valves, pressure switches, pressure transmitters, flow meters, conductivity, and pH meters…) which communicate with the programmable logic controller, included in the control panel, through IO-Link technology.
The control panel also includes a touch screen for the operation and configuration of the plant. J. Huesa’s Instrumentation and Control team have designed the control panel so that it can be integrated into the customer’s SCADA system. It also includes a remote control system.
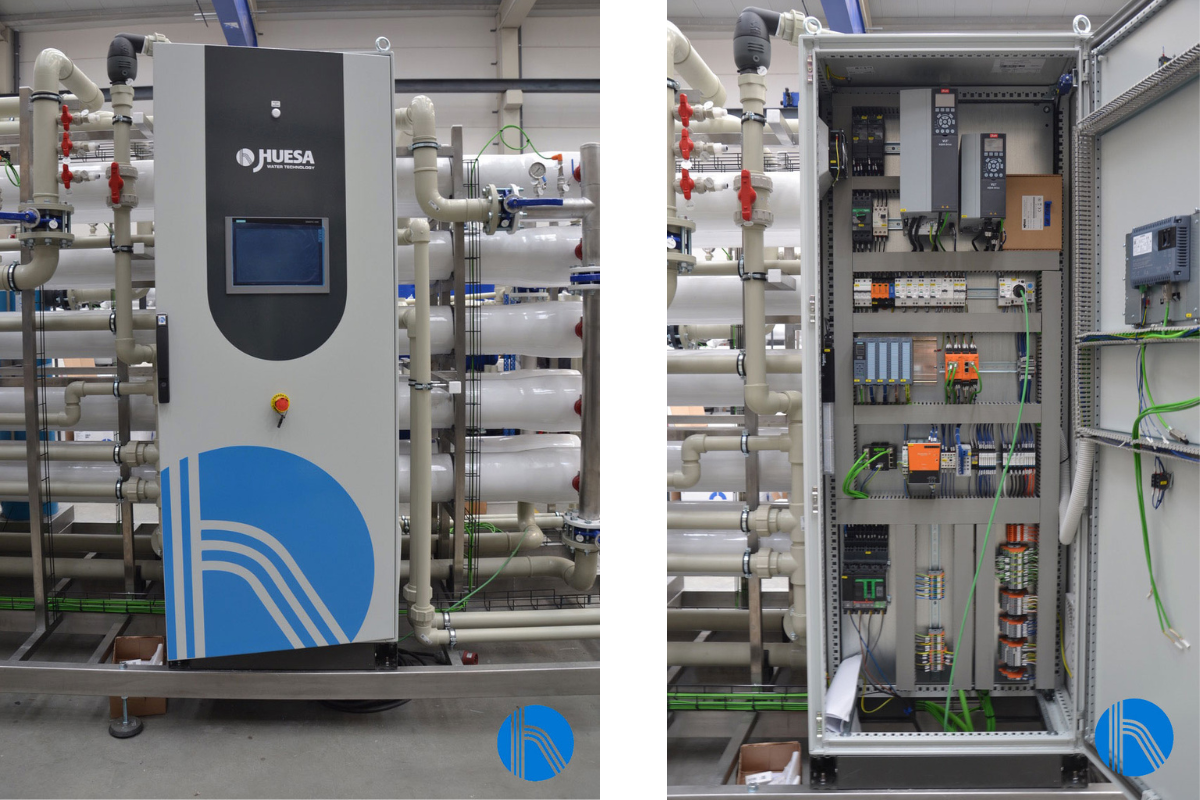
Interior and exterior detail of the electrical panel
Environmental impact
The key of the success of this project is due, on the one hand, to the experience of J. Huesa in the sector that concerns us and, on the other hand and more importantly, to the close customer-supplier collaboration that has made it possible to achieve the objective of quality and water consumption required at a technical level.
Likewise, from an environmental point of view, goal of integrating this solution into the Zero Dumping policy that the client has already had for years has been achieved.
In addition, a reverse osmosis system has been chosen, which has the following additional advantages, among others:
- System works continuously, without needed of regeneration, avoiding consumption of products that are difficult to handle such as caustic soda. In that case we have a specific consumption of hydrochloric acid to adjust pH at the system inlet.
- System is fully automatic and can work up to 24 hours a day, with minimum supervision. It does not require specially qualified personnel.
- Due to semi-permeable properties membranes, reverse osmosis system is a kind of bacteriological barrier for water obtained which remove bacteriological problems in the installation. Sanitation of membrane is considered in previously design of the equipment and means a daily operation that can be repeated over time.
- No toxic, hazardous or environmentally polluting discharges are produced.
- Expendable products are scarce